Making the Circular Economy a Reality
Driven by brand owner demands and new worldwide legislation, the entire supply chain is working toward the shift to circularity, with some evidence the circular economy has already begun.
Sometimes change is big and you know right away, while other times change comes in smaller actions that will build up to a larger one. For instance, you purchase a reusable water bottle and see it’s now being made with Eastman Chemical’s Tritan Renew, which utilizes 50% recycled material.
Eastman is scheduled to start up what it calls the world’s largest molecular recycling facility in Kingsport, Tennessee. It will have capacity to divert annually more than 220,000 tons of “hard-to recycle” plastic waste from landfill and transform it into a variety of virgin-quality polymers.
“Circularity is about redesigning a value chain beginning to end and back to beginning,” says Scott Ballard, president of Eastman’s Plastics Division. “No one company or even industry can do it alone.
“Partnerships are needed not just with customers and suppliers but across different parts of society. Change is needed in regulations and policy, polymer technology, product design, consumer behavior, waste management, etc. — and all the change needs to be coordinated in a way that enables innovation.”
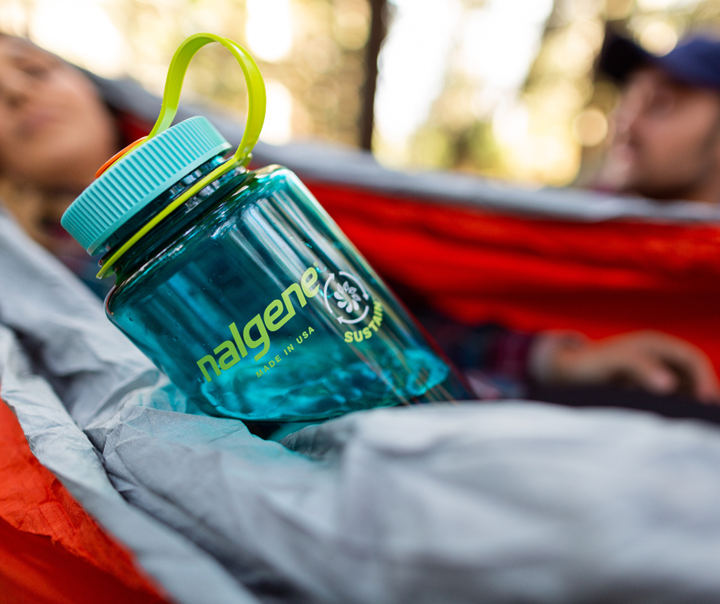
The Nalgene brand introduced reusable water bottles made from Eastman Chemical’s Tritan Renew material, which features 50% recycled content. Photo Credit: Eastman
Egor Dementev, senior analyst, plastics recycling at chemical and commodity consultant ICIS, says the circular economy has been one of the most powerful megatrends affecting the plastics industry over the last few years and is widely anticipated to keep building momentum in the future.
Despite a challenging 2023, Dementev wrote that production of mechanically recycled polymers is forecast to experience relatively strong growth supported by continuing consumer pressure, voluntary pledges and new legislation across the globe. For instance, the European Union has a plastics strategy which states that by 2030 all plastic packaging should be designed to be recyclable or reusable.
Many brands are targeting 2030 as the year to shift to a circular business model, and incorporating more recycled content and reusability across major product lines and packaging applications. But brand owners can’t achieve this alone — and that’s where the entire supply chain comes into play.
Adidas’ Circularity Ambitions
Adidas is one of the most recognizable brands in the world. The company has a long history of sustainable business practices, including creating products with recycled content, as well as promoting circularity and looking for ways to prolong the life of its products.
An Adidas spokesperson tells Plastics Technology that the company has steadily increased the amount of recycled and sustainable materials in its product range since 2015 when the company launched the first Adidas x Parley running shoe with recycled plastic waste from beaches and coastal regions.
“From there, we set an ambitious goal of using only recycled polyester by 2024, which we are on track to meet by the end of 2023 — one year ahead of schedule,” the spokesperson says. “This makes Adidas a pioneer when it comes to sustainability, as the share of recycled polyester worldwide is currently around 15%.”
Circular economy approaches like this require the cooperation of companies along the entire value chain, the spokesperson explains.
“To that end, as part of the European Union's ‘T-Rex’ project, we are working with partners from industry and science to formulate requirements for the political framework, infrastructure and technologies of a circular economy,” the spokesperson says.
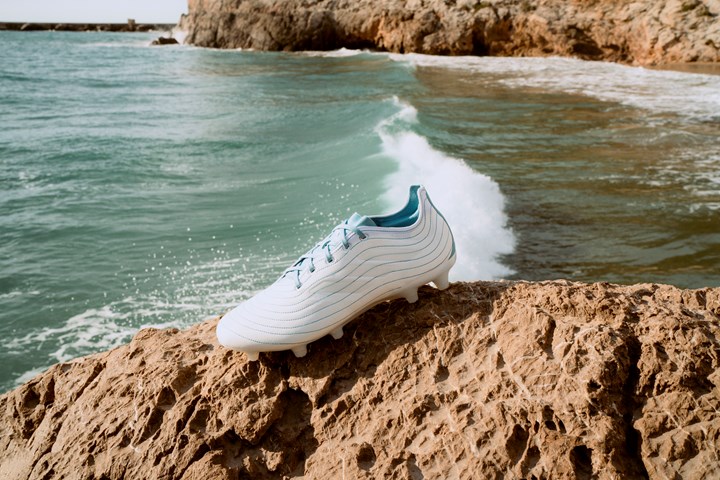
In 2023, Adidas launched the Parley Pack, its first football boot pack to be made in part with Parley Ocean Plastic. Photo Credit: Adidas
Borealis’ Sustainability Focus
Stephan Roest, head of the Circular Economy business development at Borealis, says the company is seeing an increasing demand for products with reduced environmental and climate impact, yet with no compromise in quality or performance.
“To meet these needs, we work closely with our value chain partners, including brand owners, to develop tailor-made circular solutions,” he says. “This includes a range of drop-in solutions that make it easy to switch to more sustainable feedstock without the need for investment in new processing equipment or for costly and time-consuming reapproval processes.”
For the packaging industry segment, Borealis recently launched a new monomaterial pouch containing more than 95% PP and designed for recycling. Developed in collaboration with value chain partners — including Mitsui Chemical Group, Jindal Films, Profol and Huhtamaki — this more sustainable high-barrier packaging format offers a range of benefits for the blown- and cast-film extrusion processes, as well as for brand owners and end consumers.
“It is imperative that we approach the circularity challenge in a holistic way, and that means working with our value chain partners and other value-aligned companies and industry associations to develop integrated, scalable solutions,” Roest says. “The shift toward circularity is not going to happen overnight — it’s a journey, and one we need to take on together.”
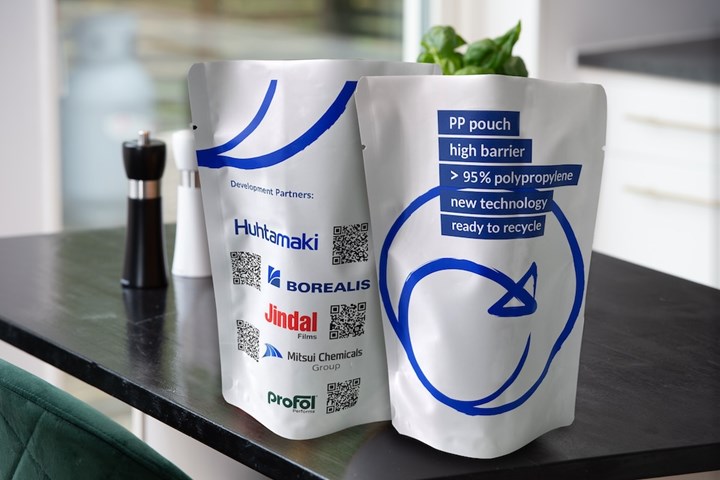
Borealis introduced a new PP monomaterial pouch that is fully compatible for mechanical recycling of polypropylene. Photo Credit: Borealis
Wittmann’s Take on Circularity and the Granulator Market
John DePasquale, product manager of material handling and auxiliaries for Wittmann USA, says developments in sustainability are happening rapidly. He sees a continued adoption of zero-waste goals further improving recycling infrastructure and leading to processors finding innovative ways to repurpose or include recycled materials.
“Over the last five years, Wittmann has seen growth in granulator demand,” DePasquale says. “Most of this is due to the financial benefit of utilizing scrap. Some is due to a shift in type of resins used in certain applications and, of course, the introduction of new models throughout this time frame with enhanced features and benefits.”
Beyond throughput and infeed or cutting chamber size, there has been an increase in concern for regrind quality. DePasquale says that customers are looking to reduce amount of dust and fines to both alleviate maintenance requirements as well as produce regrind with a more consistent size and shape to minimize processing variations.
“Following the trends, there is growing interest in postconsumer resin due to increased awareness of environmental sustainability,” he says. “Many industries were looking for ways to incorporate recycled materials into their products, and PCR is gaining popularity in the packaging, automotive and consumer goods sectors.”
Related Content
Magnetic Mold Clamping Amplifies Quick Mold Changes
NPE2024: Stäubli highlights its adaptable QMC123 technology, which is capable of calculating the clamping force for each mold beforehand, in addition to ensuring worker safety.
Read MoreBonding, Sintering Tech Advances Metal Bonding for Mold, Die Components
NPE2024: Punch Industry USA exhibits P-Bas, intended to replace the use of 3D printers when producing mold and die components, as well as a variety of mold component supplies.
Read MoreMold Repair, Design Solutions Serve Many Industries
NPE2024: Adler Industrial Solutions exhibits its selection of Pinnacle Molds and Rapid Mold solutions.
Read MoreLSR Platform Meets Critical Medical Molding Needs
NPE2024: Recent updates to Mastip’s Aquilo platform highlight how its design — from consistent thermal profile to uniform cooling — has made it successful for medical industry projects.
Read MoreRead Next
How to Solve Hot Runner Challenges When Molding with Bioresins
A review of the considerations and adaptations required to design hot runners and implement highly productive injection molding operations.
Read MoreMMT Chats: Common Sense Sustainability Initiatives
Sustainability can be as easy as recognizing the initiatives you already have in place for what their sustainability benefits are and putting numbers behind them, according to Kelly Santini, a passionate safety and sustainability advocate. Here, she chats with MoldMaking Technology Editorial Director Christina Fuges. This episode is brought to you by ISCAR with New Ideas for Machining Intelligently.
Read MorePlastics Industry Association Launches Recycling is Real Advocacy Campaign
The campaign will provide content that reflects the true efforts behind plastic recycling to help lead more informed decisions about sustainability and the circularity chain.
Read More