For the well-known consumer products company PepsiCo (maker of, among other brands, Pepsi-Cola), prototype blow molds are a vital resource for new product development. Max Rodriguez, senior manager of Global Packaging R&D, Advanced Engineering and Design at the company’s research center in Valhalla, New York, describes how a new bottle design must prove itself: “Our bottling lines run 600 to 800 bottles per minute, and there can be a lot of downtime if bottles are unstable. So, we look for optimal center of gravity and contact surface for line stability,” Then, the same bottles have to prove they work well in vending machines. Plus there is the blow molding process itself, and the need to work out the best molding parameters prior to full production. Because of all these factors, the chance to mold several hundred or thousand of a new bottle design for testing, then that many more when this design is inevitably tweaked, is crucial in bringing new packaging to market.
The impediment, of course, is the cost and time necessary for molds. Obtaining a prototype metal blow mold has traditionally entailed six weeks of lead time, at a cost of up to $10,000, according to Rodriguez and R&D packaging engineer Thangthip Tekanil, to whom I spoke for this story. For the PepsiCo team, making short-run blow molds through polymer additive manufacturing (AM) seemed to offer a faster and less expensive way to fill this need.
“Two significant developments have succeeded in realizing fast, effective, low-cost prototype blow molds via AM. One is a material advance and the other is an innovation patented by PepsiCo: a hybrid mold applying 3D printing strategically rather than using it to create the entire tool.”
Except it didn’t — not at first. Early 3D-printed blow molds made on various polymer additive platforms were capable of only around 200 samples before the tool failed; they couldn’t come close to doing the job the conventional tooling could. That was about four years ago, Rodriguez says.
More recently, two significant developments have succeeded in realizing fast, effective, low-cost prototype blow molds via AM. One is a material advance and the other is an innovation patented by PepsiCo: a hybrid mold applying 3D printing strategically rather than using it to create the entire tool.
These two innovations are now changing the way PepsiCo develops packaging. In place of six weeks, the PepsiCo team was recently able to obtain prototype tooling for a new bottle design in just 48 hours — tooling able to mold around 10,000 samples. And in place of $10,000, this AM-enabled tooling instead cost only about $350.
Photopolymer Backed by Stone
The advanced material used in this solution is xPEEK147 from Henkel Loctite. This polymer is “a big breakthrough,” Rodriguez says, a material that can be 3D printed quickly with high dimensional precision and the high-temperature strength for molding applications. Using a Nexa3D NXE 400 photopolymer 3D printer building with this material, the PepsiCo team can produce a complete mold set in about eight hours of 3D printing followed by four hours of curing.
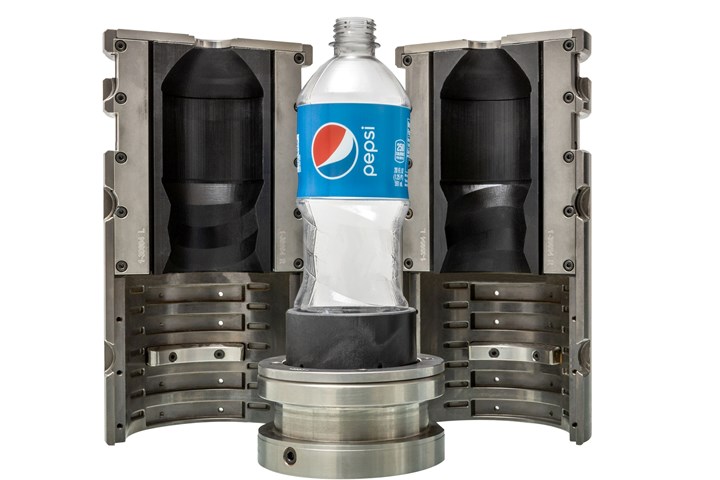
A 3D-printed mold set produced in about 12 hours mounts within a universal shell to complete the tool. Photo Credit: Nexa3D
The mold forms made this way capture only the bottle geometry, not the entire structure of the mold. PepsiCo’s innovation for prototype molding optimizes strength and reduces cost by containing the 3D-printed mold set within a universal metal mold shell that fits standard blow molding machines. The 3D-printed forms are backed by dental stone (gypsum used for dental dies) for strength and stability within this shell against molding pressure reaching 40 bar.
Part of what drives the need for more prototyping and product development in PepsiCo is the company’s commitment to sustainability, including goals it has set for reduced material use. “From a sustainability perspective, the possible changes that we can make are bottle design, preform design, material or process changes. Having the ability to rapidly prototype allows us to find the best solution through one or more changes to these drivers,” Rodriguez says.
For example, reengineering bottle designs potentially offers the chance to increase the amount of recycled PET content in each bottle, reducing the need for virgin material. However, this change in material content leads to bottle geometry changes and blow molding parameter changes, both of which must be tested and refined. AM for tooling is making this sustainability-related exploration faster and cheaper.
“In just a couple days, we can now get a mold to blow only the quantity needed to get samples to all the stakeholders for real-time feedback,” Rodriguez says. That feedback leads to changes, likely necessitating another 3D-printed prototype mold. With the speed at which AM tooling can be obtained, multiple iteration loops can now occur in one week, rather than multiple weeks being needed for each loop.
So far, the AM tooling is only for prototyping. The next step the researchers see is bridge production.
Rodriguez’s team has seen 14,000 samples produced by a 3D-printed mold set that could have gone further still, but he says, “We need to significantly improve this.” One possible path he sees to raising this tool life is coating the tooling sets. “If we could increase that quantity to 100,000 bottles per 3D-printed mold, then that is of great interest to us,” he says. “At that quantity, we could send products to stores from the low-cost molds, and do test marketing.”
Updated and republished from Additive Manufacturing Media.
Related Content
Hammonton Mold, ADOP France Forge Strategic Partnership in Injection Blow Moldmaking
Hammonton Mold Inc., a leading full-service mold shop based in New Jersey specializing in injection blow molds (IBM), proudly announces its official partnership with ADOP France, a prominent IBM mold manufacturer based in Normandy, France.
Read MoreNavigating Economic Resilience and Consumer Trends
Consumer behavior provides mold builders insight into the evolving market dynamics of goods and services that helps strategic planning.
Read MoreMMT Chats: Applying Bench Lessons to the Business of Moldmaking
For this MMT Chat, my guest is Mark Gauvain, one of MMT’s newer Editorial Advisory Board members who has plenty to share as he recently made the move from working for some big manufacturers to working for himself as a consultant to moldmakers and molders on procurement and technology investment strategies.
Read MoreRead Next
How to Improve Mold Venting with Metal Additive Manufacturing
Patented 3D-printed mold insert design rapidly evacuates gases while preventing plastic flash-through, eliminates costly maintenance and need for press-side temperature-control units.
Read MoreWhat Is Additive Manufacturing's Place Alongside Traditional Moldmaking?
Technology improvements and design freedom solidify 3D printing’s role in mold manufacturing.
Read MoreHow to Calculate the Full Cost of Additive Manufacturing
A true evaluation of additive includes a look at materials, speed, quality, scalability, and cost.
Read More