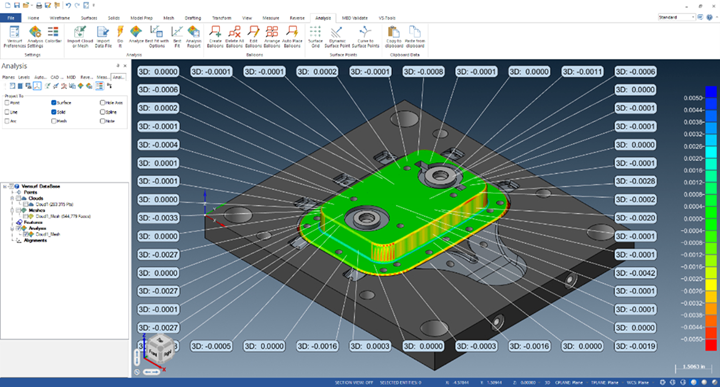
Measurement and inspection software, built on an intelligent CAD/CAM platform, ensures data continuity and preservation of the digital twin while supporting workflows where editing GD&T datums or G-code is necessary. The goal of a common metrology platform is to seamlessly support the design/build process, including CAD/CAM and computer-aided inspection (CAI). Photo Credit, all images: Verisurf
Automated metrology is pervasive in manufacturing today, but not just for quality verification. Various types of coordinate measuring machines (CMMs), also called sensors, combined with applicable software, are being put to work across the manufacturing enterprise for many applications. While quality verification is at the root of metrology in manufacturing, the technology is also used for reverse engineering, especially when verifying or capturing complex surface profiles, tool building for mold and die and fixturing applications, assembly guidance and more.
The metrology genie is essentially out of the bottle. It continues to be fueled by the creativity of design and manufacturing engineers, technicians and CMM operators, who are credited with expanding the technology beyond the lab to the shop floor and even into the field. The expansion of automated metrology has been very positive. Still, it has caused challenges for many companies with legacy equipment or new departments within the organization with an emerging need for metrology capabilities.
Whether your current or future needs include CMM programming and inspection, reverse engineering or mold building, a common platform approach will save time and money while improving efficiency and quality across the board.
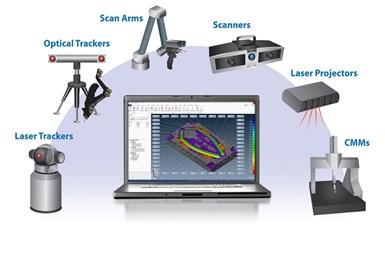
A critical success factor in implementing a common metrology platform is universal software compatibility. The software must support all CAD file types, and interface with and operate all fixed and portable CMMs, regardless of type or brand, across your manufacturing enterprise.
Setting the Software Stage
With metrology beyond the walls of the lab, there is a need to get organized, both from a solutions and budget perspective. If not, shops risk sacrificing productivity gains over the long haul. This is compounded by better, faster and more flexible CMMs and multiple software choices to drive them.
On average, shops today use three or more metrology software programs to keep all of their CMMs running. This is due to legacy or closed operating systems of existing CMMs, new CMMs purchased with OEM software or existing software lacking the flexibility and power to effectively support a broad range of metrology applications.
Shops are starting to take a broader view of metrology and the software that helps automate it. A strategy behind this is to implement a foundational software platform for all metrology workflows across the manufacturing enterprise, providing power, flexibility and extensibility while maintaining repeatable process control.
Openness and compatibility are significant considerations for shops looking to select the right platform. Ideally, you only want one software to learn, maintain and maximize. For example, a software built upon a CAD/CAM platform that supports model-based definition, works with all CAD files and drives all fixed and portable CMMs, including 3D scanners and trackers.
The accelerated adoption of CAD/CAM and model-based design/build workflows has pushed metrology vendors to innovate to keep up with the digital thread trend, or as it is often referred to in Industry 4.0 circles, “the digital twin.”
Today, there is an array of fixed and portable CMM choices, including arms, scanners and laser trackers. Selecting the right CMM type to match your application, whether quality inspection, reverse engineering, tool building or something else, is essential. To implement a common software strategy, you need to select a platform that can support your intended application workflows, drive all your devices and be able to keep up from a processing performance standpoint. Compatibility challenges come into clear view when you start introducing legacy CNC CMMs and new high-performance measurement sensors capable of measuring millions of points very quickly.
A complete hardware/software solution that includes open platform metrology software plus a scanner option for measuring flexibility can be used for automated “in-process” inspection right to the shop floor to verify manufactured parts directly to nominal 3D CAD models or drawings. The common measurement software extends the 3D model-based workflow to include reverse engineering of features or complete parts and tool building.
Step by Step
Here are six steps to implement an inspection software strategy:
-
Start With Software
Too often, manufacturing companies either minimize the importance of measurement and inspection software or, worse, they make purchase decisions based on hardware features that may or may not provide the results they need. Only after they take delivery and use the equipment do they realize that they have purchased software that is not up to the task or is the wrong type of CMM, given their workflow and the required results. Select your software platform first.
-
Focus on Repeatable Process Control
Repeatable process control is the backbone of quality management and should be applied to all metrology workflows, regardless of application. It is a systematic approach to managing processes that ensures the quality of the final product is consistent, reliable and meets customer expectations. Hence, metrology automation software should support repeatable process control.
The software must work seamlessly with intelligent CAD/CAM data, adding value while maintaining data continuity and providing output to downstream tools that monitor statistical process control, six sigma, total quality management and lean manufacturing initiatives.
-
Software and Device Compatibility
Choosing the right metrology software platform will ensure compatibility with all CAD file types and interface with and operate all fixed and portable CMMs, regardless of type or brand. It is plain to see the benefits this has in maintaining digital continuity and maximizing resource utilization. To take device compatibility to the next level, your metrology software should have software development kits to integrate with systems like advanced automation using robotics effectively.
-
Data Continuity
Your metrology software needs to work with the various formats used in other areas of your manufacturing operation, e.g., CAD/CAM with intelligent geometric dimensioning and tolerance (GD&T). By using a common metrology platform across the manufacturing enterprise, you ensure the consistency of shared data and database accessibility. This benefit is amplified when sharing results with downstream applications such as SPC statistical process control and product lifecycle management.
-
Operator Training and Education
You no longer have to settle with multiple metrology software programs due to legacy CMMs or proprietary devices that do not support open communication protocols. Tribal knowledge, where certain employees must be dedicated to specific machines because they are the only ones who know the software to run them, is a thing of the past. Being able to train operators across all metrology workflows and device types on a single software platform makes sense.
Consistency of programming, use of available software productivity tools and the ability to create workflows that can be repeated on any available measurement device are all benefits of a single software platform strategy. Training time and associated costs are reduced while improving repeatable process controls and data consistency.
Reference Point System Alignment is an example of the type of workflow one might expect from an enterprise-wide metrology platform. These alignments play a critical role in industries like automotive, stamping die, aircraft engines and power generation, ensuring precise alignment of points and features on different part types to defined reference points.
-
Software Maintenance
By implementing a common metrology software strategy, you reduce dependency on multiple software applications and gain greater efficiency and control. This will reduce duplicate costs associated with licensing fees and annual maintenance agreements with multiple software providers.
A common metrology software approach to the manufacturing enterprise helps to mitigate challenges by establishing and maintaining universal compatibility. The goal should be one metrology software for any CAD file and all CMMs. Whether your current or future needs include CMM programming and inspection, reverse engineering or mold building, a common platform approach will save time and money while improving efficiency and quality across the board.
When designing and implementing a metrology strategy for your manufacturing enterprise, do your homework, ask questions and lean on software providers for help. Don’t accept a canned demonstration; ask for a use case or example based on your unique workflow requirements.
Related Content
Surface Finish: Understanding Mold Surface Lingo
The correlation between the units of measure used to define mold surfaces is a commonly raised question. This article will lay these units of measure side by side in a conversion format so that companies can confidently understand with what they are dealing.
Read MoreLaser Welding Versus Micro Welding
The latest battle in finely detailed restoration/repair of mold materials.
Read MoreHow to Use Diffusion Bonding to Optimize a Mold’s Thermal Performance
Joining dissimilar metals has tremendous potential for conformal cooling, but to successfully use diffusion bonding, a mold builder must understand the complexities of the interface and its effect on the chemical and thermo-mechanical properties of the bond.
Read MorePrecision Welding Services Offer Rapid Turnaround Mold Repair and Reduced Molder Downtime
X-Cell Tool & Mold relies on outsourced, high-quality welding repairs from Lewis-Bawol Welding to ensure its customers' molds are back in production quickly and affordably.
Read MoreRead Next
Facing the Quality Challenges of Large, High-Precision Tooling
Advanced off-line inspection software speeds up mold manufacturing and assembly for aerospace giant.
Read MoreSpeed Mold Verification and Improve Global Cooperation
Technology solution that combines model-based inspection software and portable inspection devices to improve mold verification.
Read MoreMeasuring Massive Molds
When working with massive molds, the penalties of rework are greater than those of smaller sized molds.
Read More