Q&A: How to Optimize Micro Molding Outcomes
Molding at the micro-scale requires a completely new perspective concerning rheology, tooling, gating, handling and assembly. Accumold Sales Engineer Craig Tappe explains the micro molding process and the right questions to ask when securing a tooling specialist.
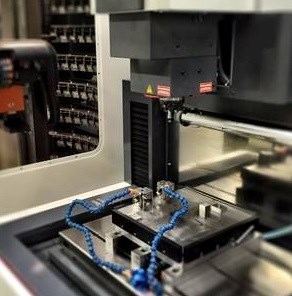
Craig Tappe has been with Accumold for nearly 11 years and has worked as a machinist, lead toolmaker, and is today one of the company's sales engineers. Accumold has grown to a 130,000 square foot fortified facility designed for assurance of supply, employs over 350 staff and is a net exporter shipping all over the world every day from its Ankeny, IA, USA facility, which runs 24 hours a day, 7 days a week.
Here Tappe breaks down the micro molding process and what to look for in a micro molding specialist:
Q: What is design for micro molding (DfMM)?
DfMM refers to developing and optimizing designs specifically tailored for micro-scale injection molding. Micro molding is a highly precise manufacturing technique to produce miniature plastic parts with intricate details and dimensions in the micrometer range. Designing for micro molding involves considering material selection, part geometry, tooling requirements and process limitations unique to micro-scale production. The goal is to create designs that maximize manufacturability, ensure part quality and enhance functionality within the constraints of micro molding technology. Attention to detail, such as minimizing wall thickness variations, incorporating proper gating and venting and addressing potential issues related to part ejection and moldability, is crucial in achieving successful micro molding outcomes.
Q: What challenges are faced when transitioning from prototype development to large-scale production in micro molding?
One of the key difficulties is scaling up the production process while maintaining the same precision and quality achieved during prototyping. Material behavior, tooling design and process parameters must be optimized to ensure consistent and reliable production. Also, cycle time, cooling and part ejection issues become more critical when moving to large-scale production, as they can significantly impact productivity and cost efficiency. Managing increased tooling complexity, maintaining tight tolerances and addressing potential defects or variations that may arise during high-volume manufacturing are also crucial challenges. Often prototype molders will ask for part design changes that eliminate micro features on parts as their machining processes cannot achieve the required tolerances. Effective communication and collaboration between designers, engineers and manufacturers become paramount.
Q: What are the key factors to consider when selecting a micro molder that can scale up to large-scale production?
Expertise and experience in micro molding at larger volumes is vital. Manufacturing capabilities, including advanced machinery, quality control processes and the ability to handle increased production demands, should be assessed. Effective project management, strong communication channels and a commitment to continuous improvement are also important. More specifically, look for a large onsite toolroom that can handle multiple large projects simultaneously, sustainability initiatives (recycling plastic), an on-site automation team/capabilities to reduce cost and available production floor space/press capacity to scale quickly.
Q: How Accumold has successfully scaled up from prototyping to large-scale production while maintaining quality and efficiency?
At Accumold, we've taken multiple projects for Fortune 100 medical companies from the early engineering/DFM stages into prototyping on one-cavity tooling then into full-scale production with multiple 16- and 32-cavity tools. We currently run projects with 200 million parts per year volumes and have the capabilities/scalability to produce billions of parts annually.
Q: What are the advantages of vertical integration when micro molding?
The advantages of vertical integration in micro molding include enhanced control over the entire production process, improved coordination between design and manufacturing stages, reduced lead times, better quality assurance and increased cost efficiency. This vertical integration allows Accumold to hold quick lead times and efficiently collaborate to solve problems and produce quality products.
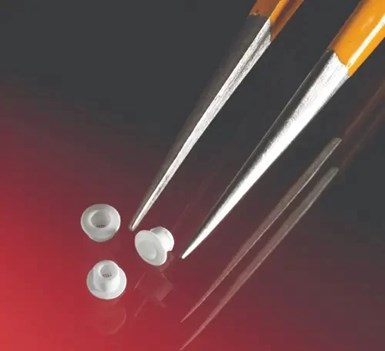
Q: How does collaboration between design teams and micro molding experts facilitate the optimization of product design for the micro molding process?
We work with customers to establish part designs ideal for the finished product and fit well with the molding process. This combination allows for a robust manufacturing solution and consistent part quality. We run mold flow simulations, provide feedback on snap features, work to provide solutions for molding complex undercuts and share our expectations for finished part characteristics based on microfeature designs.
For example, we worked with a wearable diabetes patch maker to redesign the cannula portion that is inserted into the patient's skin where the insulin is dosed through. The old cannula design was an expensive multi-step manufacturing process. It used a polyimide tube with a tipping and flaring operation and a separate hub to which this polyimide cannula was glued. These parts had a lot of fallout and quality issues from the gluing and were very expensive. Accumold worked in our innovation lab to provide a solution for this problematic thin-walled drug delivery cannula. We produced a single-piece cannula that fits our customer's design requirements and is produced at a fraction of the cost.
Q: What role does quality control play in micro molding, especially when scaling up production?
We use automation wherever we can – some of our tool-build processes, electrode cutting, electrode measurement and touch-off systems. This eliminates human error and ensures that every cavity from tool to tool is identical for high-volume projects. The electrodes are used to EDM the fine core/cavity details into our mold steel. All our production cells use automation and most of our measurement techniques also use automation. Accumold has strict preventative maintenance and calibration standards on all equipment and tooling.
Q: How does Accumold stay up-to-date with the latest advancements and technologies in micro molding?
We constantly attend technology and equipment trade shows to ensure we have the latest and greatest equipment. A year or two ago, we brought in our first (we have two now) Nano Dimension Fabrica 2.0 micro additive manufacturing (AM) machines. This has helped us with rapid front-end prototyping for low-cost, quick-turnaround front-end development. We are now close to using this technology for 3D-printed prototype tooling. We plan to use a new high temp 3D printing resin to 3D print the mold core and cavity components for prototype tools.
Q: Can you provide insights into the future of micro molding?
All components are getting smaller and multiple functions are being designed into each component, such as wearable medical devices, micro-electronics and surgical tools.
Related Content
VIDEO: How to Protect Your Hot Runner Systems
Chad Root Managing Partner for Fast Heat by Spark Industries reviews some molding machine integration concepts that protect hot runner systems, the molding machine, reduce scrap and help keep a log of events.
Read MoreVIDEO: Standardization and the Future of Moldmaking
Progressive Components President Glenn Starkey discusses their focus on standardization and the future of moldmaking (it’s here to stay!).
Read MoreMMT Chats: Westfall Technik Talks Runnerless Micro Molds and More
Westfall Technik sits down with MMT Editorial Director Christina Fuges to discuss their new micro hot runner technology, the closeness of the moldmaking community and the importance of integration. This episode is brought to you by ISCAR with New Ideas for Machining Intelligently.
Read MoreMentorship Matters: A Fresh Perspective from a Young Female Newcomer to a Mature Male-Dominated Industry
Jane Huot, a 23-year-old mold designer and project manager, celebrated her one-year anniversary with Accede Mold & Tool by going on her first business trip to a conference geared for women in plastics and shadowing sales on customer visits.
Read MoreRead Next
Toolroom Perspective on Micro Molding
Design for manufacturing, or more specifically design for micro molding is critical to this mold manufacturing niche as it presents unique challenges and impacts the tool build.
Read MoreOpportunities for Mold Shops with Micro Molds and Micro Milling
Learning about the trends and challenges with micro molds and micro milling will help shops maintain their competitive edge.
Read MoreDesign-for-Manufacture Review on Micro-Molding Operations
According to Mold Craft Inc., a design-for-manufacture (DFM) review ensures that its customers receive the highest quality molds that produce parts with close tolerances.
Read More