President
- FMA
- The Fabricator
- FABTECH
- Canadian Metalworking
Categories
- Additive Manufacturing
- Aluminum Welding
- Arc Welding
- Assembly and Joining
- Automation and Robotics
- Bending and Forming
- Consumables
- Cutting and Weld Prep
- Electric Vehicles
- En Español
- Finishing
- Hydroforming
- Laser Cutting
- Laser Welding
- Machining
- Manufacturing Software
- Materials Handling
- Metals/Materials
- Oxyfuel Cutting
- Plasma Cutting
- Power Tools
- Punching and Other Holemaking
- Roll Forming
- Safety
- Sawing
- Shearing
- Shop Management
- Testing and Measuring
- Tube and Pipe Fabrication
- Tube and Pipe Production
- Waterjet Cutting
Industry Directory
Webcasts
Podcasts
FAB 40
Advertise
Subscribe
Account Login
Search
The value of a workforce prepared for smart manufacturing
Leveraging knowledgeable employees is key to smart manufacturing success
- By Bill Frahm
- February 14, 2024
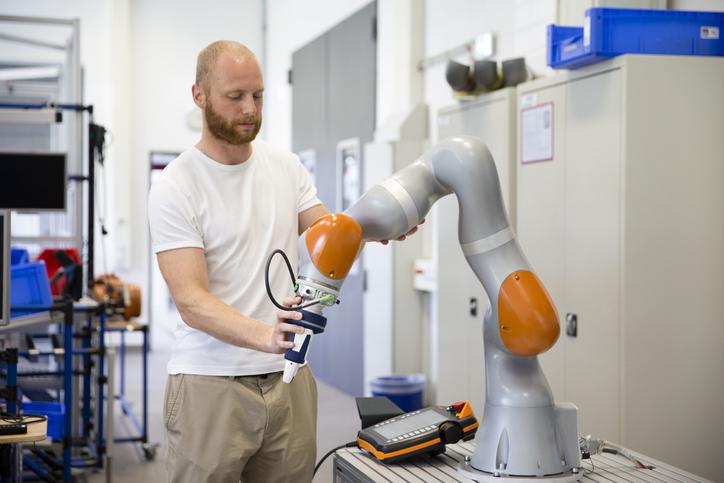
As new technologies are introduced to the shop floor, managers need to talk open and honestly about how these new tools will change processes for the better. fotografixx/E+
The greatest asset in any smart manufacturing implementation is a prepared workforce. Employees have the knowledge, intuition, and experience to define where smart manufacturing can add value and what information will contribute to finding solutions. Your employees, especially subject matter experts, also are the most reliable control over misapplication, misuse, and poor implementation of smart manufacturing. Unfortunately, the current hype cycle isn’t letting the message through.
Facing Fear, Embracing Technology
Artificial intelligence anxiety is a real thing. Employees are concerned about job loss, job changes, loss of operational control, and quality and safety risks. I recently read that CEOs are looking to install AI in the hope of reducing head count. In fact, we are just starting to move past the hype and beyond the jargon to define what AI is and how it will serve manufacturers.
Most of us don’t expect mass layoffs; in fact, many people expect a redistribution of skills. Manufacturers will need to hire people to maintain networks, hardware, and software. Data integrity, control, and security will become critical activities, either through education or costly experience. Traditional manufacturing workers will need to become more aware of data integrity and be able to understand the outputs of statistical analysis.
Probably the greatest job impact will be with employees who resist new technologies. Changes today happen rapidly, and we all need to understand those changes and learn to manage what is new. It’s important for employees and employers to develop their understanding to move forward. A good start is to explore free courses that present the fundamentals of AI, the terminology, and current and potential applications.
The Role of Subject Matter Experts
Smart manufacturing and AI capture measurements, analyze historical data, and predict future events through statistical analysis. For most of us, the math behind statistical analysis mainly serves as a great way to clear out a party. But in the data-centered world, statistics are unavoidable.
However, data analysts don’t have the training or experience to understand material properties, reliability, and maintenance needs, process flows, and equipment-operating tolerances. This is where subject matter experts shine. They understand the impact and relationships of manufacturing properties and variables. They can, and should, drive a large part of statistical analysis on the plant floor.
Subject matter experts don’t need to understand the calculus, but they must understand:
- The integrity of input variables.
- How material and production variables influence production operations.
- Whether analytical reports truly reflect operational results.
Control over the quality of analysis only happens when production employees understand:
- The fundamentals of the analytical methods used.
- The need for reliable input variables.
- The meaning, scope, and limitations of statistical output.
Accountability and Communication
The many changes in information technologies demand greater accountability by executives, data analysts, and production employees. Complex and risky algorithms should be reviewed by both analysts and production employees to ensure they support good decisions without jeopardizing plant and employee safety.
Another consequence of these newer technologies is that we must make sure our managers know how to hire the right talent. Communication, subject expertise, integrity, and technical skills will become increasingly critical to a successful implementation and support of new technologies.
Smart manufacturing and its components offer manufacturers the ability to analyze tremendous volumes and types of data to make better and faster decisions for operations. But the speed and volume of data analysis comes with great risk if used improperly. The only solution is the competence and diligence of your workforce. Building both competence and acceptance demands managers communicate honestly with their workforce and train employees how to use and control these frightening but exciting new technologies.
subscribe now
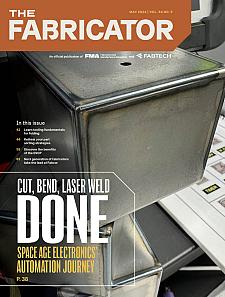
The Fabricator is North America's leading magazine for the metal forming and fabricating industry. The magazine delivers the news, technical articles, and case histories that enable fabricators to do their jobs more efficiently. The Fabricator has served the industry since 1970.
start your free subscriptionAbout the Author
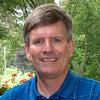
Bill Frahm
P.O. Box 71191
Rochester Hills, MI 48307
248-506-5873
- Stay connected from anywhere
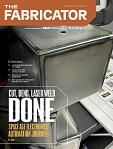
Easily access valuable industry resources now with full access to the digital edition of The Fabricator.
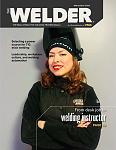
Easily access valuable industry resources now with full access to the digital edition of The Welder.
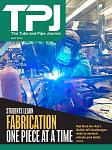
Easily access valuable industry resources now with full access to the digital edition of The Tube and Pipe Journal.
- Podcasting
- Podcast:
- The Fabricator Podcast
- Published:
- 04/16/2024
- Running Time:
- 63:29
In this episode of The Fabricator Podcast, Caleb Chamberlain, co-founder and CEO of OSH Cut, discusses his company’s...
- Trending Articles
Tips for creating sheet metal tubes with perforations
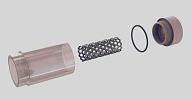
Are two heads better than one in fiber laser cutting?
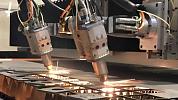
Supporting the metal fabricating industry through FMA
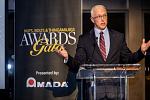
JM Steel triples capacity for solar energy projects at Pennsylvania facility
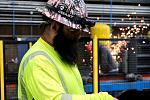
Omco Solar opens second Alabama manufacturing facility
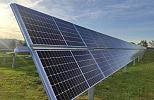
- Industry Events
16th Annual Safety Conference
- April 30 - May 1, 2024
- Elgin,
Pipe and Tube Conference
- May 21 - 22, 2024
- Omaha, NE
World-Class Roll Forming Workshop
- June 5 - 6, 2024
- Louisville, KY
Advanced Laser Application Workshop
- June 25 - 27, 2024
- Novi, MI