President
- FMA
- The Fabricator
- FABTECH
- Canadian Metalworking
Categories
- Additive Manufacturing
- Aluminum Welding
- Arc Welding
- Assembly and Joining
- Automation and Robotics
- Bending and Forming
- Consumables
- Cutting and Weld Prep
- Electric Vehicles
- En Español
- Finishing
- Hydroforming
- Laser Cutting
- Laser Welding
- Machining
- Manufacturing Software
- Materials Handling
- Metals/Materials
- Oxyfuel Cutting
- Plasma Cutting
- Power Tools
- Punching and Other Holemaking
- Roll Forming
- Safety
- Sawing
- Shearing
- Shop Management
- Testing and Measuring
- Tube and Pipe Fabrication
- Tube and Pipe Production
- Waterjet Cutting
Industry Directory
Webcasts
Podcasts
FAB 40
Advertise
Subscribe
Account Login
Search
Encouraging adoption of smart manufacturing technologies
5 tips for fostering employee buy-in throughout your fabrication shop
- By Bill Frahm
- January 12, 2024
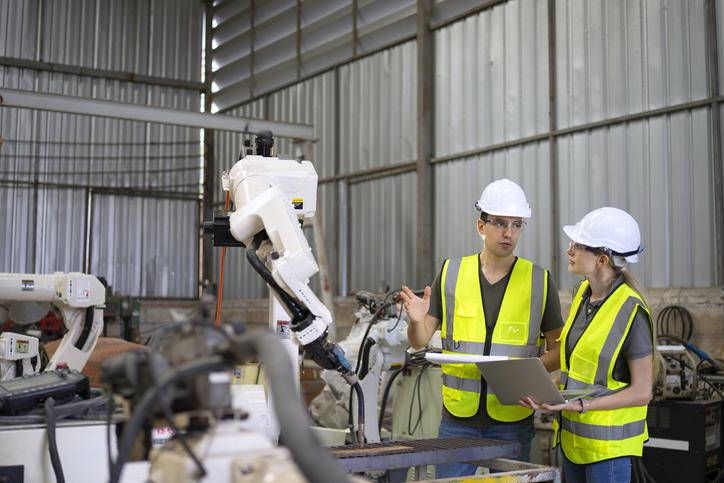
Implementing smart manufacturing is a slow process that can create confusion and distrust among employees. That's why company leadership needs to earn the trust of employees if it is to exploit the true power of tomorrow's technologies today. eyesfoto/E+
Happy 2024! At the beginning of the new year, many of us make personal and professional resolutions, setting goals to adapt our behavior to improve ourselves and our relationships with those around us. Likewise, it’s a good time to commit to learn about and adopt the many emerging technologies that can help you increase productivity, reduce plant downtime, improve product quality and safety, and support employee safety—and to encourage your employees to do the same.
Most fabricators understand that the transformation to smart manufacturing is increasingly critical to efficiency, product quality, and competitiveness. But adoption of new technologies often is painfully slow, and that creates confusion and distrust among employees. Management’s failure to share meaningful information also contributes to workers’ lack of confidence and poor acceptance. Employees must understand the relevance of new technologies to their job and how those technologies will influence their daily activities. They need confidence that the technology will be helpful and intuitive.
Managers will always encounter resistance from people uncomfortable with technology and from those who are eager to reject anything that looks like a change. In his book “My Life and Work,” Henry Ford expressed his surprise that some employees resist any change to their routines. In an attempt to make work more interesting and promote shared skills, Ford tried to diversify the daily activities of his employees—and met resistance. He spoke of one worker who operated a treadle all day. Seeing the tediousness of the work, he offered the employee a chance to rotate his responsibilities. The employee rejected the offer, preferring to stay with the “comfort” of the treadle operation. These attitudes remain with employees of all kinds. Unfortunately, companies often allow these attitudes to persist.
Leadership and guidance are necessary to encourage a positive environment willing to support technology adoption. The biggest keys to acceptance are communication (both talking and listening), honesty, and commitment.
Here are five ways to start your journey.
1. Choose Technology to Support Your Workforce
Whatever software you plan to use, it must demonstrate to the employees its ability to improve operational results and be intuitive.
Smart manufacturing is different from traditional, transaction-based applications. Traditional applications accept a formatted input, process it, and return a predictable result. Smart manufacturing applications can be a bit fuzzier in the definition of their inputs and outputs. Often, the inputs will be a statistical sample, a laser-measured component or tool geometry, or a design specification. The outputs may include a warning light or a graphic.
Your employees will need training to understand how they should contribute to the input data. They must also be confident that they will understand the outputs and that the outputs are unambiguous.
Encourage your employees to participate actively in adoption and include them in trials and pilot projects. Teach them to offer constructive feedback—and listen when they do.
2. Present and Discuss Your Reasons and Expectations
Acceptance is easier when you have solid and relatable reasons for your decision to adopt a new technology. Articulate your case to your employees in terms of real results: product quality, reliability, throughput, safety, and finances.
Leave out discussions of the Fourth Industrial Revolution and the wonders of artificial intelligence. They’re pointless if you can’t explain the expected benefits, risks, and impact on the workplace.
Smart manufacturing is hard. Tying together a large volume of collected data and analytics in a safe, meaningful way demands a disciplined approach to implementation. Much of your necessary discipline will come from the knowledge and experiences of your subject matter experts. Most of these experts will be the engineers, toolmakers, and production employees who must manage production daily.
3. Offer Focused Training
Training employees how to use technology to do their jobs better requires teaching them to understand:
- The data used to perform analysis.
- The fundamentals of statistics to understand the importance of selecting the right variables, the meaning of statistical sampling, and the meaning and interpretation of analytical outputs.
- How analysis and measurement will influence their work conditions, efficiency, and product quality.
4. Identify and Encourage Influencers
From the beginning of your project, you will notice employees fall into several categories between willing adopter and naysayer. Continuous promotion from the same managers loses its influence quickly. However, you can use your willing adopters as influencers to open a continuous and relatable communication channel with their co-workers on the production floor.
Build and maintain a channel to influencers, sharing both progress and challenges. These influencers should include employees trusted by both management and production employees. If trust is built on honest assessment and sharing of real-time information, you will begin to convert some of your negative employees to be, at least, cooperative participants.
5. Highlight and Share Credit for Quick Wins
“Nothing succeeds like success,” said Alexandre Dumas in his 1854 book “Ange Pitou,” and it holds true 170 years later. One of the best strategies to implement a complex project is to begin with small achievements. These achievements allow for developers to learn, build a sense of accomplishment, and establish momentum to attempt more difficult goals and overcome obstacles. These achievements also provide good news to share among management and employees.
Your achievements must be real and measurable to be credible. Installing an application is an important milestone but not really a credible achievement. Promote your achievements in real production terms:
- Reduced electricity consumption by 4%.
- Improved throughput by 5%.
- Decreased scrap.
- Improved machine availability.
- Identified and fixed issues with input stock.
It takes more time to measure real results, but the credibility of the information will go far in supporting your project.
Basic Principles for Success
Finally, throughout this process, follow these basic principles:
- Be honest about the benefits, challenges, and risks of the new technologies you propose to implement.
- Train your subject matter experts to manage and respond to new technologies. Their expertise is critical to build and maintain applications that support productive decision-making.
- Encourage adoption by building open lines of communication with stakeholders and recognizing productive contributors.
- Choose technologies that are within your capabilities, approachable, and intuitive.
- Implement technologies that support the culture and routines of your workplace.
- Encourage acceptance and adoption in a positive, constructive manner.
subscribe now
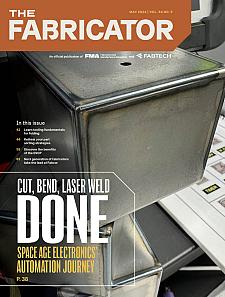
The Fabricator is North America's leading magazine for the metal forming and fabricating industry. The magazine delivers the news, technical articles, and case histories that enable fabricators to do their jobs more efficiently. The Fabricator has served the industry since 1970.
start your free subscriptionAbout the Author
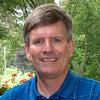
Bill Frahm
P.O. Box 71191
Rochester Hills, MI 48307
248-506-5873
- Stay connected from anywhere
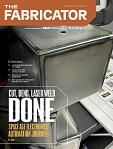
Easily access valuable industry resources now with full access to the digital edition of The Fabricator.
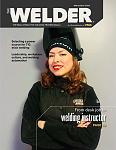
Easily access valuable industry resources now with full access to the digital edition of The Welder.
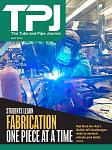
Easily access valuable industry resources now with full access to the digital edition of The Tube and Pipe Journal.
- Podcasting
- Podcast:
- The Fabricator Podcast
- Published:
- 04/16/2024
- Running Time:
- 63:29
In this episode of The Fabricator Podcast, Caleb Chamberlain, co-founder and CEO of OSH Cut, discusses his company’s...
- Trending Articles
Tips for creating sheet metal tubes with perforations
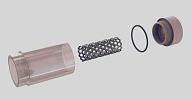
JM Steel triples capacity for solar energy projects at Pennsylvania facility
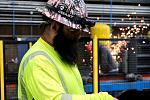
Are two heads better than one in fiber laser cutting?
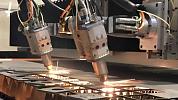
Supporting the metal fabricating industry through FMA
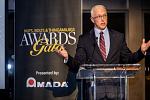
Omco Solar opens second Alabama manufacturing facility
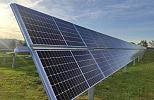
- Industry Events
16th Annual Safety Conference
- April 30 - May 1, 2024
- Elgin,
Pipe and Tube Conference
- May 21 - 22, 2024
- Omaha, NE
World-Class Roll Forming Workshop
- June 5 - 6, 2024
- Louisville, KY
Advanced Laser Application Workshop
- June 25 - 27, 2024
- Novi, MI