- FMA
- The Fabricator
- FABTECH
- Canadian Metalworking
Categories
- Additive Manufacturing
- Aluminum Welding
- Arc Welding
- Assembly and Joining
- Automation and Robotics
- Bending and Forming
- Consumables
- Cutting and Weld Prep
- Electric Vehicles
- En Español
- Finishing
- Hydroforming
- Laser Cutting
- Laser Welding
- Machining
- Manufacturing Software
- Materials Handling
- Metals/Materials
- Oxyfuel Cutting
- Plasma Cutting
- Power Tools
- Punching and Other Holemaking
- Roll Forming
- Safety
- Sawing
- Shearing
- Shop Management
- Testing and Measuring
- Tube and Pipe Fabrication
- Tube and Pipe Production
- Waterjet Cutting
Industry Directory
Webcasts
Podcasts
FAB 40
Advertise
Subscribe
Account Login
Search
Manufacturing execution systems (MES) in an era of skilled labor challenges
How good information management and automations attracts talent
- March 24, 2023
- Article
- Manufacturing Software
Editor’s Note: The following is based on “Manufacturing execution systems in an era of labor challenges,” presented at FABTECH 2022 in Atlanta, by Andrew Robling, principal product marketing manager at Epicor.
Metal fabricators everywhere face a turnover battle. Meanwhile, industry overall has a record number of unfilled jobs; Deloitte predicts that by 2030, almost 2.1 million skilled jobs will go unfilled.
Fabricators need to attract adept workers to operate equipment, inspect parts, and document and report production. That last job function—documenting and reporting production—can be a source of headache. From material handling towers for laser cutting and punching, automated parts offloading, robotic press brakes, robotic welding, automated powder coating, and even automated guided vehicles, fabricators invest heavily in automating part flow. More than anything else, reliable automation offers predictability. Well-engineered systems perform a task the same way at the same pace, every day.
At the same time, fabricators need skilled people to program, operate, and maintain these systems. A fully automated laser cutting machine can be extraordinarily productive—until something breaks. Skilled people also need to inspect parts and assemblies to ensure what leaves the plant exceeds customer requirements. In short, manufacturers are automating, and they need good people to do it.
Surrounded by machine automation, operators and managers might be making notes on paper, keying numbers into computers, printing out spreadsheets. A new employee might be struggling with a task and—since he has no easy access to training documents—either waits for help or (more often than not) just dives in to get the job done and hopes for the best.
In this scenario, part flow might be highly automated, but the flow of information is not. Like with part flow, automated information flow—built on a system that’s well-designed and reliable—adds predictability. People (ideally, at least) always have the right information when they need it.
This is where modern manufacturing execution systems (MES) step into the picture. A shop might use an enterprise resource planning (ERP) system to track shop floor activity, but the data collection is usually periodic and manual. Operators simply key in the number of pieces they made, the scrap, and other variables. An MES collects real-time data from machines and operators on the shop floor, and often in an automated fashion.
Establishing that direct connection between the MES and the machine isn’t always straightforward, mainly because most manufacturers make use of both new and old machines, and older machines do require additional interfaces to establish that connection. Moreover, assembly operations might not have obvious ways to connect automatically to an MES. That said, some operations now are connecting torque guns and other hand tools directly to an MES, recording when the assembly operation takes place, the resulting torque, and other variables for each job.
Establishing that automated connection is worth the effort, since such data can act as the foundation for effective measurement and improvement. On top of that foundation, a fabricator can institute an information system that can help the organization thrive—despite the labor shortage.
Aiding the Temp
Imagine a fabricator needs an expanded crew to assemble a complex product for a few weeks or months. The shop has no choice but to rely on temp labor, but bringing them up to speed can be a challenge.
Here, guided operator instructions, accessible digitally through an MES, can help train new or temporary employees quickly. Yes, experienced people likely don’t need the guidance, but new and temporary people do. Those digital work instructions—a combination of graphics, text, and even video—exemplifies automated information flow. Rather than wait for a supervisor, they access the instructions on the screen right in front of them.
To be sure, digital work instructions alone won’t solve all temp worker challenges. If inexperienced or temporary employees receive inconsistent parts, don’t have the tools they need to complete the job, or if the instructions themselves are confusing, they’ll likely still need to call someone experienced for help. That said, having easy access to information, via a few clicks of the mouse or a few taps on a screen, is half the battle. Such information makes life easier for new employees, who therefore will be more likely to stay.
Of course, documentation can’t cover every potential problem a new employee (or any employee, for that matter) might face. And nothing can be more frustrating than being caught with a problem when there’s no one around to help. An MES can help here too. Say a new employee has trouble with a job. Instead of wandering around the shop looking for his supervisor (or, even worse, just guessing the best course of action and hoping for the best), he can put an alert on the MES, which notifies the right people and perhaps turns on visual signals like andon lights.
In a similar vein, MES connections help track labor efficiencies and other variables of specific operations. With this information, managers can see what operations might be suitable for temp labor in the first place. If a certain operation just can’t be learned quickly or the cost of error is especially high, they can choose not to rely on temps and hire or cross-train permanent employees to cover that operation. If the company does hire temporary employees in a particular department, it bases that decision not on hunches or assumptions, but on historical data. To a manager who’s worked in manufacturing for years, a job might look simple. Historical data from the MES, though, could reveal a very different reality.
Similarly, an MES can help spread best practices. In some cases, star performers go unnoticed, quietly producing more than anyone else. In other cases, people know who the stars are but just assume their performance came from years of experience, or maybe they just have natural talent. In either case, everyone assumes their efficiency can’t be replicated.
An MES strips away all this subjectivity. Other, less efficient workers might not have gotten the proper training, and data from the MES reveals the training gap. Supervisors provide training (perhaps with some digital work instructions and videos, again through the MES), and efficiencies throughout the department rise.
Such scenarios become more common as operations go beyond simply tracking machine uptime. Tracking the inspections, the setup, and all the other labor associated with the machine helps reveal an operation’s true labor needs, what the training needs are, and the type of skill that’s really required. This helps a company hire or train the right people for that job.
A Job You (Don’t Want to) Count On
People don’t choose a manufacturing career because they like counting parts in bins or pallets. Miscounts are common, as is worker frustration. What if an operation has sensors that track parts as they emerge from a machine, then feed those numbers directly to the MES? In this scenario, the MES automates a job nobody wants.
The same applies to job tracking, writing inspection points on a form or keying them in manually at a computer terminal. New hires want to make and inspect parts; they don’t want to spend half their days as recordkeepers.
Automating data collection helps with onboarding and makes new employees less likely to leave. They don’t spend time learning how to key in this number on that screen, or file this or that form to process a job. They focus instead on making and inspecting parts—activities customers are actually paying for.
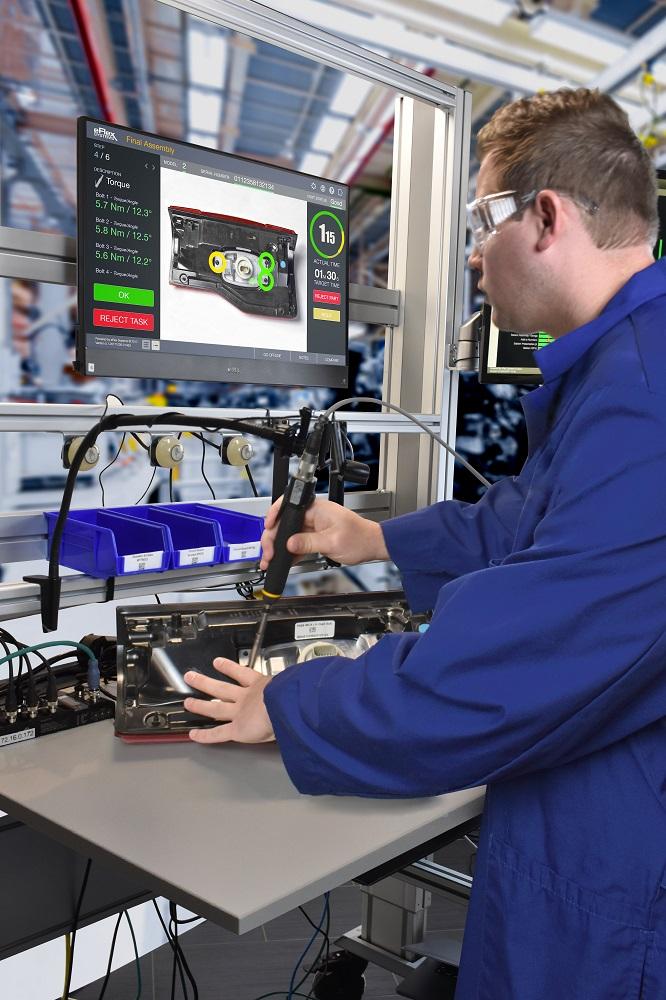
A tool communicates with the MES, verifying that the proper torque has been achieved on a specific assembly.
As metrics are collected automatically in the background, operators receive real-time feedback. They want to do well, and it’s helpful to have a benchmark right in front of them. They also can see when there’s a problem—immediately. Perhaps their machine isn’t working well. They can see evidence in the metrics and either rectify the situation or notify someone who can.
Problematic metrics brought up in production meetings or daily huddles spur reaction. The best people can do is fix what they can and institute measures to prevent the problem from happening again. Reaction also can stir emotion and finger-pointing, not least because operators feel frustrated and powerless. They might not have been aware of the problem until after the fact.
Real-time metrics from an MES spur preventive action. Operators see an issue as (or even before) it occurs and then immediately act. They’re not just a button-pusher, a small cog in a much larger organizational wheel. They identify and solve problems as they happen.
That feeling of “Big Brother is watching” often stems from a feeling of powerlessness, which can grow as managers continue to scrutinize past production numbers. But if employees see metrics in real time—and are given the time and resources to act—their perception might change.
Stop the Vicious Cycle
Say an operator records metrics on a paper traveler or another paper form, which is then brought to the office for data entry. Even worse, those entering the data are separate from frontline production, so they might not recognize there’s a problem when they key in the numbers (and they probably don’t have the authority to fix the problem anyway). Once someone finally reviews the metrics and sees the problem, it’s too late to fix, and employees do what they can to prevent recurrence.
Now, imagine that machine operator leaves the company. A new hire or cross-trained person takes his place. The new hire rushes through the recordkeeping (he wants to make parts, not fill out forms), the data-entry person keys in the data, after which managers catch the problem again. Frustration spurs turnover, which keeps this vicious cycle going indefinitely.
Automating the flow of information transforms this vicious cycle into a virtuous cycle. When a problem occurs, operators and managers know immediately, then work together to rectify it. Instead of working in silos—one person pushing a button at a machine, another keying in data, frustrated supervisors poring over stale production metrics—everyone sees what they need to see at the right time. This promotes collaboration and creates a pleasant and engaging environment—a place where prospective hires want to work and experienced talent won’t want to leave.
Related Companies
subscribe now
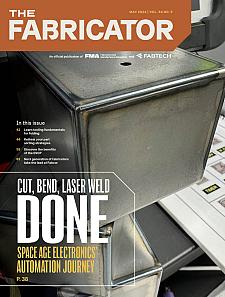
The Fabricator is North America's leading magazine for the metal forming and fabricating industry. The magazine delivers the news, technical articles, and case histories that enable fabricators to do their jobs more efficiently. The Fabricator has served the industry since 1970.
start your free subscription- Stay connected from anywhere
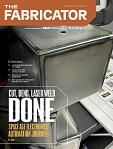
Easily access valuable industry resources now with full access to the digital edition of The Fabricator.
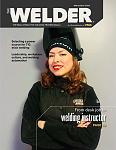
Easily access valuable industry resources now with full access to the digital edition of The Welder.
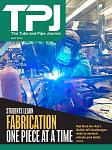
Easily access valuable industry resources now with full access to the digital edition of The Tube and Pipe Journal.
- Podcasting
- Podcast:
- The Fabricator Podcast
- Published:
- 04/16/2024
- Running Time:
- 63:29
In this episode of The Fabricator Podcast, Caleb Chamberlain, co-founder and CEO of OSH Cut, discusses his company’s...
- Trending Articles
Capturing, recording equipment inspection data for FMEA
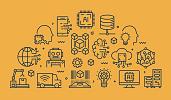
Tips for creating sheet metal tubes with perforations
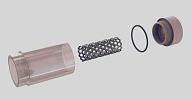
Are two heads better than one in fiber laser cutting?
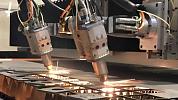
Supporting the metal fabricating industry through FMA
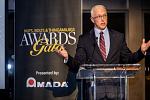
Omco Solar opens second Alabama manufacturing facility
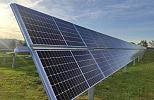
- Industry Events
16th Annual Safety Conference
- April 30 - May 1, 2024
- Elgin,
Pipe and Tube Conference
- May 21 - 22, 2024
- Omaha, NE
World-Class Roll Forming Workshop
- June 5 - 6, 2024
- Louisville, KY
Advanced Laser Application Workshop
- June 25 - 27, 2024
- Novi, MI