What Is Takt Time and How to Use It?
Takt time is a key concept in lean manufacturing and process management, representing the rate at which a finished product needs to be completed in order to meet customer demand. Let’s take a look at where and when it could be implemented.
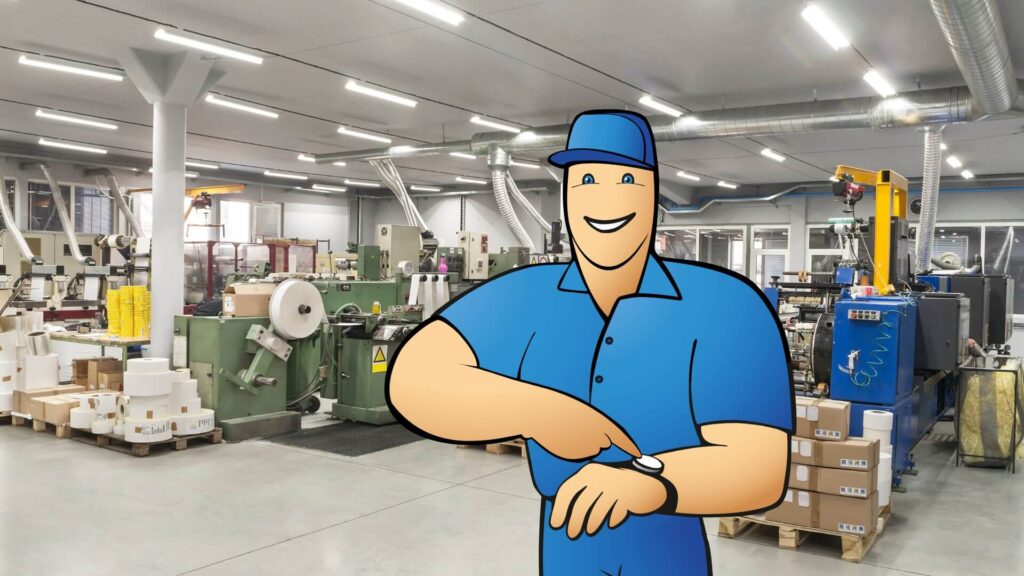
You can also listen to this article:
What is takt time?
Takt time is a key concept in lean manufacturing and process improvement that helps synchronize production with customer demand. It represents the maximum amount of time in which a product needs to be processed to meet that demand.
If a production line or workstation is unable to process at takt time, additional resources, process re-engineering, or demand leveling might be needed.
Takt time formula
Takt time is calculated by dividing the available production time by the number of units required by customers.
Takt Time = Available Time / Demand
For example, if a toy factory operates for 480 minutes a day (8 hours) and the demand is for 240 toys per day, the takt time would be:
Takt Time = 480 / 240 = 2 minutes.
This means every 2 minutes, a toy should be completed to meet the daily demand consistently.
Be aware, however, that companies should also account for changeovers, maintenance, and other types of machinery downtime when implementing takt time.
Takt time vs. cycle time vs. throughput time
Takt time and cycle time are often mentioned in the same breath, yet they serve distinct functions. While cycle time refers to the amount of time it takes to complete a single production task (e.g. welding or drilling) from start to finish, takt time is the rate at which products must be completed to meet customer demand.
Another similar concept is throughput time, which is the total time it takes for a product to pass through the entire production process, from start to finish. Throughput time is, therefore, the actual time it takes for a product to be finished while takt time is the ideal time.
Benefits of takt time
Takt time plays a crucial role in production process optimization. Its importance in manufacturing can be highlighted through several key points:
- Aligning production with customer demand. Takt time ensures that the production rate is perfectly aligned with customer demand, preventing both overproduction and underproduction. This alignment aids in keeping customer lead times short, improving customer satisfaction and loyalty.
- Improving efficiency and reducing waste. By setting a consistent production pace, takt time helps in identifying and eliminating inefficiencies and bottlenecks in the production line. It reduces waste, such as excess inventory and idle time, contributing to a leaner, more cost-effective manufacturing process where value-added activities reign supreme.
- Better planning and resource allocation. Takt time provides a clear framework for production scheduling, workforce allocation, and resource utilization. It allows for more accurate forecasting, inventory management, and supply chain management, leading to improved overall operational efficiency.
- Process standardization and predictability. Implementing takt time leads to standardized work processes, making production activities more predictable and manageable. Standardization simplifies training and onboarding processes, ensuring consistent quality and performance.
- Supporting continuous improvement. Takt time serves as a benchmark and key metric for continuous improvement efforts, allowing manufacturers to constantly refine and optimize their production processes. It fosters a culture of ongoing development, vital for staying competitive in dynamic market conditions.
- Enabling real-time performance monitoring. Using takt time allows for real-time monitoring of production performance, providing immediate feedback for necessary adjustments. It helps in quickly addressing issues, maintaining the flow of production, and ensuring deadlines are met.
In summary, takt time is vital for creating a balanced, efficient, and responsive manufacturing environment. It’s not just a metric but a philosophy that drives lean production, quality, customer satisfaction, and continuous growth.
The origins and evolution of takt time
The genesis of takt time can be traced back to Germany. The German word ‘Takt’ represents rhythm or pace, a vital concept in creating a harmonious and efficient production line. Post World War I, German industries, notably Hugo Junkers’ aircraft manufacturing, first implemented takt time to ensure timely delivery of aircraft subassemblies.
However, the concept of takt time truly flourished in Japan, where it became integral to the Toyota Production System (TPS). Post-World War II, Toyota, inspired by the German model and Ford’s assembly line methods, refined takt time to suit its lean production system. This blend of German precision and Japanese efficiency transformed takt time into a fundamental tool for modern manufacturing processes worldwide.
When to implement takt time?
Takt time is especially common in continuous flow production processes where a product moves through a chain of workstations, each performing a certain set of tasks. However, it can be implemented in many other scenarios. Here are some situations where takt time would be advantageous:
- High demand consistency. Takt time is most effective in environments where demand does not fluctuate wildly, as it relies on a consistent pace of production.
- Need for process synchronization. When production processes require better synchronization, takt time helps in aligning various stages of production to ensure a smooth flow of operations.
- Improving production efficiency. When there is a need to enhance overall production efficiency by identifying and eliminating bottlenecks and balancing workloads across the production line.
- Customer satisfaction focus. When meeting customer deadlines is critical and there’s a need to align production closely with customer requirements.
- Standardization of processes. When there is a need to standardize processes and establish a consistent rhythm in production, making it easier to train staff and maintain quality.
- Complex supply chains. When the supply chain is complex and there’s a need to precisely manage inventory levels and production schedules.
Implementing takt time should be considered carefully, keeping in mind the nature of the demand, the existing manufacturing processes, and the overall strategic goals of the organization.
Implementing takt time in manufacturing
Implementing takt time in manufacturing involves a series of strategic steps to align production processes with customer demand, ensuring efficiency and minimizing waste. Here’s a step-by-step guide:
- Understand customer demand. The first step is to accurately gauge the demand for your product. This involves understanding your sales cycles, customer expectations, and market trends.
- Calculate takt time. Use the takt time formula: divide the total available production time by the customer demand. For example, if your factory operates 8 hours a day (480 minutes) and the daily demand is 240 units, the takt time is 2 minutes per unit.
- Assess current production capacity. Analyze your current production processes to understand how long it takes to produce one unit. This step is crucial to identify if your current speed can meet the calculated takt time.
- Identify and eliminate bottlenecks. Examine your production line for any bottlenecks that may impede meeting the takt time. This might involve reallocating resources, adjusting workflows, or investing in training and equipment.
- Implement standard work routines. Develop standardized work procedures that align with the takt time. This ensures that every part of the production process is optimized to meet the required pace.
- Continuous monitoring and adjustment. Takt time implementation is not a one-time task. Continuously monitor production performance against takt time and adjust processes as needed. This may involve recalculating takt time based on changing customer demands or production capabilities.
- Train and engage staff. Educate your workforce about takt time and its importance. Their understanding and cooperation are vital for smooth implementation and adherence to takt time principles.
- Use visual aids and real-time tracking. Employ visual management tools and real-time tracking systems like MRP software to keep everyone aware of production pace and targets. This can help in maintaining the rhythm and quickly identifying deviations.
By following these steps, manufacturers can effectively implement takt time, leading to more efficient, lean, and responsive production systems.
MRP software and takt time
MRP systems facilitate the application of takt time by providing detailed planning, scheduling, and inventory management capabilities, ensuring that the materials and capacity required for production are available precisely when needed. This integration allows for a more dynamic and responsive manufacturing process, adapting seamlessly to changes in customer demand.
MRP software can also be used to track processing times per employee or workstation. This enables manufacturing companies to benchmark actual processing times to their takt time, thereby discovering bottlenecks and inefficiencies.
Together, MRP software and takt time form a powerful combination that promotes a culture of continuous improvement, enabling companies to set out on a path of sustainable growth.
Challenges of implementing takt time
Depending on the production process and industry specifics, applying takt time could involve overcoming several challenges:
- Variability in production. Any kind of variability on the shop floor, either in product quality, processing times, disproportionate workloads at workstations, or due to downtime, may have a negative effect on the production line’s ability to meet the takt time benchmarks. Doe to this, time buffers might need to be added to takt time and task distribution needs to be leveled.
- Managing increased demand. When customer demand significantly increases, resulting in a reduced takt time, it necessitates either streamlining tasks to fit the shorter takt time or dividing them across multiple stations. This might involve adding an additional station to the production line, requiring workers to adapt to changes in their work environment.
- Stress on production elements. A shorter takt time can exert significant stress on both automated and non-automated elements of the production system. In automated systems, this increases the likelihood of mechanical breakdowns. For personnel, it can lead to increased physical strain, higher risks of repetitive motion injuries, emotional stress, and potentially reduced motivation, sometimes manifesting as higher absenteeism or more frequent breaks.
While demonstrably effective in many use cases, these risks have to be accounted for before implementing takt time.
The future of takt time in manufacturing
Looking forward, the integration of automation and advanced forecasting methods are set to further refine takt time application. Automation can aid in maintaining the consistency and precision required for effective takt time management. Meanwhile, advanced forecasting tools can predict customer demand more accurately, allowing for more agile adjustments in production scheduling. These advancements promise to make takt time an even more powerful tool in the future.
Key takeaways
- Takt time is a critical concept in lean manufacturing, aligning production with customer demand.
- Takt time is calculated by dividing available production time by customer demand, setting a pace for product completion.
- Takt time is ideal in scenarios with consistent demand and a need for process synchronization.
- A robust MRP system should be implemented to aid in adopting takt time.
- The ability to meet takt time can be affected by production variability, demand volatility, and stress on production systems and personnel.
Frequently asked questions
Takt time is a manufacturing concept used to match the pace of production with customer demand, ensuring that products are produced at a rate that meets demand without overproduction.
Cycle time refers to the total time it takes to complete one production cycle for a product, whereas takt time is the rate at which products need to be completed to meet customer demand.
The formula for takt time is: Takt Time = Available Production Time / Customer Demand.
Takt time is the rate at which products must be finished to satisfy customer demand, while throughput time is the total time taken for a product to pass through the entire production process, from start to finish.
Sources
- Liker, Jeffrey. (2004). The Toyota Way: 14 Management Principles from the World’s Greatest Manufacturer. McGraw-Hill.
- Ducharme, C; Ruddick, T. (2004). Assembly Operations – Takt Time. https://ocw.mit.edu/courses/esd-60-lean-six-sigma-processes-summer-2004/resources/8_1assembly_op/
- Schneider, U; Friedli, T; Basu, P.K, & Werani, J. (2015). Operational Excellence in Practice—the Application of a Takt-Time Analysis in Pharmaceutical Manufacturing. https://www.researchgate.net/publication/272939945_Operational_Excellence_in_Practice-the_Application_of_a_Takt-Time_Analysis_in_Pharmaceutical_Manufacturing
- Vijay, S; Prabha, M.G.. (2020). Work standardization and line balancing in a windmill gearbox manufacturing cell: A case study. https://www.sciencedirect.com/science/article/abs/pii/S221478532036466X