Principal
- FMA
- The Fabricator
- FABTECH
- Canadian Metalworking
Categories
- Additive Manufacturing
- Aluminum Welding
- Arc Welding
- Assembly and Joining
- Automation and Robotics
- Bending and Forming
- Consumables
- Cutting and Weld Prep
- Electric Vehicles
- En Español
- Finishing
- Hydroforming
- Laser Cutting
- Laser Welding
- Machining
- Manufacturing Software
- Materials Handling
- Metals/Materials
- Oxyfuel Cutting
- Plasma Cutting
- Power Tools
- Punching and Other Holemaking
- Roll Forming
- Safety
- Sawing
- Shearing
- Shop Management
- Testing and Measuring
- Tube and Pipe Fabrication
- Tube and Pipe Production
- Waterjet Cutting
Industry Directory
Webcasts
Podcasts
FAB 40
Advertise
Subscribe
Account Login
Search
How serious is your manufacturing company about starting a lean journey?
There's a difference between just dabbling in a few lean manufacturing ideas and taking it seriously
- By Jeff Sipes
- Updated September 30, 2022
- September 30, 2022
- Article
- Shop Management
This is the first of a three-part series where I am going to ask a basic question and then explore that topic. These questions will be extremely timely as we navigate unprecedented times and deal with disruptions thrust upon us as result of the pandemic, geopolitical issues, and social advancements. Read Part II and Part III.
For those of you who are early in or midway through your careers, you may look back on these times as transformative, even as a fork in the road. For those who are in the later stages of your careers, you may be thinking about retirement and the legacy you will leave behind.
Wherever you are, consider the questions in this series and reflect on what your honest and critically derived answers are. This month’s question is: Are you dabbling with a few lean ideas, or are you serious about your lean journey?
Why Is This an Important Question?
To frame this matter, think about lean manufacturing involvement in three levels. You may have done nothing in terms of pursuing the lean body of knowledge as a way to improve business performance. Perhaps the timing is not right, or maybe you’ve decided not to use the approach. That’s the first level of involvement, or lack thereof. You’re essentially doing nothing.
The second level of involvement is to do something—a little here, a little there. People have taken initiative in isolated departments, but you see no evidence of lean application anywhere else. Let’s call that level of involvement dabbling.
The final level of involvement is all in. You see evidence in your performance measures, customer satisfaction, and organizational stress level. The behaviors exhibited by personnel from the shop floor to the top floor indicate the characteristics you would expect from a mature lean organization.
Let’s put the first level of involvement (doing nothing) to the side for purposes of this discussion. Our focus is on the dabbling and serious levels of involvement. These require an investment of time, talent, and treasure, and there is a base to build upon.
So, why is it important to have clarity around the distinction of dabbling and seriousness? Simply put, some people and organizations think they are serious when at best they are dabbling. Their actions and decisions do not match with the lean body of knowledge. They send mixed signals that confuse people both inside (employees) and outside (customers, suppliers, community) the company. They may be knowingly doing this. Or worse, they may really think they are “walking and talking” lean when it may just be a lot of talk.
Getting an honest answer to the dabbling-versus-serious question requires more than a five-minute discussion. Rather, it deserves a more thorough analysis and exploration of both personal and organizational behaviors. It may take several different activities, including personal Gemba walks, surveys for data gathering, group discussions, and other creative mechanisms, to arrive at an honest and useful assessment. Given the forces shaping your company today and into the future, the answer to this question is nothing short of mission critical!
What Is Dabbling?
Dabbling involves superficial or intermittent interest, investigation, or experiment. Some examples help distinguish a lackluster effort from a serious one. They come from anywhere in the organization, but the largest leverage comes from dabbling within the leadership ranks.
What happens when a leader or the whole leadership team voices support for a lean strategy? They publicly stand up and say the right things, and maybe even spend some time developing a closer understanding of the effectiveness of work processes, but then fade into the background. Leaders say “X” but their actions say “Y.” The organization may have started with a vigorous burst, but complacency soon sets in.
What is the result when you create the time for some spot training, maybe in a particular area or on a specific topic, but you fail to follow through? The trainees are exposed to some of the lean body of knowledge. Perhaps they get an opportunity to work on a project or be involved in a kaizen event. Effective follow-through might include some recognition for their efforts, time carved out for them to see the project through to completion, or additional training to reinforce and deepen their lean knowledge so that the initial project was not just a one-time shot. This limited follow-through is a start, but not sufficient for reaching lean growth and maturity.
Dabbling can confuse the workforce into complacency. They have seen these improvement “programs” come and go before. They keep their heads down and wait for it to pass. Additionally, they may find that customers become increasingly dissatisfied with your performance and begin to question your company’s ability to deliver as expected. In these instances, you may damage and erode your credibility, and it’s hard to earn back.
With respect to dabbling and your effectiveness in acting in a manner consistent with lean principles (think about respect for people and operating with humility, for starters), an honest assessment might include taking a look in the figurative mirror. Whom do you see? Do you see a leader who supports lean and process improvement? In your mind, do your actions match the lean message? Most of us see ourselves in positive lights that may or may not match how others in our organizations see us.
Looking in the figurative mirror can be difficult. You may open yourself to unexpectedly harsh feedback. But that honest evaluation can be essential to understanding whether you and your organization are dabbling or serious. If your honest assessment is that you are serious, great. Keep it going. But if your assessment says otherwise, you have a launching point to get serious.
Why Is it Important to Be Serious?
An organization that takes a serious approach to its lean journey will have higher probability of sustainable results and adopt more aggressive practices that enhance competitiveness. If your competitors are pursuing lean seriously and you are dabbling, which company is likely to be in a better marketplace position?
Given the internal and external forces put on companies today, the status quo will be insufficient. To respond effectively, you need to be flexible, and the lean body of knowledge, when applied seriously, will help you adapt.
Regardless of your volumes and predictability of your customers’ demand—low volume, high mix; high volume, low mix; or anything in between—rhythm and flow are achievable if you approach your lean journey in a serious manner. Dabbling in a technique or two will not get you there. Rhythm and flow enable lower stress, greater clarity, and safer workplaces. Be serious.
People will quickly see through your lack of seriousness. Whether you recognize or acknowledge how serious you are, employees will have an understanding, real or perceived. If you are dabbling, they will know it … regardless of what you see in the mirror.
Companies have been thrust into uncharted territory. The question is how they will respond. Do they see an opportunity to position themselves for whatever comes, or do they see a speed bump to navigate around before returning to normal? The companies that seize opportunity will do everything in their power to be serious about their lean journeys. Are you dabbling or are you serious?
About the Author
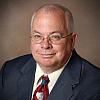
Jeff Sipes
9250 Eagle Meadow Dr.
Indianapolis, IN 46234
(317) 439-7960
subscribe now
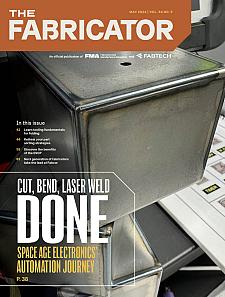
The Fabricator is North America's leading magazine for the metal forming and fabricating industry. The magazine delivers the news, technical articles, and case histories that enable fabricators to do their jobs more efficiently. The Fabricator has served the industry since 1970.
start your free subscription- Stay connected from anywhere
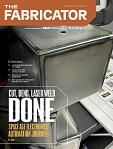
Easily access valuable industry resources now with full access to the digital edition of The Fabricator.
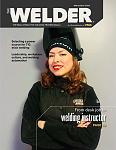
Easily access valuable industry resources now with full access to the digital edition of The Welder.
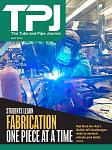
Easily access valuable industry resources now with full access to the digital edition of The Tube and Pipe Journal.
- Podcasting
- Podcast:
- The Fabricator Podcast
- Published:
- 04/16/2024
- Running Time:
- 63:29
In this episode of The Fabricator Podcast, Caleb Chamberlain, co-founder and CEO of OSH Cut, discusses his company’s...
- Trending Articles
Capturing, recording equipment inspection data for FMEA
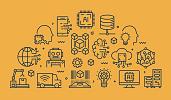
Tips for creating sheet metal tubes with perforations
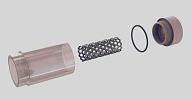
Are two heads better than one in fiber laser cutting?
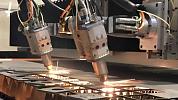
Supporting the metal fabricating industry through FMA
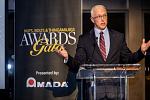
Omco Solar opens second Alabama manufacturing facility
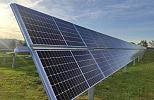
- Industry Events
16th Annual Safety Conference
- April 30 - May 1, 2024
- Elgin,
Pipe and Tube Conference
- May 21 - 22, 2024
- Omaha, NE
World-Class Roll Forming Workshop
- June 5 - 6, 2024
- Louisville, KY
Advanced Laser Application Workshop
- June 25 - 27, 2024
- Novi, MI