- FMA
- The Fabricator
- FABTECH
- Canadian Metalworking
Categories
- Additive Manufacturing
- Aluminum Welding
- Arc Welding
- Assembly and Joining
- Automation and Robotics
- Bending and Forming
- Consumables
- Cutting and Weld Prep
- Electric Vehicles
- En Español
- Finishing
- Hydroforming
- Laser Cutting
- Laser Welding
- Machining
- Manufacturing Software
- Materials Handling
- Metals/Materials
- Oxyfuel Cutting
- Plasma Cutting
- Power Tools
- Punching and Other Holemaking
- Roll Forming
- Safety
- Sawing
- Shearing
- Shop Management
- Testing and Measuring
- Tube and Pipe Fabrication
- Tube and Pipe Production
- Waterjet Cutting
Industry Directory
Webcasts
Podcasts
FAB 40
Advertise
Subscribe
Account Login
Search
Transitioning from bottom bending to air forming on the press brake
Never underestimate the importance of training in metal fabrication shop
- By Steve Benson
- October 11, 2023
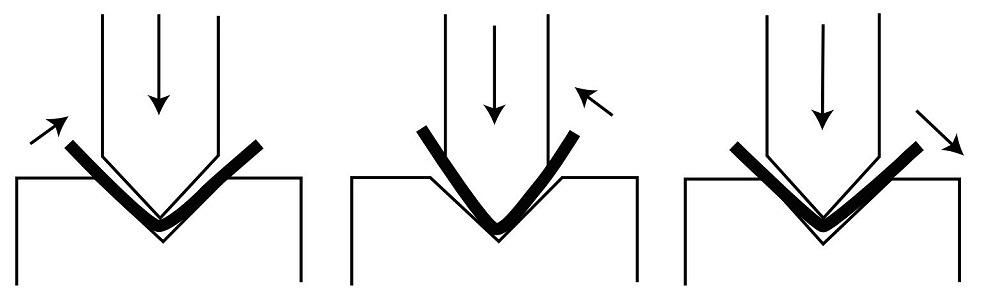
FIGURE 1. In bottoming, the punch applies downward force as the material wraps around the punch body (center), then continues to apply pressure to force the material against the die angle (right).
Question: I work for a high-precision defense and aerospace machine shop. We have always bottom-bent our sheet metal parts but recently have tried air bending. I find it difficult to control tight tolerances, and we may get a few good and then a few bad parts. It seems like there is no constant accuracy with air bending. Does this statement seem correct? Should we be sticking to bottom bending?
Answer: Your statement sounds correct, and this perception of air forming is quite common. Bottom bending is completely different from air forming. Because the forming methods are so different, from part design and layout to operations on the shop floor, you need to review and design the pieces you work with for your forming method of choice. If a part is designed to be bottom-bent, it must be bottom-bent. If it is intended for an air form, it must be bent as an air form.
Analyzing the choice between bottom bending and air bending in sheet metal involves looking at various technical aspects of the parts to be produced and the production requirements for those parts. Both methods have their place and take time to learn. However, everything you know or experience with a given forming method generally is not transferable to the other.
Bottom Bending Advantages
Bottom bending offers superior control over tight tolerances. The die’s inside angle provides the set angle of the finished bend. To get to the set angle with a bottom bend, the material is brought up to the required angle, plus an amount to compensate for springback. At this point, rather than releasing the bend, the operator drives the punch nose further into the material and forces the bend to open, a phenomenon known as negative springback or springforward. This opening of the bend angle continues until the metal reaches the angle set by the die, usually 90 degrees (see Figure 1).
Because you have angular clearance between the die angle and punch angle, the punch nose can be forced further into the material without the tonnage requirements of coining, which has no angular clearance and very high tonnage requirements (see Figure 2).
Springback, or the tendency of the material to return to its original shape after bending, is easier to predict and manage with bottom bending. The better predictability helps achieve accurate final dimensions. For this reason, bottom bending is often preferred for parts with intricate geometries or critical tolerances. The die’s support ensures uniform deformation across the part’s profile.
While skill is very much required, bottom bending tends to be less operator-dependent than air forming is, simply because it deals with material variables (such as slight differences in hardness or thickness) through the use of force. Assuming you use precision-ground tooling rather than planer tools, bottom bending typically involves shorter setup times, which can impact production efficiency with quicker setups, especially on smaller runs. Planer tools are much harder to use, especially where setups involve the staging of tooling across the press brake bed.
Bottom Bending Disadvantages
Bend angles other than 90 degrees will require specialized dies, and tooling can lead to higher initial costs, particularly if the part design changes frequently. Also, since the material comes into direct contact with the die, marking on the bend’s outside surface can be a concern, especially for visible or finished surfaces. Without highly skilled operators that truly understand the bottoming process and how to perform it, you risk serious damage to the press brake and tooling from overloading.
I have just scratched the surface here. There is much more to bottom bending and how to do it correctly and safely, so training is highly advised.
FIGURE 2 Coining, with no angular clearance between the punch and die, has very high tonnage requirements.
Advantages of Air Forming
Air bending offers quicker setup and tooling changes, making it advantageous for jobs with varying bend angles or short production runs. This flexibility could reduce downtime and increase overall efficiency—if it wasn’t for the material variables, which we will discuss in a moment.
Air bending with precision-ground tooling can lead to cost savings over time, especially compared to bottom bending, because air bending has fewer specialized tooling requirements. This is true even though precision-ground press brake tooling is expensive; the tooling will pay for itself in labor savings once the learning curve has passed.
An air forming operation contacts the material at three points: the two die shoulder radii and the punch tip (see Figure 3). The material doesn’t interact with the tooling as much as it does in bottoming. Air bending can result in fewer marks on the surface, which is good for parts requiring cosmetic finishing. With little direct contact between the material and the die faces, air bending tools tend to experience less wear and last longer.
Air Forming Challenges
Achieving consistently tight tolerances can be more challenging in air bending because the bend is “floated” rather than “stamped.” Variations in material thickness, tensile and yield strengths, grain direction, and other properties introduce a lot of inconsistencies.
Variations in material properties from batch to batch can affect bend accuracy, making careful material selection and testing crucial. Evaluate the geometry of your parts. Bottom bending might be more appropriate for intricate designs or critical tolerances to maintain accuracy.
Like bottom bending, air bending demands skilled operators who understand the nuances of adjusting parameters such as the bend angle, material thickness, and pressure to mitigate variations. Skilled operators are essential for achieving accurate results in air bending. So is having good, up-to-date equipment. Evaluate your team’s expertise and training resources.
If your parts require precise tolerances, bottom bending’s predictable springback could be advantageous. However, with careful setup and skilled operators, air forming’s accuracy can be improved. Bottom bending might be preferable for high-volume production with consistent parts due to its reliability. Air bending suits shorter runs and dynamic requirements.
The Weak Link: Material
Specific materials respond to bending differently, and it is a given that no two pieces of material are the same—sheet to sheet, batch to batch, manufacturer to manufacturer. Every material has a tolerance zone. For example, 16-ga. steel can be anywhere between 0.053 and 0.067 in. thick. A36 steel has a minimum yield strength of 36,000 PSI, yet it can go up to 41,000 PSI and still be called A36; that’s a 13% increase in strength. Such variations in strength or thickness can cause several degrees of bend angle variation.
Grain direction is an additional issue. Is your material anisotropic (has a grain structure)? Is it a heavy grain or fine? Are you bending with or against the grain? It all makes a big difference.
Evaluating these issues starts in engineering. And that begins with the engineer going to the shop floor, talking with the operators, and finding out their opinions. Find out which jobs and materials are best used with which method of forming. Get a list of the available tooling, die widths, die angles, punch radii, and punch angles. From there, design to those parameters.
FIGURE 3. Air forming contacts the material at three points: the two die shoulder radii and the punch tip. The radius forms as a percentage of the die opening.
With bottom bending, you can send the job to the shop floor and allow the press brake operators to choose the tooling they prefer. Bottoming works because the radius on the punch nose is bottomed into the material. That punch nose radius is also used to calculate the bend allowance and bend deduction.
Air forming is entirely different. The bend radius is developed as a percentage of the die width, and it’s that radius that’s used to calculate the bend deduction and bend allowance. Information about which die width was used for the calculation is what needs to be used to build the parts. If you’re air forming, and you allow each operator to use whatever die they want, you will have a wide variety of finished pieces from the same flat blank.
Air forming will require experimentation to fine-tune the process. Consider whether you should allocate resources for process refinement. Engage with experts, tooling suppliers, and peers in the field to gain insights into best practices.
For the Long Term, Go With Air Forming
As a mechanical engineer, your decision should be driven by the complexity of your parts, the required tolerances, production volume, operator capabilities, and the resources you’re willing to invest in process optimization. While bottom bending provides greater accuracy and consistency, air bending’s flexibility and potential cost savings make it a viable option, as long as you adjust your operation appropriately and have the skilled operators to make it happen.
I don’t know much about your shop and what types of tooling and press brakes you are working with, but if possible, try using both methods in your product mix. That said, when air forming, only use the best press brakes designed for precision-ground tooling.
Air forming is the future, and long-term, air forming is the way to go. Make the investment to train everyone, including your engineers and operators. If you want to lessen the time and pain involved in your transition to air forming, the importance of training cannot be overstated.
subscribe now
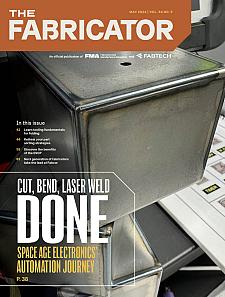
The Fabricator is North America's leading magazine for the metal forming and fabricating industry. The magazine delivers the news, technical articles, and case histories that enable fabricators to do their jobs more efficiently. The Fabricator has served the industry since 1970.
start your free subscriptionAbout the Author
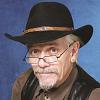
Steve Benson
2952 Doaks Ferry Road N.W.
Salem, OR 97301-4468
503-399-7514
Related Companies
- Stay connected from anywhere
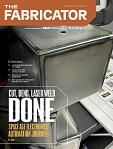
Easily access valuable industry resources now with full access to the digital edition of The Fabricator.
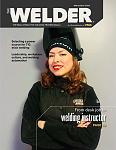
Easily access valuable industry resources now with full access to the digital edition of The Welder.
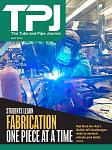
Easily access valuable industry resources now with full access to the digital edition of The Tube and Pipe Journal.
- Podcasting
- Podcast:
- The Fabricator Podcast
- Published:
- 04/16/2024
- Running Time:
- 63:29
In this episode of The Fabricator Podcast, Caleb Chamberlain, co-founder and CEO of OSH Cut, discusses his company’s...
- Industry Events
16th Annual Safety Conference
- April 30 - May 1, 2024
- Elgin,
Pipe and Tube Conference
- May 21 - 22, 2024
- Omaha, NE
World-Class Roll Forming Workshop
- June 5 - 6, 2024
- Louisville, KY
Advanced Laser Application Workshop
- June 25 - 27, 2024
- Novi, MI