3 advanced motor management enablers to reduce cost and downtime
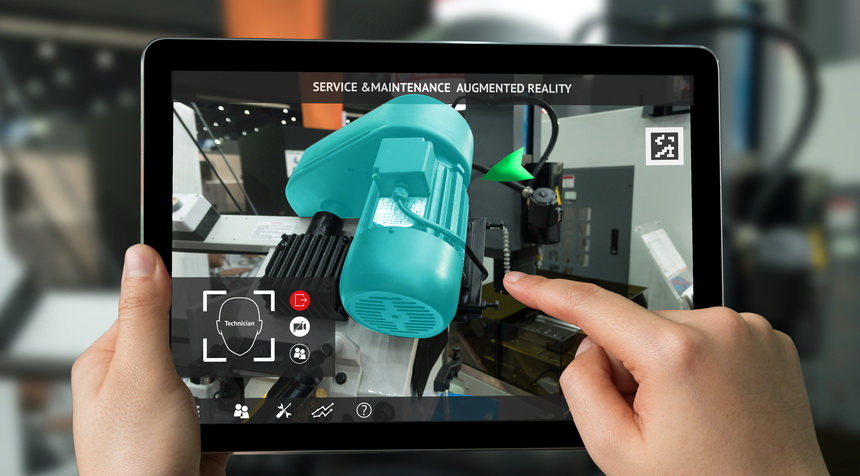
[Source: Shutterstock]
Electric motors consume about 60% of the electricity used by manufacturing industries. Moreover, for heavy industries this proportion can ramp up to 90%. Adopting advanced motor management principles reduces both energy use and motor related downtimes.
Yet, ofttimes users do not apply modern energy management principles to help reduce consumption. Industrial electric motors drive critical infrastructure assets such as conveyor belts, pumps, compressors, agitators, fans, and others. Yet, according to Schneider Electric, despite their key operational role, traditional motor management often fails to optimise performance.
This results from a piecemeal approach that focuses on individual motors, rather than taking a more holistic view. In other cases, motor maintenance is reactive. Only after downtime occurs do users marshal resources to address the issue and the costly downstream delays. Today’s challenge for plant operators is better control of motor energy costs whilst retaining operational resilience. From plant stoppages, damage to equipment, and risk to people or even the environment, motor failure can be expensive and slow to resolve.
Having one strategy that integrates motor control and protection solutions can help plants reduce costs while increasing production. Robust connection and communication between the motor and the automation systems plays a key role in minimising motor failure. Moreover, when monitoring energy data from motors to better align performance to the workload, overall energy costs fall.
Key enablers for migrating to advanced motor management
Implementing a more holistic and advanced motor management strategy takes careful planning and the right combination of technologies. Companies have failed to pursue the integration of motor control, automation, and energy systems because of the perceived technical complexities.
However, trends like digitisation and IIoT using advanced connectivity make the implementation of an advanced motor management strategy practicable. Key elements of this include:
1. Application-oriented tools
For machine builders who source their motorised solutions, efficiencies increase when core machine components are easy to select, install, wire, commission, and remote maintenance. When designing and configuring a solution, rather than accessing multiple catalogues to identify products to build a motor management architecture (e.g., circuit breakers, contactors, overload relays, drives) and then writing down the proper part numbers for ordering, automated configuration tools now allow OEMs, panel builders, and even end users to generate quick and comprehensive solutions. These tools have proven to reduce design and selection time by up to 40%.
For heavy industry applications, large motors also affect the electrical design. The ability to check the appropriate transformer size, select a starting solution, or deal with power quality improvement is critical to making the right early design decisions. The proper engineering tools designed around these needs are the answer to such constraints.
2. Collecting energy performance data
When connecting devices, such as Altivar Process service-oriented drives to motors, their onboard intelligence controls the motor at the best efficiency point, helping to reduce electrical consumption by at least 30%. Furthermore, intelligent motor starters, like TeSys Island, and digital load management solutions make it much easier to optimise machine performance.
Each load feeder can provide data to optimise the machine and the process, as well as provide actual line current data. These devices offer machine builders the option of local and remote monitoring of installed devices. They also provide their clients with a cloud-based predictive maintenance service and monetise the accessible load asset data.
3. Software analytics
With intelligent motor management solutions in place, maintenance personnel no longer need to be near asset components to troubleshoot them. Pre-alarming based on pre-set parameters allows the addressing of abnormal situations before they cause a production stoppage. Dedicated software solutions like EcoStruxure Asset Advisor analyse collected data to help predict future performance of the customer’s assets.
The total cost of ownership improves with advanced analytics to identify potential failure modes via actionable web dashboards, timeline reports, and recommendations with operational support for people on-site.
Recent blog posts