Editor-in-Chief
- FMA
- The Fabricator
- FABTECH
- Canadian Metalworking
Categories
- Additive Manufacturing
- Aluminum Welding
- Arc Welding
- Assembly and Joining
- Automation and Robotics
- Bending and Forming
- Consumables
- Cutting and Weld Prep
- Electric Vehicles
- En Español
- Finishing
- Hydroforming
- Laser Cutting
- Laser Welding
- Machining
- Manufacturing Software
- Materials Handling
- Metals/Materials
- Oxyfuel Cutting
- Plasma Cutting
- Power Tools
- Punching and Other Holemaking
- Roll Forming
- Safety
- Sawing
- Shearing
- Shop Management
- Testing and Measuring
- Tube and Pipe Fabrication
- Tube and Pipe Production
- Waterjet Cutting
Industry Directory
Webcasts
Podcasts
FAB 40
Advertise
Subscribe
Account Login
Search
A metal fabricator's guide to bringing powder coating in-house
It’s not as easy as just adding equipment; costs, systems, and processes must be clear
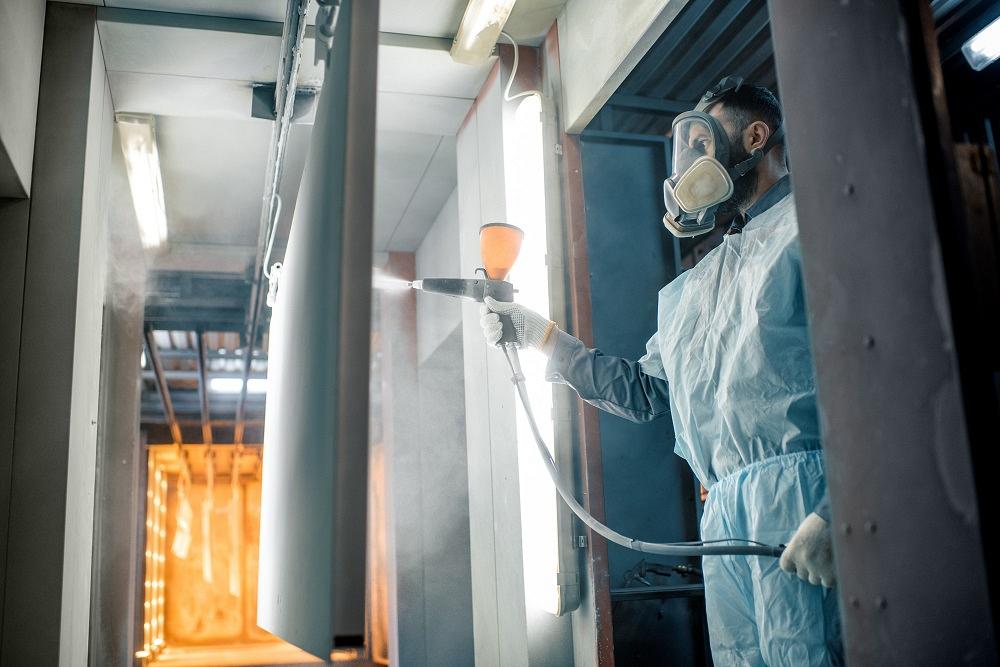
When metal fabricators bring powder coating in-house, they gain control over finish quality of parts and the schedule. That’s an attraction for a lot of shops, but plenty of reasons exist as to why most fabricators stay away from the process. Bringing in powder coating is not as easy as simply adding a piece of equipment. RossHelen/iStock/Getty Images Plus
The motivations to add powder coating capabilities are many, but the number of metal fabricators that do are small. Even with that lack of widespread adoption, some shops still feel obligated to at least consider the addition of the finishing process. For them, it’s about control.
That’s the way Rich Saddler sees it. He’s got more than 30 years of experience in finishing, both liquid and powder coating, with several of those years being spent in the very meticulous office furniture industry. Today, he runs a finishing consultancy because, as he described it, “there aren’t a lot of people where you can say, ‘Help me build this finishing line.’”
For the sake of this discussion, the focus is on powder coating, because it doesn’t generate harmful solvents or airborne pollutants. The environmental friendliness of the process typically appeals to job shops because permitting in most North American municipalities is not as big of a deal when compared to liquid processes that might actually involve solvents and potentially other pollutants.
With that in mind, Saddler pointed out all of the parties involved in the possible implantation of such a line: the pretreatment chemical suppliers, the pretreatment/application booth builder, application gun vendor, the curing oven builder, and the actual powder coating material supplier. That’s a lot of parties and rarely will one step forward to offer guidance on other aspects of the overall process.
If a metal fabricator is looking to bring powder coating in-house, it has a daunting task ahead of it when trying to make the right decision. Hopefully this guide can help.
What’s the Cost Justification?
Metal fabricators that have made the move to powder coating many times have done it because their outsourcing bill to the custom powder coater down the street reached a level that became too much to ignore. That dollar amount likely differs among fab shops, but most have some idea, unless they have a stellar relationship with the custom coater.
Saddler said, from his experience, most metal fabricators justify the investment in a powder coating system because they are able to gain more control over the process. The companies don’t lose days to transportation, and quality risks are reduced because they don’t have to load parts onto a truck and then unload the finished parts when the shipment is returned.
“Most of the time, what I’ve seen is that it’s all about logistics—the timing of getting things back and forth and being able to meet customer demands and schedules,” he said.
Delays in delivering parts on time because of problems getting jobs back from a custom coater can lead to financial penalties, which then can be used to justify a possible powder coating system investment. There’s also rework that might be linked to quality issues. But both areas are more related to customer satisfaction and retention.
To get at a true idea of just what will be needed for an investment, which then can be juxtaposed to the annual spend on outsourced custom coating services, Saddler said a shop needs to know how large of a system is needed, how many people are needed to run it, and how many parts likely will be finished. And that’s just the start.
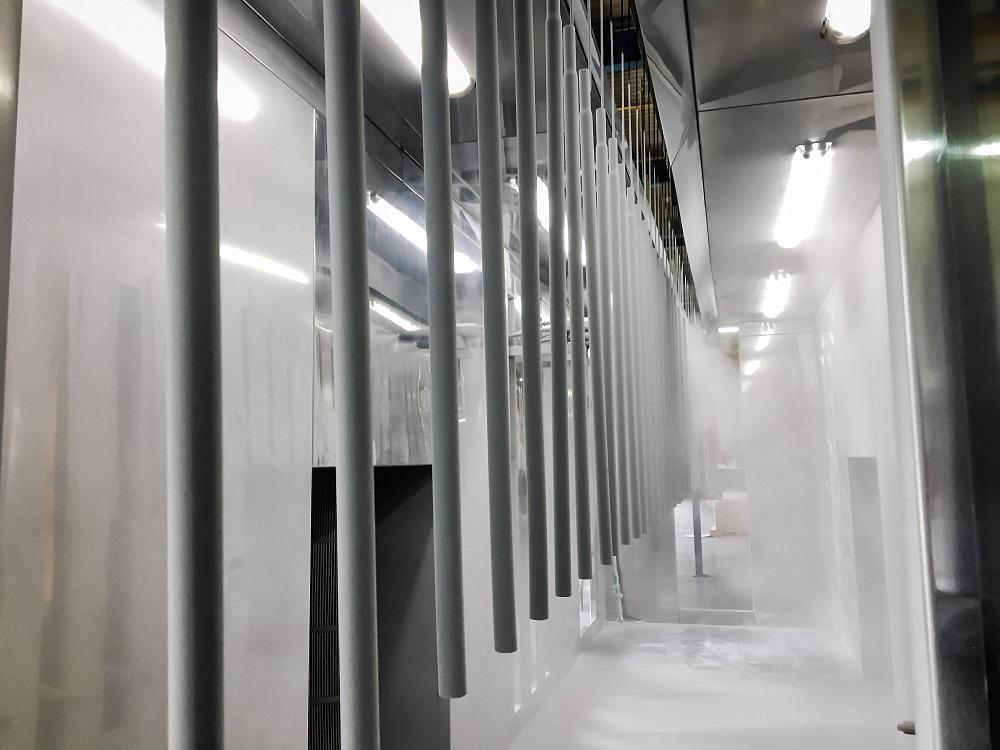
Metal parts need to be properly pretreated before the application of powder occurs. This is just one part of the system that is required to ensure that the powder coating adheres to the metal for a long time. AlexanderLipko/iStock/Getty Images Plus
The amount and size of the parts to be powder coated dictate the size of the system that is needed. Estimates from system integrators or from companies that supply the separate components of a powder coating system establish the investment needed for equipment.
Once the size is determined, the amount of people required to run it can be figured out. Any salaries or wages associated with the new workers make up the labor cost for running a powder coating operation.
The estimate on the number of parts to be powder coated allows a metal fabricator to determine just how much surface area needs powder coverage. That figure and the estimated price per pound for powder material provides a base figure for how much of a material investment is needed.
Then a metal fabricator has to take into account such additional costs as utilities, packaging, and ancillary supplies.
“Obviously, it always boils down to dollars and cents,” Saddler said.
That leads to a major question for the metal fabricator: What’s the biggest headache—investing in and running a powder coating line or living with the variabilities associated with outsourcing powder coating services?
Labor Concerns
If a metal fabricator thinks it is going to find the expertise to guide the setup and run the powder coating operation for $15/hour, it will be woefully disappointed. That type of expertise is hard to find in general, and it’s the main reason that Saddler offers his consulting services.
“If you look at welding, I can go to welding school to learn how to do it, and I can go to college to learn about metallurgy and how welding can affect the metal. You can go to high school and even learn about welding,” he said. “But how many people understand paint particles and powder coating? They might be familiar with painting a fender on a motorcycle or whatever, but that’s not what we’re talking about. We’re talking about industrial finishing.”
The search for people to operate the line is going to be a challenge as well. The lack of potential job applicants interested in working in manufacturing is well-known, and the trend is widespread. Finding finishing technicians has been an uphill battle for quite a long time, and it hasn’t gotten any easier.
The knee-jerk reaction of any metal fabricator challenged with trying to find workers is to consider automation. That’s completely possible when it comes to powder application, but even that requires a skill set that is not well-represented in the pool of potential workers.
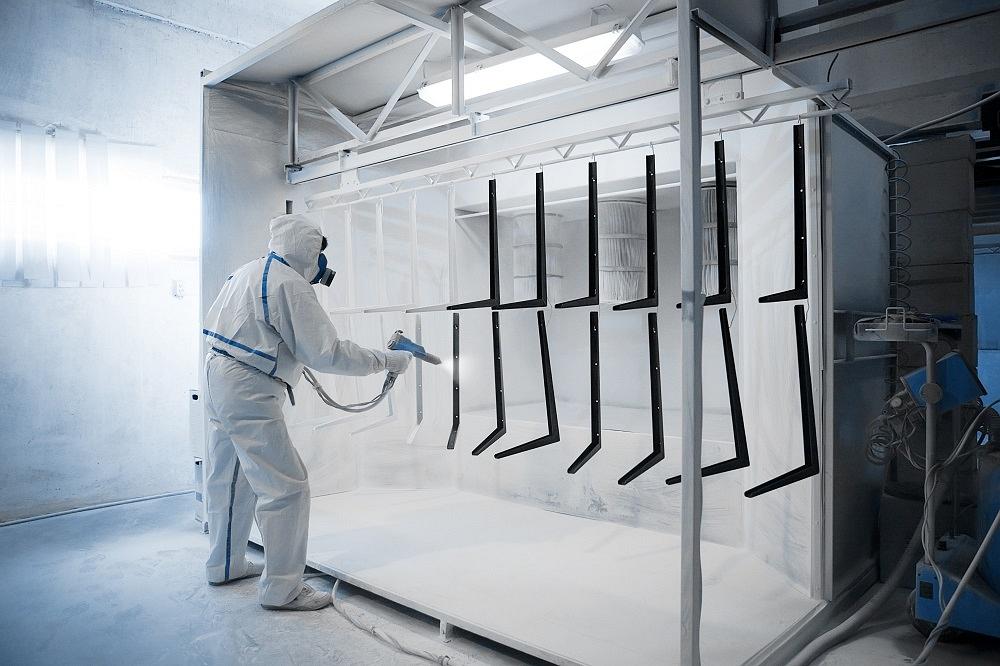
A batch powder coating system is attractive for those shops that don’t need to finish thousands of parts per shift. DingaLT/iStock/Getty Images Plus
Saddler said that in the instances where automated powder coating systems are being considered, someone is going to have to teach the robotic arms how to move for proper powder coating coverage and when the guns should be turned on and off. That means knowing how the powder coating needs to be applied to achieve the desired coating thickness and complete coverage and having the expertise to work with the robots.
“Having a background in knowing how to finish a part successfully is important,” he said.
The other alternative is having automated guns apply a cloud of powder as parts are conveyed through a booth. Because of the electrostatic principles that govern the powder coating process (the charged metal parts attract the electrostatically charged powder particles and they then cling to the metal surface), the parts get coated, but overspray is likely going to be a result. (Recycling of powder material adds another layer of complexity to powder coating systems.)
In either scenario, someone is still needed to load and unload parts of racks. Fully removing humans from the powder coating process is difficult.
Batch or Conveyorized?
“Usually, this type of system is a monument,” Saddler said, when describing a large conveyorized powder coating system. His point: Once it’s built, it typically remains where it is.
He reflected on one of the first projects he ever worked on, where he and a couple of engineers were charged with building a paint system for an office furniture OEM. The system, which occupied a building expansion, still stands today in the place it was originally set up. The application equipment has been modernized, but the same stainless steel washer and the same paint booths are still there.
“Twenty years down the road, you will have moved presses, the welding department, and the assembly area around, but the paint system is still right where it was,” Saddler said.
That’s why a lot of shops start off with a batch operation. Obviously, the volume of powder-coated parts has to make sense because material handling for this type of setup is reliant on carts pushed from one area to the next.
But that’s also the attraction for such an approach to powder coating. A pretreatment area, an application booth, and an oven—they aren’t connected. They can be moved to fit in corners and, basically, be out of the way. They aren’t monuments like the conveyorized systems. Batch systems can be designed to fit into tight or awkward plant layouts.
The System Changes the Process Flow
Metal fabricators know what a bottleneck is. Work-in-process lining the floor waiting to be moved forward in the manufacturing process is the universal sign. The locations, however, can differ. Sometimes it can be the welding department because of key absences. Other times it can be the bending department because new laser cutting equipment is overwhelming the antiquated press brakes, which don’t bend parts fast enough.
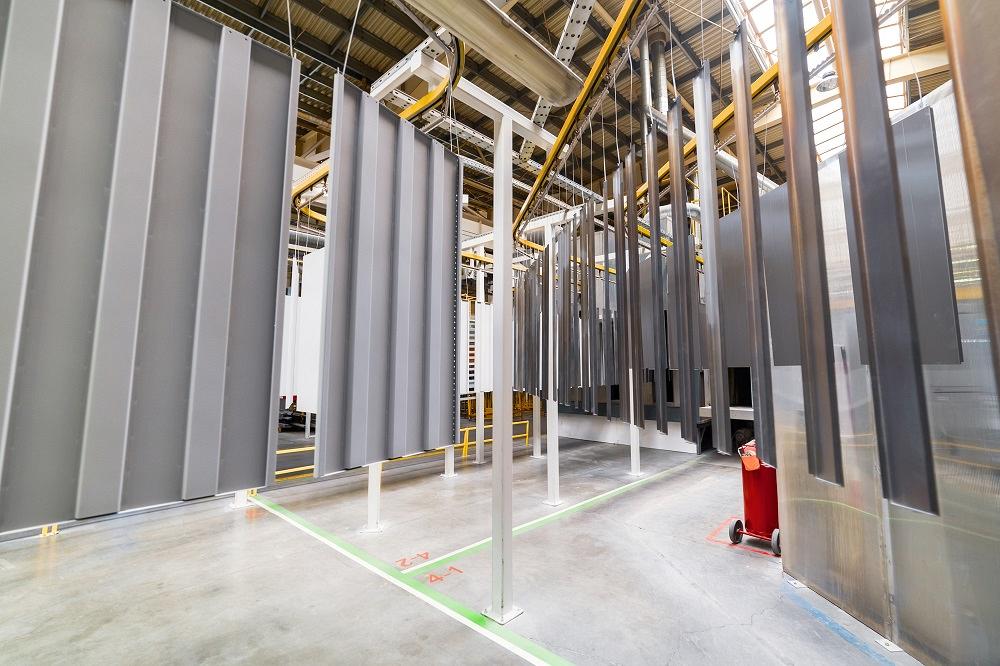
Conveyorized powder coating systems require plenty of square footage to accommodate a lot of parts and room for them to circulate and cool down after curing, which allows workers to handle them safely. Nordroden/iStock/Getty Images Plus
The powder coating line is the ultimate bottleneck. If it goes down for any reason, everything stops because a metal fabricator isn’t likely to have a second line as a backup.
“You might spend millions of dollars to build a system, and you only make one of them. If it goes down, everybody knows it,” Saddler said.
Final Advice
Companies that take on in-house powder coating are assuming plenty of risk, but that’s nothing new to metal fabricators, who routinely have to make decisions about investing thousands of dollars in new equipment to retain customers or chase after new ones. Fabricators also are problem-solvers by nature, and while they might not know much about powder coating at first, they are fast learners. Despite all of the reasons to leave powder coating in the hands of the experts who have built businesses delivering this one function, metal fabricators that feel it necessary to set up a powder coating operation won’t be deterred.
With that in mind, Saddler recommends that metal fabricators looking to bring powder coating in-house find a team of suppliers who are willing to offer their expertise. Solid guidance can prepare a path that sets up a shop for powder coating success.
“But, in the end, you’re ultimately responsible,” Saddler added.
A metal fabricator has to stand behind its metalworking results. If the shop starts powder coating, it’ll need to offer the same commitment to quality results as it relates to the finish.
About the Author
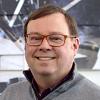
Dan Davis
2135 Point Blvd.
Elgin, IL 60123
815-227-8281
Dan Davis is editor-in-chief of The Fabricator, the industry's most widely circulated metal fabricating magazine, and its sister publications, The Tube & Pipe Journal and The Welder. He has been with the publications since April 2002.
subscribe now
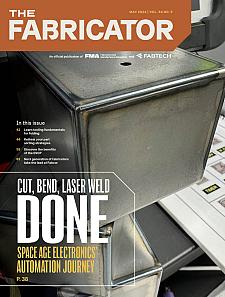
The Fabricator is North America's leading magazine for the metal forming and fabricating industry. The magazine delivers the news, technical articles, and case histories that enable fabricators to do their jobs more efficiently. The Fabricator has served the industry since 1970.
start your free subscription- Stay connected from anywhere
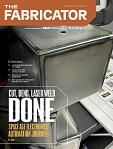
Easily access valuable industry resources now with full access to the digital edition of The Fabricator.
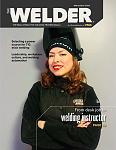
Easily access valuable industry resources now with full access to the digital edition of The Welder.
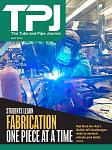
Easily access valuable industry resources now with full access to the digital edition of The Tube and Pipe Journal.
- Podcasting
- Podcast:
- The Fabricator Podcast
- Published:
- 04/16/2024
- Running Time:
- 63:29
In this episode of The Fabricator Podcast, Caleb Chamberlain, co-founder and CEO of OSH Cut, discusses his company’s...
- Industry Events
16th Annual Safety Conference
- April 30 - May 1, 2024
- Elgin,
Pipe and Tube Conference
- May 21 - 22, 2024
- Omaha, NE
World-Class Roll Forming Workshop
- June 5 - 6, 2024
- Louisville, KY
Advanced Laser Application Workshop
- June 25 - 27, 2024
- Novi, MI