Senior Editor
- FMA
- The Fabricator
- FABTECH
- Canadian Metalworking
Categories
- Additive Manufacturing
- Aluminum Welding
- Arc Welding
- Assembly and Joining
- Automation and Robotics
- Bending and Forming
- Consumables
- Cutting and Weld Prep
- Electric Vehicles
- En Español
- Finishing
- Hydroforming
- Laser Cutting
- Laser Welding
- Machining
- Manufacturing Software
- Materials Handling
- Metals/Materials
- Oxyfuel Cutting
- Plasma Cutting
- Power Tools
- Punching and Other Holemaking
- Roll Forming
- Safety
- Sawing
- Shearing
- Shop Management
- Testing and Measuring
- Tube and Pipe Fabrication
- Tube and Pipe Production
- Waterjet Cutting
Industry Directory
Webcasts
Podcasts
FAB 40
Advertise
Subscribe
Account Login
Search
Breaking down the information silos at FABTECH
The metal fabrication industry needs transparency
- By Tim Heston
- November 8, 2022
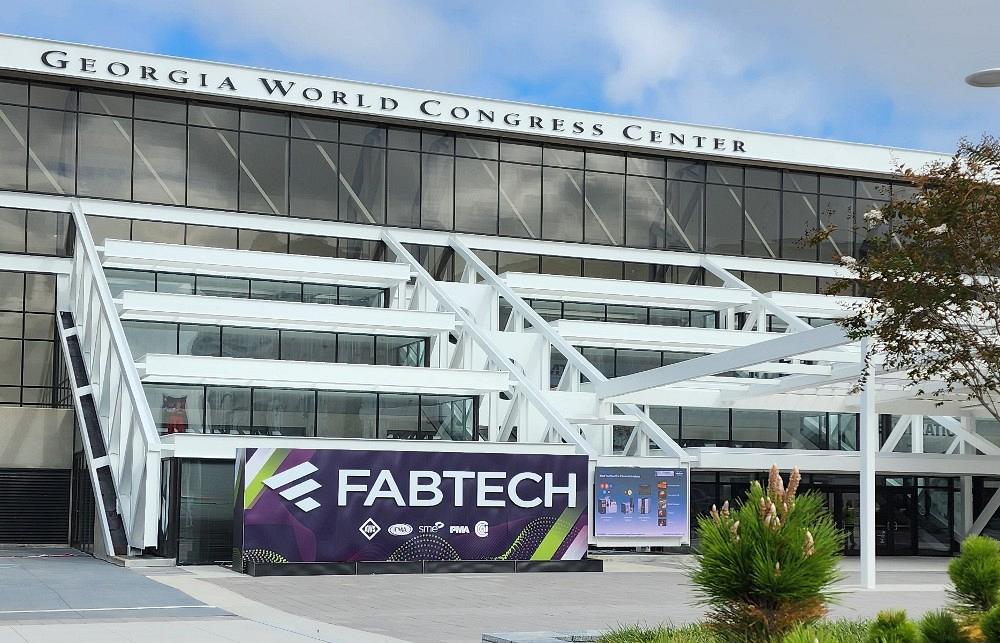
FABTECH was held in Atlanta four years ago, and it returns to the Georgia World Congress Center this week. Gareth Sleger
Imagine walking on a custom metal fabricator’s shop floor in 2022. You probably see a hive of activity: lasers cutting, press brakes bending, welders welding. People are working through the backlog, trying their best to catch up. You also might see piles of work in process (WIP), and a lot of them look like they’ve been sitting there for some time.
Ask around and you’ll find WIP is gathering dust not because some upstream process made too many parts, or because a downstream constraint in welding, powder coating, or assembly. It’s because of some purchased component, like a piece of hardware, isn’t available.
This is what choked supply chains look like from the ground level. As this year’s FABTECH show gears up at the Georgia World Congress Center in Atlanta this week, tens of thousands of fabricators will converge and look for ways to ensure they can deliver, even amid mayhem in the broader supply chain.
Some will be looking for equipment that helps get more out of the expertise they have. As always, flexibility will be paramount. Fabricators want to be able to drop in a program to a laser, perhaps a press brake with automatic tool change, produce a hot job, then return to the production order at hand.
The metal fabrication business is no stranger to the hot job. It’s the nature of the beast. But as the supply chain recovers and interest rates (and, hence, the cost of money) rise, shop managers are scrutinizing that WIP and supply-chain delays in general.
When it comes to WIP in particular, if hardware wasn’t available, why was the job released in the first place? For that matter, why wasn’t the lack of hardware known when initial promises were made, when the quote was submitted and the customer accepted?
”There’s a lack of connectivity across the industrial supply chain. And as you move through the tiers of the industrial supply chain, the quality of information declines. We can fix that problem.”
That was Jason Ray, CEO and co-founder of Boston-based Paperless Parts, a cloud-based quoting platform. Dring a pre-FABTECH interview, Ray described an industry supply chain with a serious lack of transparency. On top of this, information tends to degrade the farther down the tiers you go. Designers start with a powerful 3D-CAD file, then convert to a STEP file as they start the procurement process. Lower-tier suppliers, including many precision sheet metal fabricators, are left with a PDF. Sometimes they can get a 3D-CAD file, sometimes not.
Ray described how little information some vendors receive, especially outside service providers. Plating companies might get a redacted print. The plating provider’s vendors might just get a bill of materials (BOMs). A metal service center just gets a text message for an order, with no information about what that material will eventually become. “There are a million different ways you could drive an enormous amount of collaboration through a common digital thread,” he said.
The idea of the digital thread has been talked about for years. “We now connect the machines in our facilities. We need to build an industrial cloud to collect data from machines and perform a deep analysis. And we’re creating a digital thread to communicate with customers and supply chain partners.”
That was said at a keynote during FABTECH 2015 by Karen Kerr, who at the time was managing director of GE Ventures. Her comment rings true today, and many attendees at FABTECH 2022 hope to inch at least a little closer to that ideal. To make this happen will require equipment and software connectivity and interoperability.
Flexible equipment—everything from integrated cutting and bending centers to press brakes that can be automated for one run, then switch to manual operation the next—has made industry headlines during the past decade. Some of that flexibility is needed to meet customer demand, but let’s be honest, some quick changeovers occur because people dropped the ball several rungs up the supply chain, and so now everyone’s scrambling.
Why did they drop the ball? Because they operate in information silos. The industry needs more technologies that help break down those information silos, not just within a fabricator’s four walls, but throughout the supply chain.
subscribe now
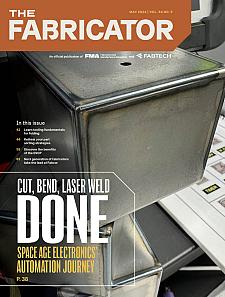
The Fabricator is North America's leading magazine for the metal forming and fabricating industry. The magazine delivers the news, technical articles, and case histories that enable fabricators to do their jobs more efficiently. The Fabricator has served the industry since 1970.
start your free subscriptionAbout the Author
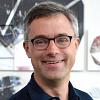
Tim Heston
2135 Point Blvd
Elgin, IL 60123
815-381-1314
Tim Heston, The Fabricator's senior editor, has covered the metal fabrication industry since 1998, starting his career at the American Welding Society's Welding Journal. Since then he has covered the full range of metal fabrication processes, from stamping, bending, and cutting to grinding and polishing. He joined The Fabricator's staff in October 2007.
- Stay connected from anywhere
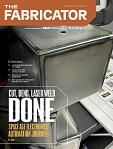
Easily access valuable industry resources now with full access to the digital edition of The Fabricator.
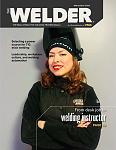
Easily access valuable industry resources now with full access to the digital edition of The Welder.
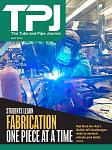
Easily access valuable industry resources now with full access to the digital edition of The Tube and Pipe Journal.
- Podcasting
- Podcast:
- The Fabricator Podcast
- Published:
- 04/16/2024
- Running Time:
- 63:29
In this episode of The Fabricator Podcast, Caleb Chamberlain, co-founder and CEO of OSH Cut, discusses his company’s...
- Trending Articles
Tips for creating sheet metal tubes with perforations
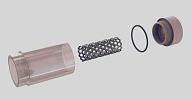
Supporting the metal fabricating industry through FMA
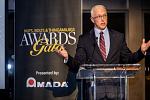
JM Steel triples capacity for solar energy projects at Pennsylvania facility
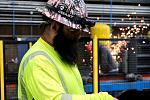
Are two heads better than one in fiber laser cutting?
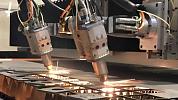
Fabricating favorite childhood memories
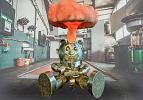
- Industry Events
16th Annual Safety Conference
- April 30 - May 1, 2024
- Elgin,
Pipe and Tube Conference
- May 21 - 22, 2024
- Omaha, NE
World-Class Roll Forming Workshop
- June 5 - 6, 2024
- Louisville, KY
Advanced Laser Application Workshop
- June 25 - 27, 2024
- Novi, MI