Editor
- FMA
- The Fabricator
- FABTECH
- Canadian Metalworking
Categories
- Additive Manufacturing
- Aluminum Welding
- Arc Welding
- Assembly and Joining
- Automation and Robotics
- Bending and Forming
- Consumables
- Cutting and Weld Prep
- Electric Vehicles
- En Español
- Finishing
- Hydroforming
- Laser Cutting
- Laser Welding
- Machining
- Manufacturing Software
- Materials Handling
- Metals/Materials
- Oxyfuel Cutting
- Plasma Cutting
- Power Tools
- Punching and Other Holemaking
- Roll Forming
- Safety
- Sawing
- Shearing
- Shop Management
- Testing and Measuring
- Tube and Pipe Fabrication
- Tube and Pipe Production
- Waterjet Cutting
Industry Directory
Webcasts
Podcasts
FAB 40
Advertise
Subscribe
Account Login
Search
MEC boot camp looks inwards to find next generation of welders and fabricators
Internal boot camp transforms nonwelders into welders for Wisconsin-based fabricator
- By Rafael Guerrero
- January 31, 2023
- Article
- Arc Welding
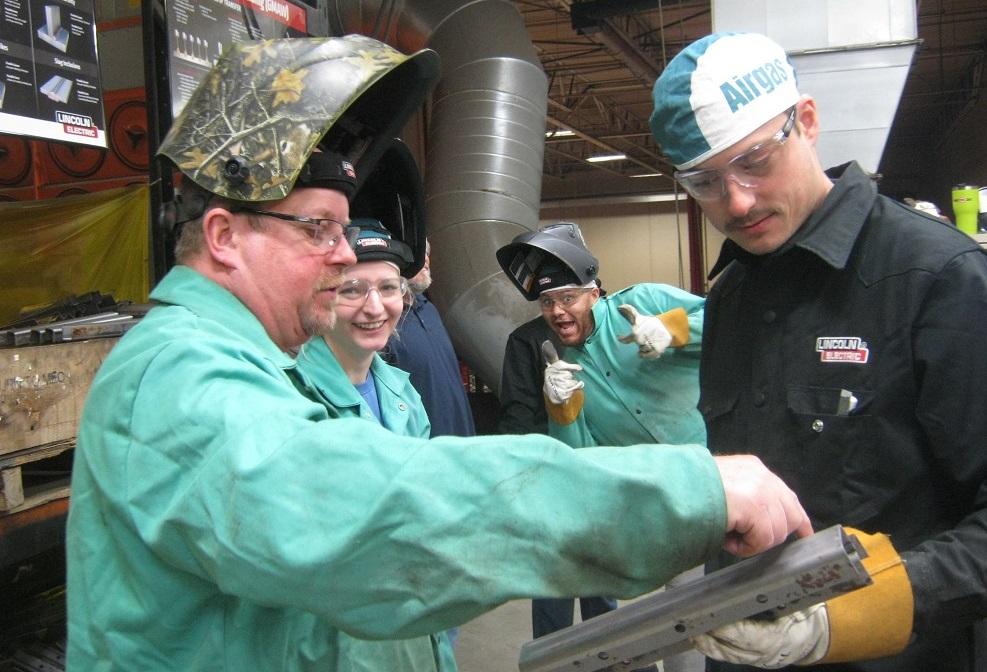
Over the years, MEC has held multiple internal weld boot camps at its Mayville, Wis., location, training participating employees to become welders. Images: Mayville Engineering Co.
It sits atop of The FABRICATOR’s 2022 FAB 40 list, employs about 2,250 in 20 locations, and was projected to earn a half-billion dollars in revenue last year. With all of that success, even Mayville Engineering Company Inc.(MEC) can’t escape the welder shortage.
Perhaps the Mayville, Wis.-based fabricator already has them on the payroll?
A few years ago, MEC began to look internally. Could it find future welders within its own walls—office assistants, forklift operators, or others who already were familiar with the MEC culture and had an interest to go under the hood and strike an arc?
And thus began the internal welding boot camp, a weeks-long program intended to teach and certify a small group of employees in welding. MEC’s Mayville location holds a couple of these boot camps each year.
“We felt we could remove the risk with these [internal] employees because we vetted them through, they already had great attendance, they had other good soft skills and other good attributes,” said Charles Francis, an MEC weld engineering supervisor.
“They can sign up and we provide the training for free during their work shift. We've been doing that now for probably four or five years to much great success,” he said. As of September 2022, about 75 employees have completed the welding boot camp and earned certification since its inception—a pass rate of at least 90%.
The WELDER spoke with Francis and Human Resources Manager Travis Moser about MEC’s internal welding boot camp, participant success stories, and lessons learned.
The WELDER: Why did MEC pursue this route to find welders?
Charles Francis: These are people that we already know have a great track record here at the company. We run these camps two or three times a year. They've been very successful, and the retainment rate has been much higher. The quality of folks has been much higher.
When you can't hire men, we learned you need to grow your own.
We find out that sometimes the less experience, the better—that less is more. You don't have to untrain bad habits because sometimes that's more difficult. We can train the skills and in the way we want to, right from the ground up with known, good employees.
TW: Are other MEC locations conducting these boot camps?
CF: There are some other [MEC] locations that have learned about this, learned about the success of it, and have reached out to us over the last year or two. But I guess they don't necessarily have the resources to do it like the team that we built here in Mayville.
That's the other thing when it comes to doing an activity like this. You can't just say “We're going to do this” and then just kind of haphazardly do it with the same resources that you run your shop with. You're never going to be successful that way. You have to have a dedicated team that writes this, administers it, and is responsible for it.
It is very important to have a dedicated team, and along with that you must have a dedicated area with machines and equipment in a suitable training environment. In other words, you're not interrupting people on the production floor, leveraging their space and their equipment. It takes a little investment, having a dedicated space, dedicated equipment, and dedicated people.
We do have a similar program for skilled painters that started a couple of years ago. When I say we, I mean a dedicated [MEC] paint team got involved and made one [an internal training program] for painters.
Travis Moser: The other thing that we're looking at is putting together a robotic press brake internal camp as well. It’s another highly technical type of position that we want to give opportunities for employees as well. So that's kind of the next iteration here.
TW: Can you explain how this internal welding boot camp works?
TM: The existing employees can apply to be a part of this program. Once they're accepted—meaning that they demonstrated good work habits already, they have good attendance and things like that—one Monday each week for eight weeks we take them out of their current role and job. They go to this welding camp and learn everything from the fundamentals of welding, the theory behind the welding, etc.
We have what we call a welding lab. There are six welding stations up there where we just give [the students] some scrap metal. They’re burning wire and basically learning how to weld.
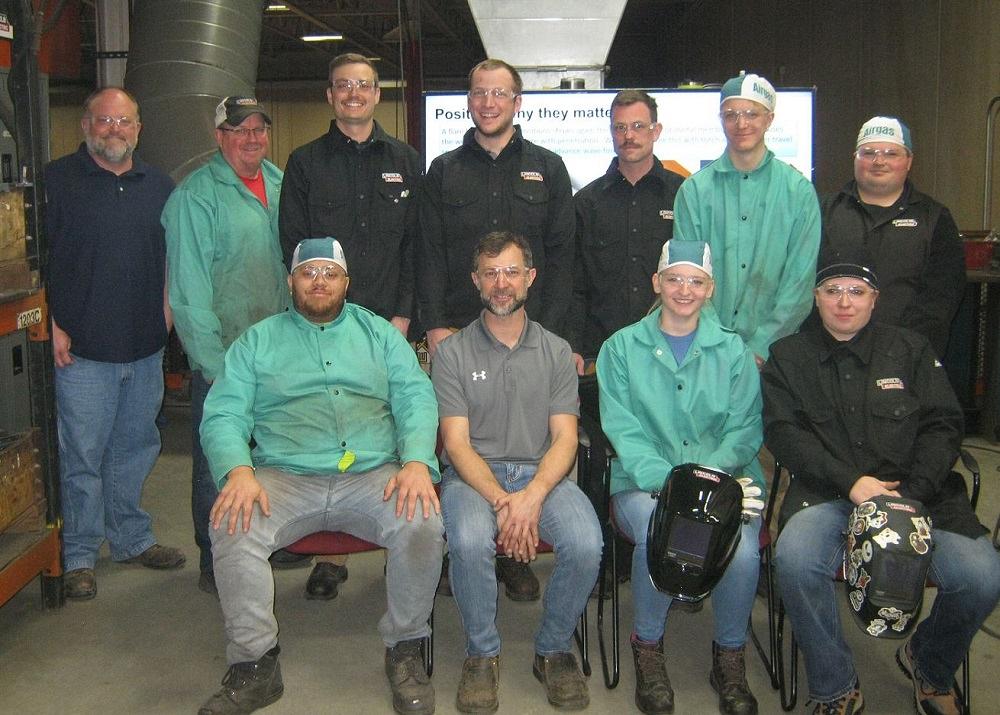
The boot camp is open to qualifying MEC employees who are nonwelders, such as forklift operators, secretaries, and entry-level workers.
After they’re done, they go right back to their departments and work in their current role, but they have access to the lab on breaks and after work for practice. And then, during the final two weeks of the camp they work in the welding department—a solid two weeks. They take a welding test at the end; once they pass that, then they become a welder and we can then transfer them right into that department.
CF: Those final two weeks, they’re welding every day. We've extended some from two weeks to four weeks or from two weeks to three weeks, because at that point we're integrating them into the production floor. I help them transition, and during that time we give them their final weld test and their weld certifications. They must have the technical skills to be able to take and pass those tests.
TW: You’ve had several employees go through boot camp successfully. Where did they come from?
TM: One of the individuals that passed the last camp was an entry-level person that we had hired as an operator—just a production operator, a helper. Within a year he went through the boot camp, and now he's a welder. That was a young kid, probably in his mid-20s.
Another example is a guy that was a forklift operator. He's probably in his early 50s, never welded before. He went through the welding camp and now he's a welder. He’s later in his career and was just surprised that we would still invest in him.
You know, it really doesn't matter what your background is so long as you have a willingness to learn and you put 100% into it. We feel confident that with the instruction that we can provide and the tools we provide, you can become a welder.
CF: Probably an even bigger success story is one of our earlier graduates, who is still one of our best robot operators. She was what I would call a middle-aged woman who worked in a secretarial job most of her life, never even saw the inside of a factory in her life. She heard of this program and signed up for it, scared to death. And I'll tell you, she was one of our best students, and she's one of our best robotic operators today.
TW: What are some of the benefits to looking internally for welders?
CF: One of the most notable ones is you don't hire in a lot of [people with] long-term bad habits that may not be a good fit for MEC and can be very hard to retrain. This gives us a chance to take on quality people and train them in the ways that we expect.
TM: I think one of the biggest things is that there's a commitment to training [internally]. If you want to become a welder, you don't have to leave MEC and go get trained and go work someplace else. You don't even have to pay tuition to learn how; we'll pay you to learn.
Differences between our internal weld camp and the schools? No. 1: The school has a finite number of class periods. You get only so much time with the instructor. You only get at the end of that semester a pass or fail, right? We can take some more additional time with people.
The other thing is when we pass somebody, we're thinking of our customers. We're not going to pass somebody just to say that we had 100% of people pass. We have our customers in mind, that everybody that we pass we feel comfortable that they are—that we are—going to send out quality products.
TW: What are the challenges to running such a program?
CF: It was maybe more challenging at first, getting the workspace, getting equipment, dedicating resources to it. The development took a lot of effort before we even started it. They always say plan for nine years and execute for one to get it right, and that's kind of how it went.
There was a lot of time before anything happened, and then once it did there was a lot of changing after the first couple of camps. We kept having lessons-learned moments, which made it better. Now we have a really good process, and it just flows.
TW: Is this type of program feasible for shops/businesses of any size?
CF: I absolutely think it can be done with a much smaller business. You would just have to do it on a much smaller scale so it's kind of proportional. The process works, it's successful. You just need to scale it up or scale it down.
TM: I think it would just come down to resources too. In a small company, I think people are accustomed to wearing a lot of different hats. A welding camp instructor might have to wear a lot of different hats.
CF: Obviously, a small company wouldn't be looking for eight to 10 folks in their area three times a year. They might be looking for one or two here and there—it could easily be much easier to accommodate that.
About the Author
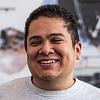
Rafael Guerrero
2135 Point Blvd.
Elgin, IL 60123
(815)-227-8242
Rafael Guerrero. was named editor of The Welder in April 2022. He spent nine years as a journalist in newspapers in the Midwest and Pacific Northwest, covering topics and communities in central Illinois, Washington, and the Chicago area.
About the Publication
Related Companies
subscribe now
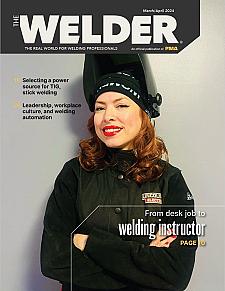
The Welder, formerly known as Practical Welding Today, is a showcase of the real people who make the products we use and work with every day. This magazine has served the welding community in North America well for more than 20 years.
start your free subscription- Stay connected from anywhere
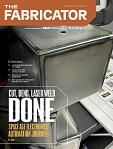
Easily access valuable industry resources now with full access to the digital edition of The Fabricator.
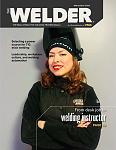
Easily access valuable industry resources now with full access to the digital edition of The Welder.
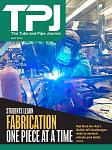
Easily access valuable industry resources now with full access to the digital edition of The Tube and Pipe Journal.
- Podcasting
- Podcast:
- The Fabricator Podcast
- Published:
- 04/16/2024
- Running Time:
- 63:29
In this episode of The Fabricator Podcast, Caleb Chamberlain, co-founder and CEO of OSH Cut, discusses his company’s...
- Industry Events
16th Annual Safety Conference
- April 30 - May 1, 2024
- Elgin,
Pipe and Tube Conference
- May 21 - 22, 2024
- Omaha, NE
World-Class Roll Forming Workshop
- June 5 - 6, 2024
- Louisville, KY
Advanced Laser Application Workshop
- June 25 - 27, 2024
- Novi, MI