Editor-in-Chief
- FMA
- The Fabricator
- FABTECH
- Canadian Metalworking
Categories
- Additive Manufacturing
- Aluminum Welding
- Arc Welding
- Assembly and Joining
- Automation and Robotics
- Bending and Forming
- Consumables
- Cutting and Weld Prep
- Electric Vehicles
- En Español
- Finishing
- Hydroforming
- Laser Cutting
- Laser Welding
- Machining
- Manufacturing Software
- Materials Handling
- Metals/Materials
- Oxyfuel Cutting
- Plasma Cutting
- Power Tools
- Punching and Other Holemaking
- Roll Forming
- Safety
- Sawing
- Shearing
- Shop Management
- Testing and Measuring
- Tube and Pipe Fabrication
- Tube and Pipe Production
- Waterjet Cutting
Industry Directory
Webcasts
Podcasts
FAB 40
Advertise
Subscribe
Account Login
Search
Doubling down on growing the manufacturing workforce in central Pennsylvania
A local high school and local businesses join forces to prepare the next generation of metal fabricators and welders
- By Dan Davis
- November 5, 2022
- Article
- Shop Management
New Oxford High School students (from left) Alaina Myers, Camden Elmo, and Beauen Garman pose with the mobile welding curtain fabrication that they built at the SkillsUSA competition in Atlanta last June. Their effort placed first in the Welding Fabrication section.
For the longest time, many communities in the U.S. took their local manufacturing companies for granted. That’s not the case in Adams County, Pa.
When a bond issue came up for the Conewago Valley School District in the late 2010s, then School Superintendent Russell Greenholt recognized an opportunity to not only improve the shop area at New Oxford High School, the district’s only high school, but also take a major step in supporting local manufacturing companies. With manufacturing representing the largest economic sector in the county, providing just over 8,600 jobs according to the Adams Economic Alliance, Greenholt felt compelled to make this commitment to vocational training work.
“At the time we had about 70% going to four- or two-year schools [after graduation], which meant the rest were going into the job market,” Greenholt said. “We felt like we needed to do something for the 30% of the kids not going to school.”
Manufacturing was at the top of Greenholt’s mind as he pursued this effort. He said he had read a survey of manufacturing executives where almost three-quarters of them agreed that local schools and community colleges were the effective way to try and resolve their problem of developing skilled workers for today’s advanced manufacturing jobs. He wanted New Oxford High School to be a proving ground for that theory.
“I went to our department chair one day, and I said, ‘We’re going to upgrade the shop. What would you think about a 25,000-sq.ft. simulation of a manufacturing plant?’ He said, ‘Are you serious?’”
Greenholt was. He made the same appeal to the school board, and they responded in the same manner. After making the case, Greenholt won the board over and was told to build up community support for what was to become an educational facility that would be the envy of many other school systems in the area.
Laying the Foundation
One of the first things that Greenholt did was reach out to the Adams County Tech Prep program based at nearby Gettysburg High School. He wanted to ensure them that the new Career and Technology Center (CTC) at New Oxford High School wasn’t going to try and replace the programs associated with the Tech Prep program, but rather be an extension.
The same thought process applied to Harrisburg Area Community College. While the school did have a welding program, it was only offered at the school’s Harrisburg campus. The campus locations near New Oxford, in Gettysburg and York, did not have the physical setup for welding education.
Greenholt made it clear to those administrators and the other nearby school districts that New Oxford wasn’t looking to duplicate the programs offered elsewhere. The high school was looking to develop specific programs tailored to the needs of local businesses. In fact, the plan was to open up spots in the welding program at New Oxford High School for other area students that wanted to learn the craft.
With the local educational community onboard, Greenholt then spent the ensuing months visiting with local companies, clubs, and business associations. He got commitments of money and in-kind contributions, such as equipment, and when a company couldn’t match that, he would walk away with a commitment for metal scrap and remnants that could be used for welding coupons.
The Conewago Valley School District in Pennsylvania opened its new Colonial Career & Technology Center in 2019 in an effort to better prepare its graduates for work in one of the many manufacturing facilities in the area.
Greenholt recalled one meeting with a local concrete contractor where he asked the owner to supply panels for the front of the Colonial Career and Technology Center (CTC) building. (New Oxford High School are known as the “colonials.”) He wanted each panel to represent a different concrete stamping to showcase what could be done with the materials.
“I wanted to highlight what the company did. I wanted to highlight an aspect of manufacturing,” Greenholt said.
The company donated the panels and installed them without charging the school district. Other companies gave 3D printers and welding power sources. The New Oxford Social Club donated computers and software, including computers that are able to deliver augmented reality programs. For instance, a student working in with the AR program can interact with a small block Chevrolet engine, disassemble it, and put it back together without the actual engine being in front of him.
The $5.2 million facility was near completion as the 2019 school year approached. Greenholt said that the school district had raised $2 million for equipment for the CTC.
“What I found when I went out to visit these companies is that there is a pride in what local people did, particularly when it came to manufacturing, and they had a willingness to partner with us,” Greenholt said.
For many companies, it just made sense. Precision Cut Industries, Hanover, Pa., was one such company.
“When the school representatives came to PCI and outlined their vision about what they were going to do, we 100% supported it,” said Shonna Sites, the company’s chief operating officer. “We saw what it was going to do for the students and the community, so we had some discussions and made a donation. The relationship just took off from there.”
The New CTC Facility
The CTC formally opened at the beginning of the 2019 school year. The addition, 14,000 sq. ft. of which was new construction, houses the school’s graphics, HVAC, hydraulics, machining, mechatronics, and welding classes.
What is immediately noticeable about the new addition is that most of the common working area can be seen through large windows on one side of the hallway that runs along the CTC. These shop classes aren’t hidden in the back of the building, known only to those that are registered for the classes.
“One of the smartest things we did was put that hallway with the windows there,” said Joe Connolly, a career counselor at New Oxford High School. “You might have students, who typically would not have interested in these types of classes, walk by and see a robot moving. All of a sudden it piques their interest.
“Now we have this nice, clean environment, and people can see all the stuff in action,” Connolly continued. “It also gives a chance for the students to display their projects that they’ve worked on for everyone to see.”
The welding area now has 20 separate welding booths, all equipped with the proper ventilation and gases being plumbed in from the outside of the building. Rick Jones, the welding and metal fabrication instructor, said that the additional welding booths give every student a space to work on their own, not having to worry about multiple students having to share one workspace and work with their peers hanging over their shoulders. (The old tech room had 10 welding stations on shared benches.) As a result, the individualized spaces promote a sense of accountability because each student has to keep them clean and treat the equipment with respect. There’s no blaming anyone else when no one else is around to blame.
The CTC investment certainly has energized interest in welding at the school. After a couple of years that were significantly affected by the COVID-19 pandemic, New Oxford students returned to a much more familiar education environment, not the remote learning scenarios that were once all too familiar, and record numbers flocked to the CTC.
Rick Jones said that they have room for 80 students each fall and spring. That’s four welding classes with 20 open spots each in the fall and the same in the spring. So, for two shielded metal arc welding classes that accommodate 20 students each, for a total of 40, the school could see as many as 80 students apply for the class, according to Jones.
At that point, Jones said that administrators take a look at how the students did from a grade perspective in their previous CTC classes, if they took a nonwelding course, and how engaged they were in the classwork. In many ways, it’s like the real world in the sense that they can only progress in the welding program if they do what’s required.
Connolly said the interest in the CTC welding program coincides with a realization, by both parents and students, that not everyone is destined to attend a four-year university. Someone needs to learn the trades because society can’t function without their talents.
“People have had enough of a problem trying to find an electrician, a plumber, or any skilled craftsman, and when they do, that person usually has gray hair or is balding,” Connolly said. “Because enough people have been affected by this in their lives, they are starting recognize the value in the trades.
“When I went to school in eastern Pennsylvania, you either went to college or got some kind of vocational education as a sort of consolation price. It was looked down upon,” he continued. “But thankfully the pendulum is starting to swing back to the point that many educators, regardless of their focus or the particular subject they teach, get the value of having vocational education.”
While the building and opening of the school’s CTC has proven to be a much-needed resource, Connolly said the 110 area businesses that have stepped up to partner with the program in various ways make the learning experience even more meaningful. Some of the companies make time for job shadowing, where students get a half-day preview of what it’s like to work in a manufacturing facility, and others open their doors to students for skills testing, where students have to pass weld tests as if they were new company employees. Some companies donate the time of their employees, who serve on the advisory committee that guides the CTC curriculum development or who make an appearance before a class to speak to them about their jobs and industry. Connolly said PCI, Conewago Enterprises Inc., and KLK Welding Inc. are examples of local companies that have taken the time to help shape the vocational education that students are receiving and might start to reap the rewards as they become candidates to hire when they graduate.
Students Making Their Mark
If the large numbers of students trying to register for the new welding classes weren’t enough proof of the impact that the school’s CTC is making, New Oxford High School got another reminder this summer. It’s first entry into the SkillsUSA competition resulted in a national championship in the Welding Fabrication category.
Alaina Myers, now a senior, and Camden Elmo and Beauen Garman, who graduated from New Oxford earlier this summer, were named first place winners after constructing a mobile welding curtain. The team had to take a knowledge test, participate in an interview with subject matter experts, and then fabricate the welding curtain contraption from a set of prints. The entire process lasted more than six hours.
A win in the district contest, where the trio fabricated a pizza oven, and another victory at the state level, where the group made a metal tip hopper, preceded the national championship. More than 6,500 high school and college students competed in 108 different trade, technical, and leadership competitions, including three welding categories: welding, welding fabrication, and welding sculpture.
“That’s been the biggest surprise for me with this whole thing is that our SkillsUSA team killed it at the regional, state, and national levels. To me, that’s better than a state championship in a sport because they competed and won on a national level,” Connolly said.
“But it’s not just about showing up and winning,” he added. “It’s about all the steps the led up to that, including sending out letters of support to local businesses saying, ‘Hey, will you help to sponsor us?’ and then fielding those phone calls. They as a group did all of that. So now they’ve got some business acumen that they didn’t have prior to this. They’ve got the hard skills and soft skills that they need for the future.”
Myers said she really had no idea what welding was before taking welding classes in the CTC. She ended up in a welding class with her best friend her freshman year. She stuck with the unfamiliar, but exciting, curriculum and wound up loving it. Since then, she’s taken every single welding class, including a couple of independent study classes, an electronics course, and a basic machining course.
“Welding just puts me in a place where I can just forget about everything else. Everything just goes away, and it’s just me and the puddle,” Myers said. “That’s truly what I love about it; it just really puts me in the spot where I feel really happy.”
While her friends were working random shifts at nearby retail stores this past summer, Myers woke up at 5 a.m. each morning and went to work at PCI, where she got to work on a variety of fabrications and practice the different welding processes. The experience has only cemented her desire to follow this passion. She’s planning on attending the Pennsylvania College of Technology in Williamsport, Pa., to further her manufacturing education studies.
Of course, Myers is only one student, but there are others. Connolly said that students in the CTC classes are getting multiple job offers before they even graduate. Some actually sign commitment letters, much like their classmates who commit to play sports for a college, their junior year.
Meanwhile, Greenholt has retired and spends some of this time woodworking, enjoying a new lathe he purchased after leaving his superintendent role. He’s introduced his 10-year-old granddaughter to the tool and has found out that she loves to make things with her hands. The most recent project was a miniature car.
“I told her as you get older, no one can ever take that skill away from you,” Greenholt said. “That’s going to be a skill you’re going to have the rest of your life, and if you keep doing it, you can get better at it.”
Learning lifetime lessons is what education is all about. The folks in Adams County recognize that those lessons aren’t limited college-track classes.
About the Author
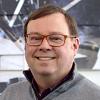
Dan Davis
2135 Point Blvd.
Elgin, IL 60123
815-227-8281
Dan Davis is editor-in-chief of The Fabricator, the industry's most widely circulated metal fabricating magazine, and its sister publications, The Tube & Pipe Journal and The Welder. He has been with the publications since April 2002.
subscribe now
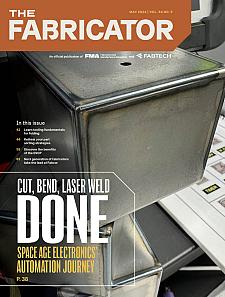
The Fabricator is North America's leading magazine for the metal forming and fabricating industry. The magazine delivers the news, technical articles, and case histories that enable fabricators to do their jobs more efficiently. The Fabricator has served the industry since 1970.
start your free subscription- Stay connected from anywhere
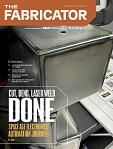
Easily access valuable industry resources now with full access to the digital edition of The Fabricator.
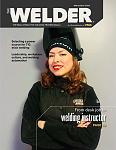
Easily access valuable industry resources now with full access to the digital edition of The Welder.
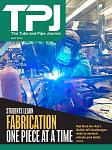
Easily access valuable industry resources now with full access to the digital edition of The Tube and Pipe Journal.
- Podcasting
- Podcast:
- The Fabricator Podcast
- Published:
- 04/30/2024
- Running Time:
- 53:00
Seth Feldman of Iowa-based Wertzbaugher Services joins The Fabricator Podcast to offer his take as a Gen Zer...
- Industry Events
16th Annual Safety Conference
- April 30 - May 1, 2024
- Elgin,
Pipe and Tube Conference
- May 21 - 22, 2024
- Omaha, NE
World-Class Roll Forming Workshop
- June 5 - 6, 2024
- Louisville, KY
Advanced Laser Application Workshop
- June 25 - 27, 2024
- Novi, MI