Senior Product Manager Welding
- FMA
- The Fabricator
- FABTECH
- Canadian Metalworking
Categories
- Additive Manufacturing
- Aluminum Welding
- Arc Welding
- Assembly and Joining
- Automation and Robotics
- Bending and Forming
- Consumables
- Cutting and Weld Prep
- Electric Vehicles
- En Español
- Finishing
- Hydroforming
- Laser Cutting
- Laser Welding
- Machining
- Manufacturing Software
- Materials Handling
- Metals/Materials
- Oxyfuel Cutting
- Plasma Cutting
- Power Tools
- Punching and Other Holemaking
- Roll Forming
- Safety
- Sawing
- Shearing
- Shop Management
- Testing and Measuring
- Tube and Pipe Fabrication
- Tube and Pipe Production
- Waterjet Cutting
Industry Directory
Webcasts
Podcasts
FAB 40
Advertise
Subscribe
Account Login
Search
Cobot safety factors in welding
Although designed to work with humans, collaborative robots still have the potential to cause injury
- By Josh Leath
- Updated August 10, 2023
- September 26, 2022
- Article
- Arc Welding
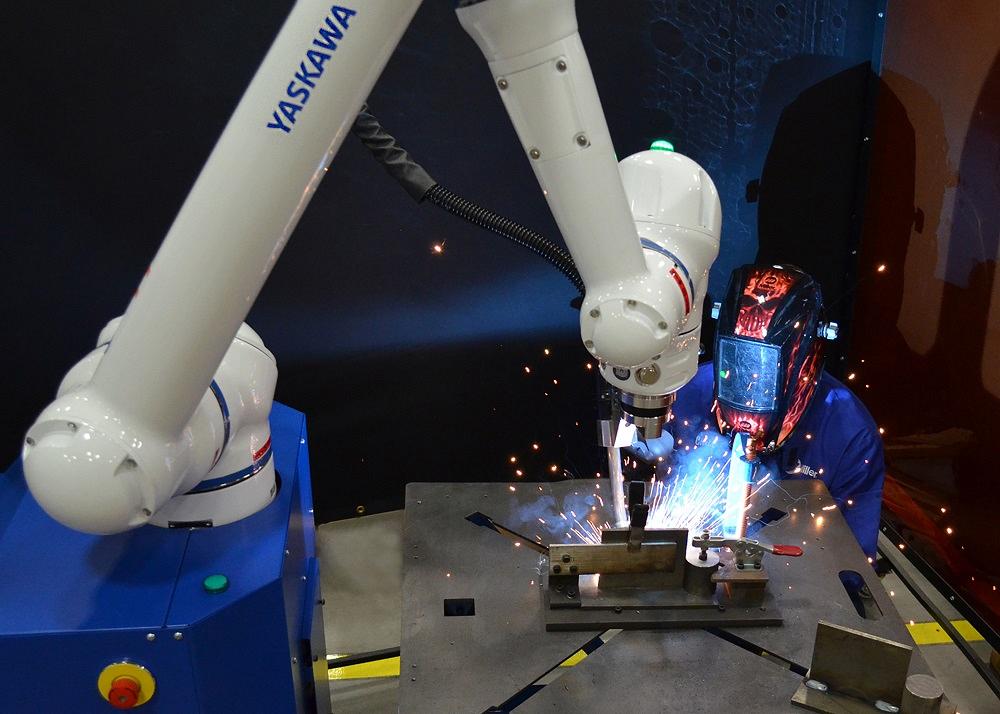
Cobots look untimidating, but they need to be treated like any other aspect of fabricating equipment. For an application to truly qualify as collaborative and deemed safe, the entire robotic system and application must be addressed. This includes the robot, workpiece, robot work area, and even the end-of-arm tooling.
Capable, yet affordable, user-friendly technology in the form of collaborative robots continues to spark confidence among companies interested in implementing robotic automation.
These highly flexible cobots are especially appealing, as they facilitate safe human/robot interaction, while also being highly productive with a space-saving footprint. That’s why cobots are the fastest growing segment of the robotics industry, according to a 2022 report from New Heights Research, and there is still room for expansion.
Once relegated to a very basic cobot with semiautomatic weld equipment, today’s welding cobots offer quite the dichotomy. They have feature-rich power supplies and intuitive pendant applications, which allow them to shift between collaborative speed in power-and-force limiting (PFL) mode (to reduce or avoid injury in case of contact with a person) or full speed in industrial mode (based on risk assessment and requirements).
Whether supplementing manual welding or being rolled-up to large, heavy workpieces, extremely versatile cobots are making highly relevant applications come to life, especially for high-mix, low-volume production environments. This has brought the issue of collaborative robot safety to the forefront, and it is well worth addressing, especially for those branching into robotics.
Cobot Safety 101
One of the greatest benefits cobots have to offer is they provide humans the ability to work with or in close proximity to robots. However, using a collaborative robot in name and design is not enough to make an application safe. For an application to truly qualify as collaborative and deemed safe, the entire robotic system and application must be addressed. This includes the robot, workpiece, robot work area, and even the end-of-arm tooling. If any of these critical areas fail to meet specified safety standards during a risk assessment, then the application cannot be approved without proper risk mitigation.
When it comes to optimizing robot usage, safety should not be overlooked. To achieve peak performance and the best robot work area possible, manufacturers should consider the following factors.
Overall Environment. While robots are extremely effective at tackling risk-intensive tasks, they also can pose their own set of concerns that should be addressed before operation. Part of this includes being sure the general workspace is robot friendly.
Similar to a typical welding environment, a cell with a welding cobot should be clear of things such as explosives or falling hazards. If tripping on robot cables or slipping on weld spatter is a concern, be sure to implement the proper peripherals needed to mitigate those risks.
Robot Stability. As with any robot, it is imperative that a cobot base or cart is properly secured per the supplier’s standards. Doing this should confirm the proper center of gravity so that the robot cannot slip. Where carts are concerned, wheels should be locked tightly to prevent any movement (or oscillation) as the robot is trying to weave.
Robot Movement. Extremely important to the success of an application is the robot’s ability to move freely from point to point, while adhering to the utmost safety. A cable management device for torch cable protection is suggested to alleviate cable interference during programming and to prevent false PFL stops on the robot.
Either an on-arm device or a cable balancer for overhead cable management is ideal. The latter can help expand the robot work area as needed.
Cobot Safety Fixturing. To achieve the best part quality in the safest way possible—especially for high-mix, low-volume production runs—having the proper weld table or fixture is key and can often be achieved by means of an existing weld table and clamps. For safe, cost-effective ideas for producing a stable fixture that is well-suited for collaborative welding, companies can turn to fixturing software, which helps them rethink what is possible.
Guarding Requirements. Keep in mind, collaborative robots currently do not offer external axes compatibility, so applications requiring the use of specific positioners for coordinated motion or a robot track need to be mitigated by fencing, light curtains, or other means. While items such as fencing may result in additional upfront cost, sometimes 20% of a workcell’s overall cost, it is often the simplest and best way to mitigate common risks.
If the use of safety fencing is necessary because of cycle time requirements or part-turning specifications, a positioner may be in order. If so, positioner size can make a difference. For example, a Ferris wheel positioner with a two-station design is more space efficient than an H-frame turn table, optimizing floor space utilization. The proper positioner also can go a long way to meeting strategic company goals for the number of welded inches per minute.
Fume Extraction. Whether they are close to the process or not, protecting human workers from harmful fumes throughout the facility is of the utmost importance and often required by local safety regulations. Widely used for manual weld processes, ambient air extraction systems and hood fume collection systems can still be used for a variety of robotic welding applications today. However, each demands a unique set of criteria that may hinder certain collaborative processes.
For example, ambient air filtration systems seek to filter all of the air within a facility. For large facilities separated by columns, walls, or even large machinery, this can present a huge risk, as these objects can trap air, causing dead zones or pockets of poorly filtered air. While highly effective for the right application, hood fume collection systems also present risks under certain circumstances. For example, if a cobot is being rolled up to a large workpiece that requires placement via an overhead gantry, a hood is typically too small to accommodate the filtration process needed. Add in other factors like the upfront capital required or monthly energy consumption costs, and these systems are not always ideal.
Enter the concept of source capture robotic fume extraction. To provide customers with an easier-to-implement and more economical solution, innovative weld equipment suppliers now offer fume capture at the source. Most beneficial for these systems is their ability to keep up with the higher duty cycles and throughput requirements of robotic welding. These options work at the torch level and feature filtration packs that can “ride along” with collaborative robots. The plug-and-play ability of source capture devices is especially helpful for welding large parts for heavy fabrication, as well as on-demand supplemental welding.
Arc Flash. As in traditional welding environments, manual welders should mitigate arc flash and UV exposure via personal protective equipment. Safety arc flash curtains or other barriers also should be put in place, when needed, to protect bystanders.
Additional Cobot Safety. Depending on application requirements, additional safety measures may help. An interfaced stack light mounted on the robot cart or nearby can assist to visually confirm the status of a robot and provide sufficient warning to those close to the work area that the robot is about to weld. This allows workers and bystanders plenty of time to look away from the arc or get out of the way. Tone-emitting or “talking” versions that give audible commands also are available.
An extra mode of collaboration to increase speed and mitigate risk, an area scanner also may be used to make sure no one is immediately around the robot before or during welds. Typically involving one to two area safety scanner units mounted below the robot, this allows the cobot to move at full industrial speeds until the protected area is broken. Additionally, area scanners are more resistant to weld spatter and smoke.
E-stop Device. Every robot system must have a fail-safe way to stop for any level of emergency. Often triggered by an external emergency stop (e-stop) push button or an output from the safety controller, knowing how to activate this, if needed, is a must.
Proper Cobot Safety Training. No matter the collaborative system of choice, proper employee training should be offered. Yes, a cobot offers a lot of ease-of-use abilities, but it is still a machine that is best (and most safely) used with some know-how. From basic programming to robotic welding and maintenance, hands-on training courses can help maximize robotic equipment performance for both beginners and experienced users.
Novice robotic welding professionals can choose from different programming options for cobot applications:
- Features such as lead-to-teach or I/O jogging from a momentary command device may provide a faster more intuitive way to change things like torch angle and tooling coordinates.
- Easy-to-use pendant applications, like the Universal Weldcom Interface, also can help fill in the knowledge gap, enabling full utilization of advanced capabilities on any brand of digital welding power supply.
Practice Cobot Safety When Welding
Whether a small to medium-sized shop is working around space constraints or a Tier 1 company is looking to measure production value per square inch, cobots can help. Conducting a thorough site audit with an experienced robot supplier or integrator can answer a multitude of questions and address issues concerning safety standard compliance.
About the Author
Josh Leath
100 Automation Way
Miamisburg, OH 45342
(937)-847-6200
Related Companies
subscribe now
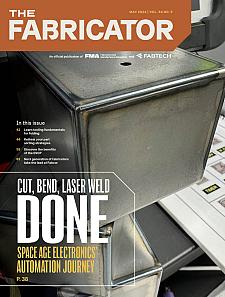
The Fabricator is North America's leading magazine for the metal forming and fabricating industry. The magazine delivers the news, technical articles, and case histories that enable fabricators to do their jobs more efficiently. The Fabricator has served the industry since 1970.
start your free subscription- Stay connected from anywhere
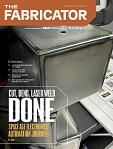
Easily access valuable industry resources now with full access to the digital edition of The Fabricator.
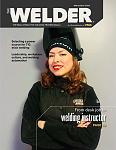
Easily access valuable industry resources now with full access to the digital edition of The Welder.
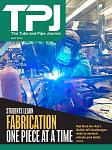
Easily access valuable industry resources now with full access to the digital edition of The Tube and Pipe Journal.
- Podcasting
- Podcast:
- The Fabricator Podcast
- Published:
- 04/16/2024
- Running Time:
- 63:29
In this episode of The Fabricator Podcast, Caleb Chamberlain, co-founder and CEO of OSH Cut, discusses his company’s...
- Trending Articles
Tips for creating sheet metal tubes with perforations
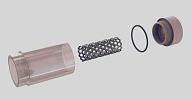
Are two heads better than one in fiber laser cutting?
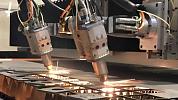
Supporting the metal fabricating industry through FMA
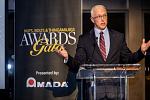
JM Steel triples capacity for solar energy projects at Pennsylvania facility
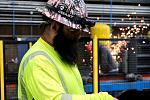
Omco Solar opens second Alabama manufacturing facility
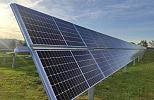
- Industry Events
16th Annual Safety Conference
- April 30 - May 1, 2024
- Elgin,
Pipe and Tube Conference
- May 21 - 22, 2024
- Omaha, NE
World-Class Roll Forming Workshop
- June 5 - 6, 2024
- Louisville, KY
Advanced Laser Application Workshop
- June 25 - 27, 2024
- Novi, MI