Senior Editor
- FMA
- The Fabricator
- FABTECH
- Canadian Metalworking
Categories
- Additive Manufacturing
- Aluminum Welding
- Arc Welding
- Assembly and Joining
- Automation and Robotics
- Bending and Forming
- Consumables
- Cutting and Weld Prep
- Electric Vehicles
- En Español
- Finishing
- Hydroforming
- Laser Cutting
- Laser Welding
- Machining
- Manufacturing Software
- Materials Handling
- Metals/Materials
- Oxyfuel Cutting
- Plasma Cutting
- Power Tools
- Punching and Other Holemaking
- Roll Forming
- Safety
- Sawing
- Shearing
- Shop Management
- Testing and Measuring
- Tube and Pipe Fabrication
- Tube and Pipe Production
- Waterjet Cutting
Industry Directory
Webcasts
Podcasts
FAB 40
Advertise
Subscribe
Account Login
Search
Soldando tubo de manera autónoma
Cómo la inteligencia artificial ayuda a hacer una realidad la soldadura autónoma de tubo
- By Tim Heston
- July 18, 2022
- Article
- Tube and Pipe Fabrication
“La soldadura de penetración completa de tubo de un solo lado es algo que he evitado automatizar durante toda mi carrera, la cual inició a principios de la década de 1980, debido a que el requerimiento de control adaptivo es demasiado alto”.
Eso dijo Dan Allford, presidente de ARC Specialties, una firma de desarrollo de procesos y sistemas automatizados con sede en Houston. “Es por eso que a todo aquél que ha acudido a nosotros con una unión de un solo lado de penetración completa, le insisto en una preparación en J. Cuando se hace una preparación en J, se hace una abertura de raíz cero, y cero es algo repetible. Sin embargo, en cuanto se pasa a una preparación en V, se tiene una abertura de raíz variable, y automatizar esa aplicación se vuelve realmente difícil”.
Esto empezó a cambiar hace tres años, cuando Allford vio tres tecnologías concretándose. La primera fue el cobot, el cual permitió que la automatización de soldadura de tubo funcionara cerca de las personas. La segunda fue un escaneo láser 2D asequible, el cual podía escanear y mapear una unión. Y el tercero fue la soldadura por arco de metal protegido por gas con transferencia de corto circuito por forma de onda avanzada (GMAW).
Cuando se trata de la soldadura de tubo, la transferencia de corto circuito por forma de onda crea un charco “suave” que en años recientes ha permitido a los soldadores de tubo unir espacios altamente variables. “Un humano puede adaptarse en un instante al espacio variante observando el ancho y cambiando su velocidad de viaje y su ancho de oscilación”, dijo Allford. “Eso está perfecto, las máquinas no pueden hacer eso hasta que tienen la capacidad de detectar el ancho del espacio de raíz y reaccionar a ello. Es ahí donde entró el escaneo láser así como la inteligencia artificial, lo que significa que el sistema aprende sobre la marcha. En este caso, estamos usando el CPU para determinar cuáles son los mejores parámetros para una dimensión de unión dada”.
La GMAW de corto circuito convencional no es un proceso de elección para la raíz de una soldadura de tubo. Eso se debe principalmente a la manera en que se comporta el corto circuito: es errático, ocurre a intervalos inconsistentes y a niveles variantes de intensidad. Maniobrar la pistola de soldadura en la raíz es un poco como dirigir un bote por aguas agitadas, tratando de minimizar salpicaduras de metal fundido hacia la pared lateral de la unión que podrían crear un solape en frío. En resumen, el proceso trabaja contra el soldador, quien, muy probablemente preferiría estar usando una antorcha por arco de tungsteno protegido con gas. Por otro lado, la GMAW de corto circuito por forma de onda controla el corto circuito y reduce la corriente para controlar la transferencia de metal. Eso le da al soldador mucho mejor control sobre el charco de soldadura.
Por otro lado, el proceso también tiene características de muy baja penetración y baja dilución. “Es por eso que es uno de los poco procesos no precalificado para soldadura de tubo de nivel código por la Sociedad Americana de Soldadura (AWS, por sus siglas inglés), dijo Allford. Entonces, nuestra estrategia es usarlo sólo cuando lo necesitamos”. Eso incluye esa pasada crítica de raíz.
Actualmente, la compañía ha implementado un sistema—con Soldador de Tubo de Inteligencia Artificial, AIPW, por sus siglas en inglés—que suelda tubos en 1G, con puntos colocados aleatoriamente alrededor de la circunferencia. Éste consta de un brazo de cobot de Universal Robots y una fuente de poder de soldadura de deposición regulada de metal (RMD, por sus siglas en inglés) Miller. Puede manejar espacios entre 1/16 y 3/16 de pulgada, y puede manejar una variación alta-baja (esa ligera discordancia entre las dos partes planas de la ranura en V) hasta 3/32 pulgadas. Hasta ahora, el sistema se ha usado en diámetros de tubo de hasta 24 pulgadas y en paredes entre 0.125 y 0.5 pulgadas de espesor.
“Hasta ahora hemos estado soldando tubo de acero al carbón A106 estándar”, dijo Allford, “pero el concepto debe de aplicarse a todo tipo de materiales”.
En la mayoría de las configuraciones los puntos han sido suavizados, lo que significa que hay una transición suave entre el punto y la pared lateral, pero éstos no tienen que ser suavizados. Si un punto es grande, el sistema puede empezar con corto circuito por forma de onda avanzada, cambiar rápidamente a GMAW por rociado pulsado sobre el punto grande (lo que ofrece una mayor penetración y llenado), luego regresar una vez que la pistola de soldadura pasa el punto y está soldando la raíz.
Una vez que el escáner láser mapea toda la junta, el CPU calcula cómo manejar la variación. Éste empieza en el punto cerca de la abertura de raíz más pequeña. Debido a que hay un espacio más pequeño en el punto de inicio (el cual en la soldadura de tubo también es el punto final), la pistola puede viajar con menos oscilación y a una velocidad más alta. Esto significa que al final del ciclo, cuando el charco es grande y fluido, la soldadura tiene menos oportunidad de perforación por fusión.
Un láser escanea una unión de soldadura de tubo para detectar cambios en la abertura de raíz y otras variaciones geométricas.
La soldadura inicia en la raíz con un sutil zig-zag con una forma sinusoidal (no hay mucho espacio para un zig-zag pronunciado en la raíz). Sin embargo, iniciando en la pasada caliente, el sistema puede empezar una acción de tejido a un ángulo, rellenando la soldadura en los dedos de soldadura de la pasada previa. Esto en efecto emula la acción de un soldador manual de tubo “boquillando” para asegurar una buena penetración y características de humectación de la pared lateral, lo que crea una transición suave entre la soldadura y el metal de base. Después de la raíz, el sistema cambia luego a GMAW por rociado pulsado para las pasadas caliente y de relleno.
En el fondo todo es interpolación, el acto de relacionar los datos aportados por el escáner láser con los atributos físicos de la unión de soldadura. Esto incluye la abertura de raíz y el tamaño total de la ranura en V así como la ubicación, el tamaño y la naturaleza (suavizada o no) del punto.
“Tuvimos que correlacionar todo esto”, dijo Jim Walker, tecnólogo de soldadura de ARC Specialties. “Pienso que probablemente fue la parte más difícil de todo el proyecto”.
Específicamente, el equipo necesitó desarrollar un conjunto de parámetros de soldadura como un punto de referencia para correlacionar lo que funciona para una abertura de raíz específica. Dicha interpolación podría verse como puntos de navegación a lo largo de un mapa de una unión de tubo. Conforme el escáner láser captura el mapa de la unión, el sistema basado en IA sabe que ciertas características de la unión—esta abertura de raíz, ese volumen de ranura, estos tipos de puntos de soldadura—se correlacionan con una combinación específica de parámetros de soldadura. Los parámetros más críticos son la amplitud de la oscilación (ancho de zig-zag) y la forma (sinusoidal contra boquillado).
“Tenemos diferentes programas de soldadura para cada abertura de raíz”, explicó Walker. “Actualmente, los únicos parámetros que cambian son el ancho de la oscilación, para que el robot pueda continuar uniendo el espacio correctamente, y la velocidad de viaje, para que la deposición volumétrica del metal de aportación permanezca constante. Sin embargo, lo hemos diseñado para que usted pueda cambiar la alimentación del alambre, el voltaje y el control del arco, en caso de ser necesario. Aunque hasta la fecha no hemos tenido necesidad de eso”.
Todo esto prepara el terreno para la soldadura autónoma. Un operador sujeta un tubo punteado en una sujeción rotatoria. El láser escanea la unión, el CPU calcula las variaciones y las adaptaciones del proceso requeridas, después de lo cual el cobot empieza a soldar sin ser atendido, sin intervención del operador desde la raíz hasta la tapa.
Incursionando en 5G
La configuración de cobot funciona en 1G, la posición más extendida en soldadura de tubo, en la cual el tubo gira en un posicionador y la pistola de soldadura permanece fija. Sin embargo, ¿qué pasa en situaciones donde el tubo es horizontal pero no puede girar? ¿Qué tal si se suelda en 5G?
En meses recientes ARC Specialties ha estado trabajando con el sistema mecanizado de Bug-O Systems para desarrollar soldadura de tubo en 5G totalmente autónoma. Espera empezar a comercializar el sistema el próximo año.
Las configuraciones actuales involucran dos sistemas mecanizados, cada uno de los cuales suelda la mitad de la circunferencia de un tubo de diámetro grande. (De acuerdo con Walker, podría diseñarse un sistema similar para un tubo de diámetro menor con un solo sistema mecanizado viajando por toda la circunferencia del tubo.) Como con el sistema 1G, un escáner láser mapea la geometría de la unión. Ocurre un concepto similar de interpolación, pero requiere un paso adicional. El sistema no sólo debe adaptarse a cambios en el ancho del espacio y en la geometría de la unión, sino que también debe considerar la relación en constante cambio entre la pistola de soldadura y la unión de soldadura.
“Ahora básicamente estamos soldando en todas las posiciones en cada revolución”, dijo Allford. “Estamos optimizando los parámetros no sólo en cuanto a la unión sino también en cuanto a la gravedad”.
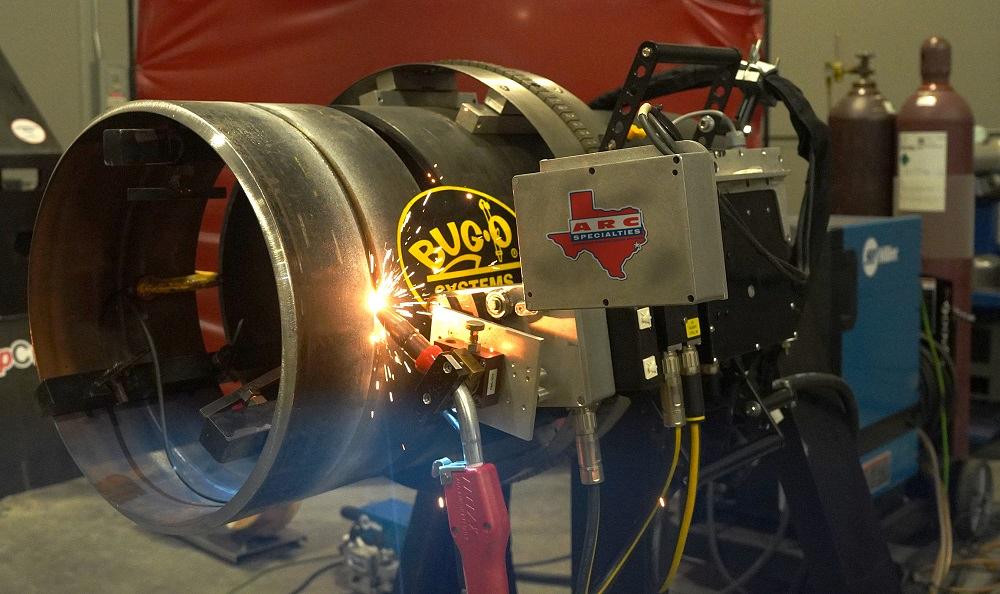
Una configuración en el laboratorio de soldadura de ARC Specialties involucra una pistola montada en una máquina de soldadura mecanizada Bug-O. Durante las pasadas caliente y de relleno, la pistola puede oscilar a lo largo de un eje de pasos, lo cual le permite moverse de una manera que apunta la pistola en el dedo de la pasada de soldadura previa, produciendo el mismo resultado que un soldador manual boquillando.
El sistema suelda de arriba hacia abajo y mantiene un ligero ángulo de la pistola hacia atrás. Conforme el sistema mecanizado llega a la posición de las 3 en punto, el viaje se acelera ligeramente para considerar la gravedad. La antorcha en el sistema mecanizado puede moverse en un zig-zag estándar y además, como su contraparte en 1G, en un modo de “boquillado”. Hace esto ajustando un nuevo eje de movimiento en el sistema mecanizado—lo que Allford llamó el “eje de apriete”. En esencia, el eje permite a la pistola cambiar el paso de forma que, durante las pasadas caliente y de copa, puede oscilar y dirigirse hacia los dedos de las pasadas de soldadura previas.
“Estamos trabajando con tres diferentes conjuntos de parámetros de soldadura para la misma abertura de raíz”, dijo Walker, y explicó que un conjunto de parámetros funciona entre la posición de las 12 y las 2 en punto; otro conjunto entre las 2 y las 4 en punto; y otro más entre las 4 y las 6 en punto.
Las sujeciones podrían ser diferentes en 5G. En 1G un tubo punteado gira en un posicionador. En 5G el tubo podría puntearse, sujetarse y alinearse internamente, o tener tanto punteado como sujeción interna. Sin embargo, se aplicaría el concepto básico detrás de la lógica de interpolación. Si la abertura de raíz y la geometría general de la unión es ésta en esa posición en la circunferencia del tubo, entonces aplicarían estos parámetros de soldadura. Mientras más soldadura haga el sistema, más aprende la máquina, y mejores interpolaciones puede hacer.
La evolución de la automatización de la soldadura de tubo
Dichas interpolaciones avanzan efectivamente la automatización unos pasos más cerca de comportarse como lo haría un soldador de tubo experimentado. Si la abertura de raíz se hace más angosta, entonces necesito cambiar mi zig-zag y la velocidad de viaje de soldadura en cierta cantidad.
Eso esencialmente crea la base para una soldadura autónoma, el tipo de proceso que los operadores no necesitan observar. Los operadores pueden configurar el sistema, luego ir a un trabajo que, por decir, requiere soldadura de tubo en 6G (tubo incluido a 45 grados) u otra aplicación cuyo costo de automatización sería prohibitivo.
Con la escasez tan aguda de mano de obra, pocas personas arguyen que la automatización causa pérdida de empleos. El mundo necesita más soldadores de tubo. El reclutamiento es una manera de llegar a ese punto, pero también lo es la automatización, especialmente cuando ésta aumenta el valor de cada soldador de tubo. Los soldadores de tubo que están iniciando su carrera ahora, es probable que se retiren de una industria muy diferente, una que mezcla destreza manual con tecnologías de soldadura autónoma—las que pueden hacer cordones estrechos, pueden tejer e incluso pueden (al menos a su manera) boquillar.
About the Author
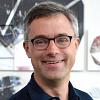
Tim Heston
2135 Point Blvd
Elgin, IL 60123
815-381-1314
Tim Heston, The Fabricator's senior editor, has covered the metal fabrication industry since 1998, starting his career at the American Welding Society's Welding Journal. Since then he has covered the full range of metal fabrication processes, from stamping, bending, and cutting to grinding and polishing. He joined The Fabricator's staff in October 2007.
About the Publication
Compañías Relacionadas
subscribe now
FMA Communications ha introducido al mercado la edición en Español de la revista The Fabricator. Esta versión consiste del mismo tipo de artículos técnicos y sección de lanzamientos de nuevos productos que actualmente presentan el personal de primera categoría de Fabricator en Inglés.
start your free subscription- Podcasting
- Podcast:
- The Fabricator Podcast
- Published:
- 04/30/2024
- Running Time:
- 53:00
Seth Feldman of Iowa-based Wertzbaugher Services joins The Fabricator Podcast to offer his take as a Gen Zer...
- Trending Articles
Los operadores de prensa dobladora inexpertos hacen indispensable el repensar la seguridad
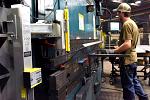
Prescripción para la reducción del desperdicio: arreglo esbelto de las instalaciones
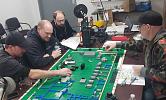
Anidado para la estabilidad del corte láser
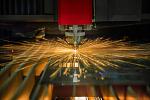
La máquina procesadora de placas crea biseles complejos en un solo corte
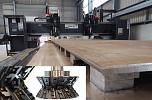
El software guía a los soldadores a través de instrucciones de trabajo
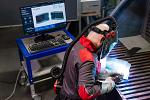
- Industry Events
Pipe and Tube Conference
- May 21 - 22, 2024
- Omaha, NE
World-Class Roll Forming Workshop
- June 5 - 6, 2024
- Louisville, KY
Advanced Laser Application Workshop
- June 25 - 27, 2024
- Novi, MI
Precision Press Brake Certificate Course
- July 31 - August 1, 2024
- Elgin,