President
- FMA
- The Fabricator
- FABTECH
- Canadian Metalworking
Categories
- Additive Manufacturing
- Aluminum Welding
- Arc Welding
- Assembly and Joining
- Automation and Robotics
- Bending and Forming
- Consumables
- Cutting and Weld Prep
- Electric Vehicles
- En Español
- Finishing
- Hydroforming
- Laser Cutting
- Laser Welding
- Machining
- Manufacturing Software
- Materials Handling
- Metals/Materials
- Oxyfuel Cutting
- Plasma Cutting
- Power Tools
- Punching and Other Holemaking
- Roll Forming
- Safety
- Sawing
- Shearing
- Shop Management
- Testing and Measuring
- Tube and Pipe Fabrication
- Tube and Pipe Production
- Waterjet Cutting
Industry Directory
Webcasts
Podcasts
FAB 40
Advertise
Subscribe
Account Login
Search
Growing a knowledge-based workforce in the manufacturing industry
The days of ‘Do as you’re told!’ have been replaced with ‘What do you think?’
- By Bill Frahm
- August 15, 2022
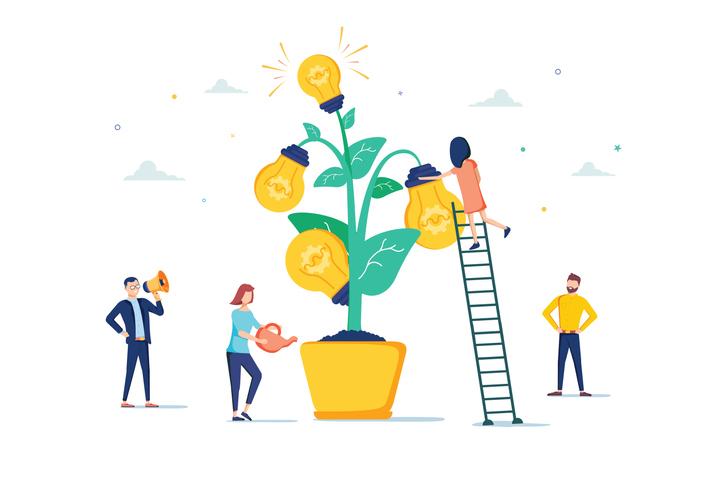
Preparing knowledge workers for the modern manufacturing workforce is going to take the involvement of both private companies and educational institutions. Mykyta Dolmatov/iStock/Getty Images Plus
I believe that many of today’s challenges developing and finding skilled tradespeople can be traced back to the introduction of scientific management, also known as Taylorism. While Taylorism did bring efficiency to manufacturing, it turned the perception of trades toward task execution rather than skilled knowledge workers.
One of Frederic Taylor’s goals in scientific management was to make employees “do what they are told to do promptly and without asking questions or making any suggestions.” This command-and-control approach to management is unacceptable to many of today’s bright, educated young people. These are the same people we need on our plant floors.
Scientific management is celebrated for introducing efficiency to modern manufacturing. To a large degree, the celebration is well-deserved. One of the biggest issues with scientific management is that it tried to separate the knowledge of trade activities from the skills. One of its goals was to discourage trade associations and unionism. The result was a discouraged and disengaged workforce.
In today’s manufacturing environments, our best management alternative is to share both knowledge and skill. Today’s dynamic and increasingly knowledge-based manufacturing business demands understanding and engagement by each individual on the shop floor.
Knowing many manufacturing employees, I hear endless stories about naive managers ordering the wrong repairs because they failed to ask the opinions of line employees. I had a brother-in-law, a millwright, who talked about the amount of overtime pay he made from this. He and his partners simply executed orders until the manager finally either asked for an opinion or stumbled on the right solution.
This type of management is obviously costly and unacceptable. These issues will continue until employers actively acknowledge and encourage the knowledge contributions of tradespeople. Operators, mechanics, tool- and diemakers, and electricians are your front line in production. They probably know their equipment much more intimately than anyone else on the floor. Their expertise should not be taken for granted.
I hear frequently that it’s difficult to find candidates who are both knowledgeable and motivated. We count on colleges and trade schools to graduate work-ready candidates. Responsibility and commitment must be taught and reinforced at these institutions if they are to contribute to building a productive workforce.
Today, manufacturing work is driven by data and information. The materials and technologies of sheet metal forming changed dramatically over the past 20-plus years. Old rules of thumb are becoming obsolete in light of modern materials and technologies. We need employees who recognize that the industry has changed and can challenge conventions and propose better alternatives.
Developing a workforce capable of meeting the demands of modern forming requires commitment from colleges, trade schools, and employers. It’s time the industry recognizes its challenges and supports efforts to develop a workforce able to meet those challenges. These efforts must also cross the entire supply chain if we are to be successful.
My suggestions for combatting our challenges and developing talent include having manufacturing companies educating prospective employees in the following areas:
- Communication and writing skills - Communication is the single most important skill for almost all careers. Employees must be able to articulate their ideas and experiences clearly. Effective communication demands the proper use of words that are easily understood by colleagues.
- Material properties and behavior - The diversity of available materials requires that employees understand the mechanical behaviors of the metals they form.
- Fundamentals of statistics - Not everyone needs to do the calculus. But most of us need to understand distributions, correlations, graphs, and other elements of statistics to make informed decisions.
- Shop math - Employees should know when and how to apply shop math to solve problems. Shop math is an applied math that employs the basics of algebra, geometry, trigonometry, fractions, and conversions to shop floor operations. Whether calculating required material dimensions to form a part, converting measures to decimals, or determining how many cartons you can lift with your forklift, shop math is important for making efficient and safe decisions.
- Forming processes - Employees should learn about the basic forming processes and equipment.
In addition to this knowledge, an understanding of safe practices and basic mechanicals also is important.
The industry must begin working with primary and secondary education providers to promote fundamental education for a new class of skilled knowledge workers.
subscribe now
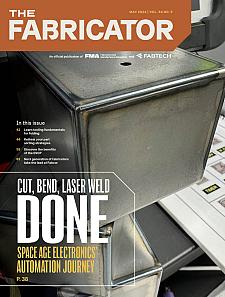
The Fabricator is North America's leading magazine for the metal forming and fabricating industry. The magazine delivers the news, technical articles, and case histories that enable fabricators to do their jobs more efficiently. The Fabricator has served the industry since 1970.
start your free subscriptionAbout the Author
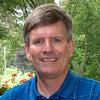
Bill Frahm
P.O. Box 71191
Rochester Hills, MI 48307
248-506-5873
- Stay connected from anywhere
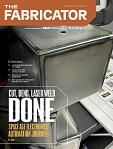
Easily access valuable industry resources now with full access to the digital edition of The Fabricator.
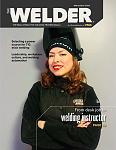
Easily access valuable industry resources now with full access to the digital edition of The Welder.
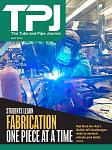
Easily access valuable industry resources now with full access to the digital edition of The Tube and Pipe Journal.
- Podcasting
- Podcast:
- The Fabricator Podcast
- Published:
- 04/30/2024
- Running Time:
- 53:00
Seth Feldman of Iowa-based Wertzbaugher Services joins The Fabricator Podcast to offer his take as a Gen Zer...
- Industry Events
Pipe and Tube Conference
- May 21 - 22, 2024
- Omaha, NE
World-Class Roll Forming Workshop
- June 5 - 6, 2024
- Louisville, KY
Advanced Laser Application Workshop
- June 25 - 27, 2024
- Novi, MI
Precision Press Brake Certificate Course
- July 31 - August 1, 2024
- Elgin,