In manufacturing, there is rarely ever just one way of doing things, and that tenet applies even to as integral a process as production itself. There are numerous methods, strategies and approaches that can be applied to production, and batch vs. continuous manufacturing is one of the major decisions that manufacturers can make.
Fortunately, this is not a decision that manufacturers need to make in a vacuum. Continuous and batch manufacturing each have distinct qualities and benefits, and manufacturers can apply these factors against their own applications and needs. Here, we will look at continuous process manufacturing and batch processing manufacturing, examining the definition and advantages of each.
What is batch process manufacturing?
Batch process manufacturing is a manufacturing method whereby discrete batches of products are moved through each step in the production process together. Each batch is made up of a specific number of pieces (which can be large or small), and no part of the batch can move forward until the entire batch is complete.
An example of batch manufacturing is a pharmaceutical product with the following steps: first, materials are mixed in the correct volumes and proportions. Next, the mixture is separated into the proper dosage; then it is packaged in the proper quantities; and finally, it is sealed. In batch manufacturing, each step described above would be completed before moving to the next step.
Advantages of batch production
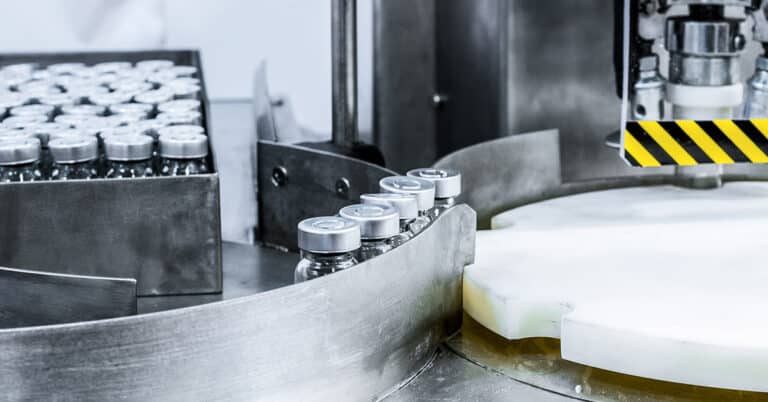
Batch production offers numerous benefits, including:
- Less setup time: In batch processes, each step typically involves an identical, repeatable function, such as mixing, sealing, cutting, and others. This means that batch production can operate in a near-turnkey manner, with less time required to set up equipment in order to fulfill each batch properly. While batch processes can sometimes be viewed as taking longer than continuous manufacturing, this component of the process offsets some of that time.
- Lower production costs: With batch manufacturing, equipment is only up and running when it is producing output. This can lead to lower costs of energy consumption, and more efficient use of personnel and resources. Batch processing can also lend itself to more efficient maintenance since it can be easier to identify low-impact times to maintain and repair equipment.
- Closer control over quality throughout the process: Quality control typically occurs at the end of each batch step, meaning that potential problems can be identified and remedied before the production cycle comes to a close. This can help to lower costs of rework and reduce the chance of rejected product making it out of the facility.
- Increased flexibility throughout the process: In addition to increased control over quality, batch processing offers more flexibility over each step of the process. For example, a mixing step for a cosmetics manufacturer can involve the same equipment with variations in raw materials and mixing ratios.
What is continuous process manufacturing?
In continuous process manufacturing, an individual piece or component moves through the entire process continually from start to finish, starting from a base or raw material and finishing with an end product (which can be a component ready to move to a different production process).
An example of a continuous process might be metal fabrication, where raw stock is worked and finished as an individual piece, not as part of a batch.
Advantages of continuous production
Continuous production offers several advantages, including:
- Higher production speed: As the name indicates, continuous production operates on an ongoing basis and is the typical type of production that people think of when they picture high-volume, 24/7 manufacturing. Depending upon the materials and processes in use, pieces can move through a continuous production line at a very high rate of speed.
- Higher volumes: Continuous production is often the method of choice for high-volume manufacturing applications due to the speed and efficiency with which it can operate.
- Quality control through performance monitoring: In continuous processing, quality is frequently monitored on an ongoing basis, including by monitoring equipment performance. Industrial sensors can detect fluctuations in temperature, air pressure, ultrasonic frequency, and other indicators of potential production abnormalities, which can provide early signals of potential quality and performance issues for equipment. By monitoring these metrics, maintenance personnel can identify and remedy potential problem situations before they lead to costly unplanned downtime.
- A more versatile range of product types: Continuous production setups can be outfitted for a broad range of product types by changing out tooling, dies, molds, and other production equipment. While these changeovers can take time, they allow for the same equipment to be used to produce a nearly limitless range of product types.
Comparing continuous and batch processing
Continuous and batch processing should always be compared against the needs of your application and your facility — there is no inherent “right” or “wrong” process. In fact, most manufacturers end up using some combination of continuous and batch processing, for example, batch processing more intricate components that can then be used in continuous processing of assemblies. With this understanding of the two approaches, you are prepared to make the right decisions for your organization.