January 3, 2024
By Joe Wiltshire | Corporate EHS & Sustainability Manager
Whatever screen you’re reading this on, there’s a good chance it was shipped on a pallet. To keep it and all the others together, workers used a lot of plastic wrap. Like a home cook transporting a pyramid of brownies, they used enough Saran Wrap to make sure nothing could fall out.
That’s a lot of plastic film.
And that’s why Fastenal partnered with Trex. By collecting, baling, and shipping the plastic film from 13 distribution centers to Trex, 600,000 pounds of plastic will be kept out of the landfill in the first year alone.
How it works
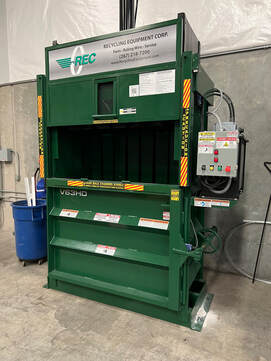
Photo credit: Fastenal Company
Let’s start with a stat. Last year, we were able to either reuse or recycle 70% of the materials that went through Fastenal’s distribution and manufacturing network. In the industry, that’s called the waste diversion rate. So, in a perfect world, everyone would be at 100%. To hit that level, all of the materials you use need to have methods where you can reuse, resell, or recycle them.
Trex is a great partner for waste reduction because they accept plastic that would otherwise be sent to a landfill, and then they turn it into outdoor products.
In fact, Trex Company is the world’s leading manufacturer of wood-alternative composites made from recycled materials. Their composite decking is very popular, but they make a variety of outdoor building products. That decking is made from 95% recycled and reclaimed materials, including a mix of polyethylene film and industrial wood scrap.
So, we’ll send them plastic film (known as “pallet wrap” in the distribution industry) and any of the bags our fasteners are packed in. Basically, anything that is plastic, stretchy, and does not crunch. Pallet wrap is vital to how we work, but once it’s off the pallets, we don’t have another use for it. And that’s really where Trex comes in.
A new level of partnership
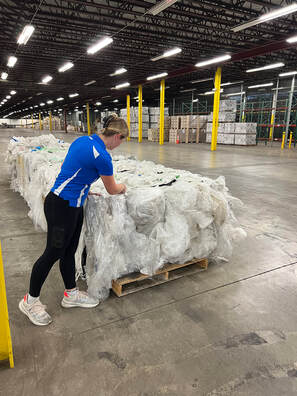
Photo credit: Fastenal Company
So, this new agreement was a perfect fit for both of us. We can divert waste while helping supply the materials needed to create more composite products.
Fastenal invested in material-handling equipment in order to:
- Prepare everything correctly
- Properly create each 40,000-pound truck load
- Then, deliver it to them in the specific dimensions and sizes that they need.
What kind of investment are we talking about? Well, each baler cost between $15,000 and $18,000. Plus, a couple of locations ordered another baler for cardboard material. So, all in, it’s more than $300,000 in equipment and infrastructure, a sizeable investment on Fastenal’s part.
What’s next?
Here’s a fun fact: Each year, Trex repurposes one billion pounds of reclaimed materials in the making of its products, including approximately 400 million pounds of plastic film.
So, what’s next? Well, I may have to update this whole article in a year or two, because the amount of diverted plastic WILL be going up.
RELATED CONTENT:
Fastenal Teams with Trex to Turn Used Plastic into Outdoor Building Products
Fastenal Releases 2023 Environmental, Social, and Governance (ESG) Report
ESG Report, Fastener Industry, Fastener News, Fastener News Desk, Supply Chain, Sustainability