Self-Reinforced Composites Lighten Load for Urban Air Mobility
Polypropylene (PP) composite reinforced with PP fibers is 52% lighter than conventional composites, potentially boosting flight time in next-gen mobility applications by 27%.
July 18, 2023
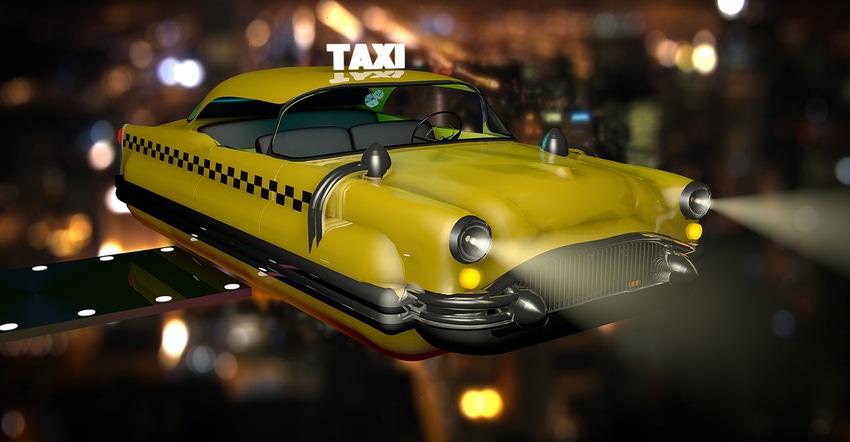
Fuel efficiency and reduced carbon emissions are essential in order for future mobility modes such as urban air mobility (UAM) to become a reality. This, in turn, will require the development of new materials with superior physical properties and recyclability. Self-reinforced composites (SRCs) are inexpensive, lightweight, and have advantages in terms of disposal and recycling because the reinforcement and base are composed of the same material. For this reason, SRCs are attracting attention as next-generation composite materials to potentially replace carbon-fiber-reinforced composites used in aircraft.
Reflecting this momentum, a research group headed by Dr. Jaewoo Kim of Solutions to Electromagnetic Interference in Future-mobility (SEIF) at Korea Institute of Science and Technology (KIST), Professor Seonghoon Kim of Hanyang University, and Professor O-bong Yang of Jeonbuk National University has successfully developed a 100% SRC using a single type of polypropylene (PP) polymer.
Until now, chemically different components have been mixed in the reinforcement or matrix as part of the SRC manufacturing process to improve flow characteristics and reinforcing-fiber impregnation, resulting in inferior physical properties and recyclability. The research team, however, has succeeded in controlling the melting point, flow properties, and fiber impregnation by deploying a “four-axis extrusion process” to adjust the chain structure of the PP matrix.
Compared with previous attempts to synthesize SRCs, the material achieved high levels of mechanical properties, improving adhesion, tensile strength, and impact resistance by 333%, 228%, and 2,700%, respectively. When applied as a frame material for a small drone, the material was 52% lighter than conventional carbon-fiber-reinforced composites and the flight time increased by 27%, confirming its potential for next-generation mobility applications.
KIST’s Kim commented: "The engineering process for 100% SRCs developed in this study can be immediately applied to industry, and we will continue to work with the joint research team and industries to secure the global competitiveness of magnetically reinforced composites."
About the Author(s)
You May Also Like