- FMA
- The Fabricator
- FABTECH
- Canadian Metalworking
Categories
- Additive Manufacturing
- Aluminum Welding
- Arc Welding
- Assembly and Joining
- Automation and Robotics
- Bending and Forming
- Consumables
- Cutting and Weld Prep
- Electric Vehicles
- En Español
- Finishing
- Hydroforming
- Laser Cutting
- Laser Welding
- Machining
- Manufacturing Software
- Materials Handling
- Metals/Materials
- Oxyfuel Cutting
- Plasma Cutting
- Power Tools
- Punching and Other Holemaking
- Roll Forming
- Safety
- Sawing
- Shearing
- Shop Management
- Testing and Measuring
- Tube and Pipe Fabrication
- Tube and Pipe Production
- Waterjet Cutting
Industry Directory
Webcasts
Podcasts
FAB 40
Advertise
Subscribe
Account Login
Search
Software helps stamper get a handle on springback
- November 15, 2022
- News Release
- Manufacturing Software
Situation
Complete Prototype Services’ sheet metal division in Clinton Township, Mich., has capabilities in design and engineering, fabrication, laser cutting, tool building, stamping, assembly and welding, quality and inspection, and low-volume production.
Using CNC press brakes, shears, benders, lasers, welding machines, and stamping presses that can handle 50 to 1,000 tons, the company can build, form, cut, and assemble any type of part.
One part the company produces often is an automotive roof header panel. In the past, employees relied on their years of experience with springback to manufacture the panel.
“Previously, we would create overbend in our tooling to allow for springback based on the length and shape of the part to be stamped,” said Ken Devroy, CAD/CAM manager. “Typically, this would result in designing and CNC cutting the tool, stamping a part, and then completing dimensional checks on the stamped part. We would then overlay the dimensional report with the 3D CAD model, which allowed us to take measurements of the differences between the stamped part and the CAD model.
“Next, we redesigned the tooling with the proper compensation to allow springback for the part to match the CAD model after the stamping process. This process always required CNC cutting of tooling surfaces at least two to three times, as well as designing and CNC cutting additional tooling to reform the part back to nominal CAD data, significantly increasing cost and lead time.”
Resolution
To cut its losses in time and money, the company decided to try AutoForm-Compensator from AutoForm Engineering. The software module allows the user to modify tooling surfaces automatically based on precise springback calculation or measured springback data. It helps define compensation regions, which are automatically adjusted using springback results, and the compensated geometry then can be used for rapid and accurate tooling validation.
Once the tooling geometry is compensated, it is automatically used as input for the next simulation. Final part geometry within the required tolerances is achieved with a minimum of correction loops.
“Now, we design our stamping tooling at the nominal CAD data,” Devroy explained. “Once complete, we are able to run stamping simulations in AutoForm software, which allows us to visualize and measure the amount of springback in the part. We then use the data provided from the software to adjust and design the tooling for the springback before CNC-cutting tooling surfaces.”
The company now can CNC-cut tooling once, eliminating the need for additional tooling to reform the part. Quoted lead time has been reduced by 25%, and tooling costs have decreased by 30%.
Related Companies
subscribe now
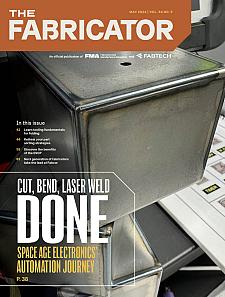
The Fabricator is North America's leading magazine for the metal forming and fabricating industry. The magazine delivers the news, technical articles, and case histories that enable fabricators to do their jobs more efficiently. The Fabricator has served the industry since 1970.
start your free subscription- Stay connected from anywhere
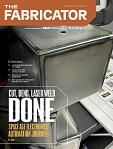
Easily access valuable industry resources now with full access to the digital edition of The Fabricator.
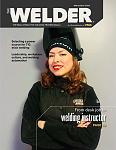
Easily access valuable industry resources now with full access to the digital edition of The Welder.
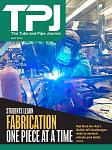
Easily access valuable industry resources now with full access to the digital edition of The Tube and Pipe Journal.
- Podcasting
- Podcast:
- The Fabricator Podcast
- Published:
- 04/16/2024
- Running Time:
- 63:29
In this episode of The Fabricator Podcast, Caleb Chamberlain, co-founder and CEO of OSH Cut, discusses his company’s...
- Industry Events
16th Annual Safety Conference
- April 30 - May 1, 2024
- Elgin,
Pipe and Tube Conference
- May 21 - 22, 2024
- Omaha, NE
World-Class Roll Forming Workshop
- June 5 - 6, 2024
- Louisville, KY
Advanced Laser Application Workshop
- June 25 - 27, 2024
- Novi, MI