- FMA
- The Fabricator
- FABTECH
- Canadian Metalworking
Categories
- Additive Manufacturing
- Aluminum Welding
- Arc Welding
- Assembly and Joining
- Automation and Robotics
- Bending and Forming
- Consumables
- Cutting and Weld Prep
- Electric Vehicles
- En Español
- Finishing
- Hydroforming
- Laser Cutting
- Laser Welding
- Machining
- Manufacturing Software
- Materials Handling
- Metals/Materials
- Oxyfuel Cutting
- Plasma Cutting
- Power Tools
- Punching and Other Holemaking
- Roll Forming
- Safety
- Sawing
- Shearing
- Shop Management
- Testing and Measuring
- Tube and Pipe Fabrication
- Tube and Pipe Production
- Waterjet Cutting
Industry Directory
Webcasts
Podcasts
FAB 40
Advertise
Subscribe
Account Login
Search
El futuro lleno de datos del corte con plasma
Cuando los consumibles se vuelven más inteligentes, lo mismo puede pasar con todo el proceso
- July 10, 2023
- Article
- Plasma Cutting
Nota del Editor: el siguiente texto se basa en “New Trends in Plasma Cutting Consumables Optimization” (nuevas tendencias en la optimización de los consumibles del corte con plasma), presentada en FABTECH 2022 en Atlanta, www.fabtechexpo.com, por Soumya Mitra, jefe del equipo de ingeniería y Kristopher Rich, director de mercadotecnia, Hypertherm Associates.
Para los fabricantes, el ambiente de negocios nunca había sido más difícil. Solo en 2021, los precios del acero subieron 215%. Las expectativas de entrega al cliente aumentaron mientras que la estabilidad de la cadena de suministro decayó.
Mientras tanto, continúa la falta de mano de obra calificada. En 2021, la Sociedad Americana de Soldadura (AWS, por sus siglas en inglés) reportó una falta de más de 400,000 soldadores calificados. Las personas calificadas son difíciles de encontrar, y cuando son contratadas, con frecuencia se van rápidamente. Sí, a veces es una realidad inevitable de un mercado con mano de obra escasa, pero también puede pasar debido a que las personas calificadas ocupan tiempo haciendo cosas que no quieren hacer: trabajar horas extra para compensar el tiempo perdido después de la descompostura de una máquina; lidiar con configuraciones inconsistentes y otros errores de compañeros no capacitados y faltos de interés. La molestia continúa, por lo que no es de extrañar que busquen otros lugares.
Los clientes siguen demandando a los fabricantes tolerancias dimensionales exigentes. Frente a una continua falta de soldadores, las compañías están recurriendo a más automatización de soldadura – tecnología que requiere un ajuste perfecto, lo cual a su vez demanda un corte de precisión.
Los fabricantes además no pueden costear el uso excesivo de operaciones secundarias como desbarbado y rectificado. Necesitan hacer los ambientes de trabajo más limpios, más seguros y más ergonómicamente amigables. Por añadidura, quieren evitar todo tiempo improductivo no planeado.
Además, las aplicaciones especializadas están en aumento. En el mercado mecanizado del corte con plasma, alrededor del 90% de los fabricantes corta con antorchas montadas en mesas estándar X-Y. Sin embargo, un número creciente de operaciones está considerando corte de bisel, corte 3D, ranurado y otras aplicaciones de plasma especializadas. Estas aplicaciones demandan consumibles hechos especialmente que atiendan las necesidades de diferentes aplicaciones, y éstos necesitan manejarse de manera efectiva.
En el campo del corte con plasma, de hecho, la mayor parte del tiempo improductivo viene de una sola fuente: problemas en el manejo de consumibles. Un operador los ensambla incorrectamente, combina partes incorrectamente, o usa los consumibles más allá de su vida útil. Sin embargo, en los años futuros, los consumibles podrían a ayudar a que la eficiencia del corte con plasma llegue a nuevas alturas – no con la fuerza bruta de la potencia de corte, sino con datos.
Las mejores prácticas para evitar el tiempo improductivo
Una fuente de poder para corte con plasma puede que sea el cerebro, pero los consumibles son el corazón de la operación. Son increíblemente importantes, y sin embargo su aplicación incorrecta también es algo increíblemente común. Un operador podría elegir el consumible equivocado para el trabajo; o podrían tener la “pila” equivocada de partes consumibles. Cada antorcha podría tener un número de partes entre tres y siete, y si éstas se combinan mal o se ensamblan incorrectamente, el corte con plasma podría salir mal.
Dichos problemas tienen diversas causas, siendo la primera la organización (vea la Figura 1). Un cajón de consumibles mal organizado puede dar lugar a todo tipo de problemas, especialmente para los operadores apurados para configurar un trabajo. En los peores casos, una estación de operador de plasma podría tener sólo un balde lleno de partes consumibles sin etiquetar, algunas nuevas, otras cerca de terminar su vida útil o más allá de su vida útil. El inventario es un desorden, y el personal calificado con salarios altos termina perdiendo tiempo escudriñando contenedores, escogiendo lo que piensan que va a funcionar, con la esperanza de que funcione.
El corte con plasma ajusta y controla la mezcla y turbulencia de gas ionizado. La manera en que fluye ese gas básicamente forma el arco de plasma. Consumibles incorrectos, mal combinados, viejos o dañados afectan el flujo y producen partes cortadas por abajo de lo óptimo.
Figura 1. Un cajón de consumibles mal organizados puede causar estragos en la eficiencia del corte con plasma.
Por ejemplo, un anillo de distribución incorrecto puede ahogar el flujo de gas, lo cual lleva a una penetración incompleta o a un corte tan malo que arruina la parte. La boquilla incorrecta con el diámetro de agujero equivocado puede dar resultados similares. El anillo de distribución o boquilla equivocados también pueden causar angularidad así como escoria (vea la Figura 2). Anillos de distribución diferentes podrían verse iguales, pero el tamaño y número de agujeros y su arreglo realmente importan, así como la manera en que están ensamblados.
Cada aplicación tiene su propia receta de flujo de gas. Un conjunto de consumibles que corta placa de 0.25 pulgadas es diferente al conjunto de consumibles requerido para cortar placa de 0.5 o 1 pulgada; algunos son comunes, algunos no. Por consiguiente, si un operador necesita cambiar de un trabajo de 0.25 pulgadas a un trabajo de 1 pulgada, necesitará cambiar ciertas partes consumibles pero dejar otras justo donde están en la pila de consumibles.
Imagine este escenario común: un operador necesita una parte consumible para hacer cierto trabajo. Hurga en el cajón desordenado y no puede encontrar lo que necesita, pero encuentra un componente que se ve similar. Bastante parecido, piensa, y arma de prisa la pila de consumibles en la antorcha. Debido a que cambiar consumibles es muy arduo, algunos operadores podrían evitarlo como la plaga, y cortar con consumibles que ya excedieron en mucho su vida útil. Todos estos escenarios producen cortes malos que requieren retrabajo como rectificado excesivo y preparación de bordes – justo las cosas que los fabricantes realmente no pueden costear en estos días.
Por supuesto, existe una razón para que la organización de consumibles sea un reto. Muchas operaciones de corte de placa tienen una vasta colección de partes consumibles, y mientras más partes usen, más difícil se vuelve mantenerlas organizadas. Además, los requerimientos de calidad del trabajo varían, y esto a su vez varía la elección del consumible. Un trabajo de corte de precisión podría requerir consumibles nuevos, mientras que un trabajo con requerimientos menos estrictos podría aprovechar un poco más consumibles más viejos. Es por eso que un cajón de consumibles puede tener partes consumibles nuevas y viejas. Las partes viejas podrían tener que tirarse pronto, y algunas es probable que debieran haberse tirado desde hace mucho.
Todo esto crea un escenario donde la calidad del corte depende de la experiencia de un operador en ese ambiente. Un operador experimentado (con frecuencia en el primer turno) sabe qué partes consumibles funcionan bien y cuándo; él podría saber “leer” una boquilla o protección y decir si está cerca del final de su vida. Podría ocupar algunos minutos escudriñando el cajón, pero ha escudriñado ese mismo cajón por años, así que lo conoce bien. Sin embargo, si vamos al segundo o al tercer turno, el escenario cambia. Los operadores más nuevos escudriñan, se esfuerzan al máximo, pero pueden acabar confundiendo los consumibles, o eligiendo el consumible equivocado por completo.
Peor aún, los problemas con los consumibles podrían ser sólo una causa raíz de los problemas con la calidad de corte. Por ejemplo, si una parte tiene escoria excesiva, el amperaje incorrecto (como cuando se está cortando a 130 amperes cuando se debería cortar a 200 amperes) podría ser un factor que afecta. Y debido a que el corte con plasma puede depender de la reacción del gas ionizado (oxígeno reaccionando con hierro en acero al carbón, por ejemplo), la elección del gas también importa. En general, el corte con plasma implica la interacción de infinidad de variables, y mientras más consistentes y repetibles sean esas variables, mejor.
Con un primer paso fundamental, los talleres pueden organizar sus consumibles, luego estandarizar y documentar el proceso de selección (vea la Figura 3). Además, pueden capacitar a los operadores para inspeccionar consumibles y documentar lo que ven.
La boquilla y el electrodo necesitan cambiarse con frecuencia pues se desgastan más rápido que los otros componentes. Así que los operadores usualmente inspeccionan los otros componentes, incluyendo protecciones y anillos de distribución, y los cambian si su condición lo justifica. Idealmente, deben documentarse las mejores prácticas y la utilización de consumibles.
Como siguiente paso, algunas operaciones están eligiendo eliminar la colección de partes consumibles y cambiarla por un sistema de consumibles en forma de cartucho. Cada cartucho comprende varias piezas y partes que van en una antorcha de plasma tradicional (vea las Figuras 4 y 5). Cuando el operador necesita cambiar a un nuevo amperaje, cambia el consumible de la antorcha por un cartucho diseñado para manejar ese amperaje. Los componentes dentro del cartucho, alineados en la fábrica, están diseñados para desgastarse a una velocidad similar. El uso de cartuchos da lugar a una operación que no tiene una mezcla de partes consumibles viejas y nuevas, y por lo tanto, mejora la calidad de corte.
Desarrolle una estrategia para los consumibles
En todo caso, sin importar qué consumibles usa un taller, tradicionales o en cartucho, necesita procedimientos en torno a la inspección de consumibles, a su organización y a su reemplazo. Esos procedimientos sirven como el punto de referencia para capacitación de los operadores y calendarización de la producción. Si todo mundo – en todos los turnos – conoce los fundamentos del corte con plasma, qué consumibles van con qué, y cuándo es momento de cambiar los componentes desgastados, seguro que el tiempo improductivo no planeado en el corte con plasma se reducirá drásticamente.
Figura 2. Un corte con escoria y líneas de arrastre inconsistentes revela problemas en el flujo de gas, probablemente relacionados con consumibles desgastados o equivocados, como los anillos de distribución.
Sin embargo, para mejorar más, la industria se topa con a una especie de barrera tecnológica. Para entender por qué, piense en dos escenarios que involucran el corte con plasma en una mesa X-Y convencional. En el primer escenario, un operador podría pretender aprovechar los consumibles hasta su último momento de vida útil. Al fin y al cabo, los operadores pueden observar problemas cuando ocurren y ajustar para compensar.
Por el contrario, una operación de corte con plasma altamente automatizada podría cambiar consumibles con mucha frecuencia, mucho antes de que las partes consumibles hayan llegado al final de su vida útil. El costo de error y desperdicio es alto, así que la compañía decide finalmente absorber el costo por consumibles extra.
Ambas estrategias pueden funcionar, pero también son imprecisas. Un operador podría alargar la vida de algunas partes consumibles y terminar con bordes de corte malos. Peor aún, los bordes de corte de mala calidad seguidos por un rectificado excesivo podrían cocinarse en la operación, sin que haya alguien que piense que podría haber una mejor manera. Por el contrario, cuando las operaciones cambian los componentes de la antorcha con mucha frecuencia, gastan más en consumibles y con frecuencia hacen más cambios de lo necesario.
Los operadores hacen lo mejor que pueden con la tecnología que se les da. Al fin y al cabo, no reciben información en tiempo real de la antorcha en sí. Los operadores experimentados observan el arco, escuchan el silbido agudo del plasma para determinar su estado, y monitorean la operación en el controlador. Cuando el tono del silbido cambia, podrían suponer que el interior de la boquilla se está erosionando. Por supuesto, no lo saben hasta que paran el sistema e inspeccionan los consumibles. Lo peor de todo es que todo esto es reactivo: el problema ya ocurrió.
Sin embargo, eso está empezando a cambiar. Algunos de los avances más recientes en el corte con plasma incluyen sensores directamente en el cartucho de consumibles de la antorcha. Actualmente, la tecnología se está usando en el mercado industrial ligero, principalmente para configurar el sistema de corte para diferentes aplicaciones. En este segmento, un taller podría necesitar consumibles diseñados para corte manual, corte mecanizado y hasta ranurado. Los cartuchos tienen código de colores con base en la aplicación (vea la Figura 6) para ayudar a los operadores a seleccionar correctamente. El cartucho tiene un circuito integrado auxiliar (chipset) que puede comunicarse directamente con el control del sistema. Esto significa que el sistema de plasma se auto-configura con base en su cartucho de consumibles.
El chip en el consumible además registra datos en cada trabajo que hace. La información en los cartuchos puede leerse usando un teléfono inteligente mediante una app. Así que, cuando los operadores o técnicos escanean los datos en el cartucho, pueden ver cuándo, dónde y cómo se ha usado ese consumible. Pueden ver detalles que incluyen información de configuración del sistema; ajustes de corriente y presión; a qué sistemas de plasma se conectaron los consumibles; información de uso; cuántos cortes hizo y las horas de arco de transferencia; y cuántos arcos de transferencia se iniciaron e hicieron contacto con la pieza de trabajo. Los datos también revelan con qué frecuencia entró el sistema en modo de formación de arco, donde el plasma hace arco dentro del consumible antes de transferirse a la superficie de la pieza de trabajo. Mientras más formación de arco ocurra, es probable que la vida del consumible sea más corta.
El poder de los datos
La tecnología de chip en la antorcha refuerza la condición a prueba de error (en todo el sentido de la palabra). Cuando el cartucho consumible y el control del sistema de plasma se comunican, están en la misma página. Cuando hay una discordancia entre los ajustes del sistema de plasma y el consumible, el sistema alerta al operador, quien entonces puede decidir cómo proceder.
Los cartuchos consumibles con chip integrado también ayudan a la solución de problemas pues pueden registrar códigos de error y otros parámetros operativos. Considere una aplicación de corte donde algunos consumibles duran tres horas mientras que otros duran seis. El operador escanea el cartucho mediante un teléfono inteligente en ambos consumibles y abre el historial de cada uno. Comparando los datos, junto con otros datos operacionales que el proceso capture, la compañía descubre que el consumible con la vida más corta tenía un ajuste menor de flujo de aire. Así que, ajustan el flujo de aire, y problema resuelto.
En dichas situaciones, los datos podrían ayudar a localizar lagunas en la capacitación. Los datos del chip del cartucho pueden ligarse a operadores específicos. Si los consumibles de un operador fallan prematuramente, usan eso para localizar el problema y difundir las mejores prácticas del corte con plasma en toda la compañía, en todos los turnos.
Correlacionar datos también ayuda a revelar fuentes de inconsistencias entre operaciones y entre turnos. Por ejemplo, los talleres con frecuencia encuentran que los sistemas de corte con plasma en el segundo o en el tercer turno operan a presiones de gas más altas que los sistemas en el primer turno. ¿Por qué? Hay menos sistemas operando en el segundo y en el tercer turno. El mismo compresor que da servicio a varias máquinas no puede dar abasto a los flujos requeridos en el primer turno, lo que da lugar a condiciones de presión baja (y abajo del valor óptimo). Con frecuencia, dicha variación permanece oculta, y los operadores simplemente hacen todo lo que pueden por adaptarse. Con datos, una operación de corte con plasma puede hacer el flujo de gas consistente en todos los turnos, hacer el corte más repetible y mejorar la calidad totalmente.
Figura 3. Un cajón de consumibles bien organizado tiene consumibles agrupados por tipo, por aplicación y por vida restante. Los consumibles nuevos no se ponen aleatoriamente al lado de partes consumibles usadas cuya vida útil está por acabar.
Cómo podría ser el futuro
Los datos ayudan a un taller a tomar mejores decisiones. Para el fabricante de placa futuro, un sistema de plasma lleno de datos podría ver un trabajo de corte de precisión en la cola, luego advertir al personal que es muy probable que los consumibles actuales no sean suficientes para esos requerimientos de calidad de corte.
Con esa información, el operador cambiaría los consumibles antes de cortar el trabajo. De manera alternativa, podría cambiar la secuencia de trabajos usando los consumibles actuales para procesar un nido donde la angularidad y otras variables de corte no sean tan críticas. Una vez terminado ese trabajo, podría cambiar consumibles e iniciar el trabajo de corte de precisión. Dichos datos incluso podrían influir en la manera en que una compañía anida partes, calendariza sus trabajos o incluso cotiza su trabajo.
Observe que todo esto representa un potencial futuro, no es el estado actual. Ciertamente, el corte con plasma lleno de datos está en una etapa temprana, pero su potencial es innegable. Una vez que la recolección de datos prolifere y crezca el conjunto de datos, el corte con plasma en general se volverá más inteligente – idealmente, sin operadores hurgando en un balde de consumibles, agarrando un anillo de distribución o una boquilla, ensamblándolos desesperadamente en la antorcha y arrancando el sistema con la esperanza de que funcione.
About the Publication
Compañías Relacionadas
subscribe now
FMA Communications ha introducido al mercado la edición en Español de la revista The Fabricator. Esta versión consiste del mismo tipo de artículos técnicos y sección de lanzamientos de nuevos productos que actualmente presentan el personal de primera categoría de Fabricator en Inglés.
start your free subscription- Podcasting
- Podcast:
- The Fabricator Podcast
- Published:
- 05/14/2024
- Running Time:
- 62:12
Cameron Adams of Laser Precision, a contract metal fabricator in the Chicago area, joins the podcast to talk...
- Trending Articles
Anidado para la estabilidad del corte láser
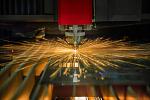
Seguridad en la soldadura desde el inicio
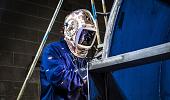
El software guía a los soldadores a través de instrucciones de trabajo
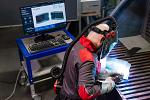
La rueda reduce las fuerzas de empuje/tracción hasta en un 50%

Gafas protectoras diseñadas para trabajadores que necesitan lentes correctivos
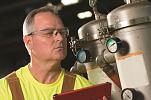
- Industry Events
Laser Welding Certificate Course
- May 7 - August 6, 2024
- Farmington Hills, IL
World-Class Roll Forming Workshop
- June 5 - 6, 2024
- Louisville, KY
Advanced Laser Application Workshop
- June 25 - 27, 2024
- Novi, MI
Precision Press Brake Certificate Course
- July 31 - August 1, 2024
- Elgin,