Smart Factory Consultant
- FMA
- The Fabricator
- FABTECH
- Canadian Metalworking
Categories
- Additive Manufacturing
- Aluminum Welding
- Arc Welding
- Assembly and Joining
- Automation and Robotics
- Bending and Forming
- Consumables
- Cutting and Weld Prep
- Electric Vehicles
- En Español
- Finishing
- Hydroforming
- Laser Cutting
- Laser Welding
- Machining
- Manufacturing Software
- Materials Handling
- Metals/Materials
- Oxyfuel Cutting
- Plasma Cutting
- Power Tools
- Punching and Other Holemaking
- Roll Forming
- Safety
- Sawing
- Shearing
- Shop Management
- Testing and Measuring
- Tube and Pipe Fabrication
- Tube and Pipe Production
- Waterjet Cutting
Industry Directory
Webcasts
Podcasts
FAB 40
Advertise
Subscribe
Account Login
Search
Perfeccionando el ciclo de corte-doblado
El futuro de la fabricación de chapa flexible
- By Felix Weigelt
- December 1, 2022
- Article
- Automation and Robotics
En la fabricación autónoma, los algoritmos de software identifican piezas adecuadas para procesos específicos de corte y doblado, asignan enrutamientos y escriben programas, todo sobre la marcha y en segundo plano.
La fabricación es, y siempre ha sido, una industria en constante evolución. Pero la tasa de cambio parece haberse acelerado en los últimos años, junto con un crecimiento en los pedidos. Mantener el ritmo de la creciente demanda de los clientes ha planteado desafíos para muchos fabricantes. Simplemente parece que no hay suficientes fabricantes para satisfacer la necesidad creciente.
Durante la pandemia, el comercio del fabricante tradicional se redujo drásticamente ya que muchos decidieron jubilarse anticipadamente o pasar a nuevos puestos que prometían ganancias salariales. Al mismo tiempo, la industria ha visto una tendencia creciente hacia una alta individualización y lotes más pequeños. Los clientes exigen la individualización de sus productos finales y quieren ver el estado de sus pedidos en producción. Esto ha estimulado una mayor complejidad en la fabricación junto con la necesidad de una transparencia continua mientras se reducen los tamaños de los lotes. Hacer mejoras en los procesos individuales no es suficiente.
Es posible que los robots no hayan tenido mucho sentido en entornos de producción anteriores, pero los cambios recientes en la producción requieren otra mirada al papel potencial de la automatización en la fabricación de metales. Un área notable donde la automatización ha producido ganancias, particularmente para los fabricantes medianos, es en el ciclo de corte y doblado.
El impacto de los procesos indirectos
Un estudio realizado hace algunos años por el Instituto Fraunhofer y TRUMPF analizó cuánto tiempo dedican los fabricantes a procesos indirectos relacionados con la organización y entrega de piezas a su siguiente paso. El estudio encontró que casi el 80% del tiempo de producción se dedica a esas tareas indirectas. Esto deja solo el 20 % del tiempo de producción para tareas de valor agregado (las generadoras de dinero) como cortar, doblar, soldar y ensamblar. Los fabricantes que buscan aumentar los ingresos deben reducir ese 80 % automatizando y optimizando esos procesos.
La industria ha visto solo un uso limitado de la automatización. Ciertamente, los fabricantes han utilizado torres de almacenamiento, sistemas de carga/descarga y automatización de doblado durante varias décadas. Sin embargo, debido a la limitada flexibilidad de los sistemas existentes, la mayor parte de ese uso de la automatización se ha limitado a trabajos de alto volumen y baja combinación, generalmente con Fabricantes de Equipo Original (OEM’s) o grandes fabricantes por contrato con una demanda predecible y productos altamente estandarizados. Hasta la fecha, la industria realmente no ha visto la adopción generalizada de sistemas de automatización complejos y altamente sofisticados en entornos flexibles.
La mayoría de los fabricantes norteamericanos trabajan en entornos con cambios de demanda rápidos y, a menudo, extremos en diferentes máquinas y centros de trabajo. Algunos pedidos tienen piezas cortadas solamente, otros tienen partes cortadas y formadas, otros requieren soldadura. Los rápidos cambios en las piezas, los niveles de demanda y las rutas de trabajo dificultan la planificación de ciclos de producción estables y predecibles para adaptarse a la demanda del cliente.
Las diferentes geometrías de las piezas, los requisitos de superficie y las expectativas de calidad de los bordes pueden influir en la tecnología que los fabricantes seleccionan para fabricar esas piezas. Por ejemplo, una parte con persianas y características formadas podría prestarse para el punzonado. Si un cliente espera que no se introduzca oxígeno en un borde cortado durante el corte con láser entonces el trabajo podría prestarse a láseres de fibra de alta potencia. O tal vez un pedido contenga piezas con características complejas de doblado redondo, que podrían producirse mejor en un proceso de doblado de paneles sin rayones.
Tecnología heredada y disposición del área de producción
Históricamente, muchos fabricantes con entornos de alta mezcla establecieron un diseño centrado en el proceso con máquinas punzonadoras y de corte por láser en un departamento y prensas dobladoras en otro. Tal distribución puede ofrecer flexibilidad. Por ejemplo, si es necesario perforar una pieza y luego doblarla en una dobladora de paneles, los manipuladores de materiales pueden mover el trabajo fácilmente entre los pasos del proceso utilizando carros, montacargas u otros métodos manuales. Si se pierde el contrato de una pieza en particular el fabricante puede llenar esa nueva capacidad disponible con trabajo adicional en la dobladora de paneles. O, si se requieren piezas sin marcas de “mordiscos”, el trabajo se puede cambiar de la punzonadora a una máquina láser o combinada.
Este enfoque hace el trabajo y ha funcionado bien durante décadas en la fabricación de chapa, pero también tiene desventajas significativas. Las desventajas incluyen piezas perdidas, tiempo perdido debido al manejo manual de materiales y el costo de los montacargas. Sin embargo, estos factores en realidad no incurren en el mayor gasto de hacer negocios como este. La mayor parte de los ingresos perdidos se puede atribuir a una reducción en el capital de trabajo.
Piénselo de esta manera: cada empresa necesita una cierta cantidad de capital para hacer negocios diariamente. Al igual que una persona, una empresa necesita una cierta cantidad de dinero en cualquier momento para hacer negocios. Esta cantidad de dinero se llama capital de trabajo.
Un sistema integrado de corte y doblado (en este caso, un láser, un punzón y dos prensas dobladoras robóticas) tiene torres que almacenan material en bruto y un almacenamiento de trabajo en proceso. Ese almacenamiento garantiza que todas las máquinas puedan producir a mayor capacidad y lograr un mayor rendimiento.
En un entorno en el que las piezas se cortan, se separan manualmente y luego se transportan con montacargas para doblarlas, las piezas de trabajo en proceso (WIP) y, por lo tanto, el inventario de piezas entre los pasos del proceso, pueden volverse inmensos. En un modelo típico centrado en el proceso, la mayoría de las piezas esperan el 98.6 % del tiempo de producción. Tales operaciones pueden tener miles o incluso cientos de miles de piezas de trabajo en proceso (WIP) esperando el siguiente paso en la producción. Eso representa una suma considerable de capital de trabajo ligado a partes sin terminar en el taller. En algunas organizaciones, ese valor supera los millones de dólares.
En tiempos de aumento de la inflación y las tasas de interés, los altos niveles de piezas de trabajo en proceso (WIP) pueden crear una carga financiera real. Imagine que es un fabricante por contrato de tamaño mediano con ingresos de $20 millones por año. Su margen de beneficio es de alrededor del 15% anual y su tiempo de entrega promedio es de alrededor de ocho semanas. Una vez que se realiza un pedido, se tarda unas dos semanas hasta que se cortan las piezas y otras seis semanas hasta que se envían. Esto significa que las piezas permanecen como piezas de trabajo en proceso (WIP) durante unas seis semanas. Multiplique $20 millones por el 85% del costo de los bienes vendidos y las partes que estarán en su taller durante seis semanas ($20 millones × 85% × 6/52), y encontrará que tiene $1.9 millones en capital de trabajo inmovilizado en partes que se encuentran en el taller. Eso ya es mucho dinero, pero si las tasas de interés son altas y si utiliza una línea de crédito para pagar ese capital de trabajo, los pasivos financieros pueden acumularse rápidamente.
Nuevas opciones para corte y doblado integrados
¿Cómo puede reducir ese almacenamiento y reducir el capital de trabajo entre esos diferentes pasos del proceso? Realmente, solo hay una opción. Debe acortar su tiempo de producción y reducir el búfer entre diferentes centros de trabajo. Es más fácil decirlo que hacerlo, ya que es complejo dirigir los procesos en consecuencia, especialmente considerando el elemento humano de las piezas móviles entre el corte y el doblado.
Compare la planta de fabricación de bajo volumen y mezcla alta con un aeropuerto importante. Imagine programar diferentes aviones, algunos a tiempo y otros retrasados, administrar diferentes horarios de salida mientras vigilas el clima siempre impredecible. Este escenario es comparable a un entorno de fabricación flexible con demandas y solicitudes de clientes en constante cambio. ¿Cómo gestionan los controladores aéreos este problema? Se basan en el radar y otros modelos analíticos de simulación por computadora para ayudar a tomar las mejores decisiones.
En el pasado, el software de gestión de fabricación podía ser complejo y extremadamente caro. Gracias a una aceleración en el desarrollo de software, esto ha cambiado. El software complejo específicamente para el entorno de fabricación ahora está disponible a un costo relativamente bajo. Utilizando algoritmos de programación avanzados, los sistemas de ejecución de fabricación (MES) ayudan a los fabricantes a aumentar el rendimiento, reducir los niveles de piezas de trabajo en proceso (WIP) y reducir el capital de trabajo.
Acortar el ciclo de corte y doblado
Los tableros de producción de sistemas de ejecución de fabricación (MES) muestran y comunican la orden más urgente al operador en tiempo real. Una vez que el operador comienza a ejecutar una pieza determinada, la máquina le comunica al sistema que la pieza está en proceso y el software realinea o reprograma las prioridades sobre la marcha en diferentes centros de trabajo.
Todo esto sucede con un objetivo en mente: la reducción del tiempo de procesamiento y, con ello, el capital de trabajo. Cuando llegan los pedidos de piezas nuevas, los algoritmos comprueban rápidamente cuáles de esas piezas se prestan para el doblado robótico mediante la creación de programas para la máquina dobladora y para el robot. Una vez que se toma esa determinación, es fácil para alguien como un ingeniero de control de sistemas programar y asignar las órdenes a una máquina dobladora manual o robótica.
Los efectos de la digitalización
Para adaptarse a las configuraciones que consumen mucho tiempo y que involucran la programación en la máquina y los dobleces de prueba, los talleres de fabricación tradicionales utilizaron grandes espacios intermedios entre el corte y el doblado. Gracias al software y los cambios rápidos de herramientas, las configuraciones toman menos tiempo y el almacenamiento se ha reducido drásticamente. Las operaciones de mezcla alta aún necesitan este almacenamiento para acomodar tiempos de ciclo variables, pero la tecnología moderna ha hecho que la mayoría de las configuraciones impredecibles sean cosa del pasado.
Por supuesto, estas mejoras de procesos solo son posibles utilizando algoritmos complejos e inteligencia artificial. Gracias a los modelos de aprendizaje automático en constante mejora, los algoritmos se vuelven mejores para tomar esas determinaciones. Verdaderamente, esto es lo que permite soluciones integradas de corte y doblado que tienen sentido en la fabricación de bajo volumen y alta mezcla.
Los algoritmos permiten a los fabricantes de equipo original (OEM’s) construir máquinas altamente complejas con una separación de piezas avanzada y confiable. Con estos algoritmos, los modelos informáticos funcionan en segundo plano, lo que demuestra la tasa de éxito para separar geometrías de piezas específicas de forma fiable; en base a esto, recomiendan las máquinas que mejor se adaptan.
Esta configuración conecta una punzonadora y una dobladora de paneles con una torre de almacenamiento en el medio que actúa como amortiguador. Hoy en día, los algoritmos ayudan al software a identificar qué proceso (como el punzonado contra el corte por láser o las prensas dobladoras contra las dobladoras de paneles) se adapta mejor a un trabajo en particular.
Lo mismo sucede con el doblado robótico automático. Los algoritmos determinan qué pinzas se requieren para ejecutar las piezas en el equipo, así como las herramientas correctas, y escriben programas para el robot y las máquinas dobladoras, sobre la marcha y en segundo plano, antes del lanzamiento a producción. Esta tecnología permite sistemas integrados de corte y doblado donde un láser o punzonadora corta y separa las piezas. Luego, esas piezas se almacenan en el sistema de almacenamiento antes de que una máquina dobladora robótica automatizada las solicite.
Los sistemas de corte y doblado conectados directamente sin una torre intermedia existen desde hace algún tiempo, pero funcionan bien solo en ciertas partes, incluidas aquellas que dedican el mismo tiempo al corte y al doblado. Si un proceso u otro corre más lento o más rápido, entonces la cortadora o la dobladora tendrán que esperar a que la otra termine. Esto crea un cuello de botella y subutiliza el costoso equipo de producción.
Los sistemas con una torre en el medio contrastan con eso. Mediante el uso de una torre, el procesamiento por lotes se vuelve factible y cada máquina puede producir el mayor nivel de producción sin ralentizarse o ralentizar otra máquina. Si una máquina es más lenta, la otra puede procesar piezas de la torre de almacenamiento intermedio o de equipos fuera del sistema automatizado.
Tecnología para la próxima generación de fabricantes
En el futuro, la fabricación autónoma será la clave del éxito especialmente cuando los fabricantes de América del Norte luchan por ocupar puestos y encontrar jóvenes que estén entusiasmados con una carrera larga y estable en la fabricación. Al establecer procesos autónomos, los fabricantes también pueden esperar que las máquinas funcionen más ya que no requieren la presencia de operadores.
A medida que la industria continúa avanzando hacia niveles más altos de automatización, los fabricantes estadounidenses serán aún más competitivos en el mercado mundial y sentarán las bases para la próxima generación. Los fabricantes de hoy requieren personas con nuevas habilidades. En los últimos 50 años, los operadores se adaptaron desde el funcionamiento de las cizallas hasta la programación y el funcionamiento de equipos CNC. La próxima generación se centrará en hacer que los procesos sean autónomos.
About the Author
Felix Weigelt
1900 W. Central Road
Hoffman Estates, IL 60192
About the Publication
Compañías Relacionadas
subscribe now
FMA Communications ha introducido al mercado la edición en Español de la revista The Fabricator. Esta versión consiste del mismo tipo de artículos técnicos y sección de lanzamientos de nuevos productos que actualmente presentan el personal de primera categoría de Fabricator en Inglés.
start your free subscription- Podcasting
- Podcast:
- The Fabricator Podcast
- Published:
- 05/14/2024
- Running Time:
- 62:12
Cameron Adams of Laser Precision, a contract metal fabricator in the Chicago area, joins the podcast to talk...
- Trending Articles
Anidado para la estabilidad del corte láser
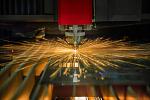
Seguridad en la soldadura desde el inicio
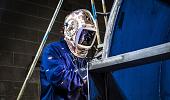
El software guía a los soldadores a través de instrucciones de trabajo
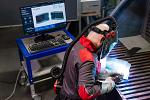
La rueda reduce las fuerzas de empuje/tracción hasta en un 50%

Gafas protectoras diseñadas para trabajadores que necesitan lentes correctivos
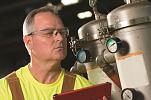
- Industry Events
Laser Welding Certificate Course
- May 7 - August 6, 2024
- Farmington Hills, IL
World-Class Roll Forming Workshop
- June 5 - 6, 2024
- Louisville, KY
Advanced Laser Application Workshop
- June 25 - 27, 2024
- Novi, MI
Precision Press Brake Certificate Course
- July 31 - August 1, 2024
- Elgin,