- FMA
- The Fabricator
- FABTECH
- Canadian Metalworking
Categories
- Additive Manufacturing
- Aluminum Welding
- Arc Welding
- Assembly and Joining
- Automation and Robotics
- Bending and Forming
- Consumables
- Cutting and Weld Prep
- Electric Vehicles
- En Español
- Finishing
- Hydroforming
- Laser Cutting
- Laser Welding
- Machining
- Manufacturing Software
- Materials Handling
- Metals/Materials
- Oxyfuel Cutting
- Plasma Cutting
- Power Tools
- Punching and Other Holemaking
- Roll Forming
- Safety
- Sawing
- Shearing
- Shop Management
- Testing and Measuring
- Tube and Pipe Fabrication
- Tube and Pipe Production
- Waterjet Cutting
Industry Directory
Webcasts
Podcasts
FAB 40
Advertise
Subscribe
Account Login
Search
Mejore el manejo de sus consumibles de plasma
La tecnología moderna ayuda al operador a hacer los cambios correctos en el momento correcto
- January 17, 2023
- Article
- Plasma Cutting
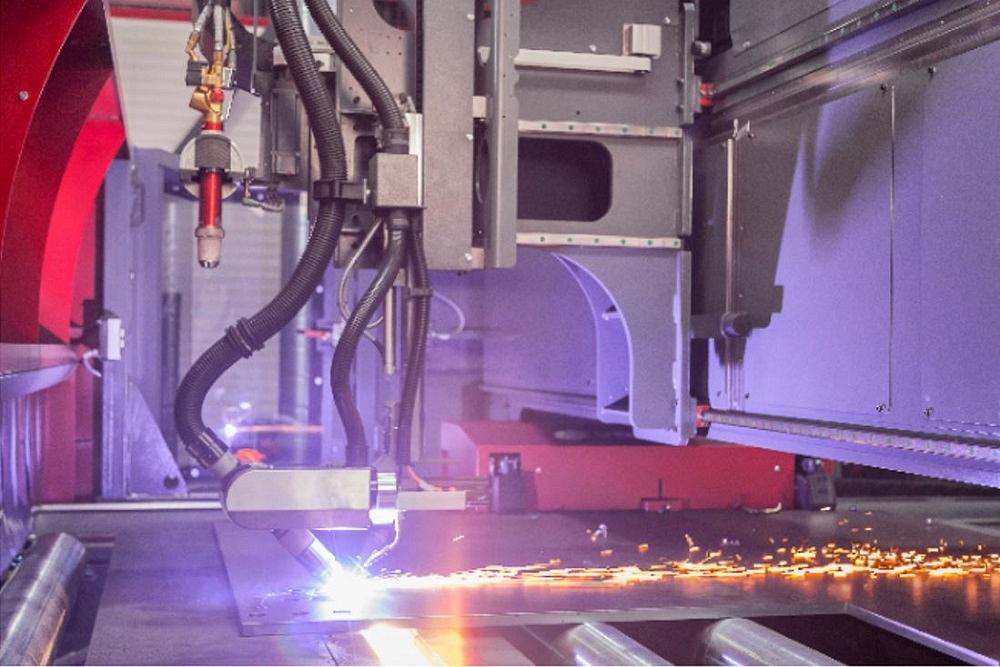
Una de las mejores maneras de mantener el tiempo productivo al cortar con plasma es reconocer cuándo los consumibles de corte con plasma deben cambiarse o no. Voortman Steel Machinery
Nota del editor: este artículo se adaptó del seminario virtual de Voortman Steel Machinery e Hypertherm “How to improve your plasma consumable management” (cómo mejorar el manejo de sus consumibles de plasma) del 23 de junio. Entre los oradores estuvieron Joey Schreur, gerente de unidad de negocios, placas, Voortman; Stef Rohaan, gerente de producto, placas, Voortman; y Timo Lecher, gerente de ventas de consumibles, Hypertherm. Puede ver el seminario virtual completo en www.voortman.net/en/knowledge-base/plasma-consumable-management-webinar.
La mayoría de las compañías que operan maquinaria de corte con plasma sienten que su equipo de planta hace lo correcto en cuanto al reemplazo de consumibles. Confían en que sus operadores están sacando el máximo provecho de la maquinaria de corte con plasma, optimizando el desempeño del equipo sin sacrificar calidad.
Aun cuando estas compañías probablemente tengan razones de sobra para creer en sus operadores de máquina, también es probable que quieran revisar la caja de consumibles usados. Es ahí donde sale a flote la verdad. A veces la gente simplemente tiene malos hábitos.
Un excelente ejemplo de una mala decisión es un operador de máquina de corte con plasma que cambia los consumibles antes de un nuevo trabajo porque no quiere que los consumibles se acaben a la mitad del trabajo de corte. Este tipo de cambio de consumibles puede ocurrir aun cuando el electrodo, la boquilla y la tapa de protección todavía son utilizables.
Algunos otros operadores juran que pueden monitorear la vida de los consumibles por el sonido. Creen que todo está bien hasta que la frecuencia cambia drásticamente. Desafortunadamente, el oído humano no es una herramienta de medición precisa. Para el momento en que un operador experimentado cree haber escuchado algo que sugiere la necesidad de un cambio de consumibles, la antorcha de plasma puede haber cortado mal varias partes, corriendo el riesgo de que éstas se tengan que desechar.
Con el software CAM moderno, operadores de todos los niveles de experiencia pueden hacer los cambios correctos de consumibles en el momento correcto cuando se trata de corte con plasma. El software monitorea los inicios/paros y la distancia de corte, usa esos datos para determinar el desgaste de la antorcha, y notifica al operador cuando los consumibles de la antorcha excedieron sus límites. Como resultado, los operadores de máquina ya no cargan con toda la responsabilidad.
1. Elija la secuencia correcta
Un operador de máquina de corte con plasma que trabaja en una mesa moderna se da el lujo de conocer muchos detalles sobre el trabajo que está por iniciar. Puede iniciar el día viendo la lista de trabajos, echando un vistazo a los nidos y haciendo los ajustes que se requieran.
Muchos operadores no pueden darse el lujo de concentrarse en una máquina durante un turno completo. Tienen responsabilidades por otro lado. Por eso es importante que el operador pueda ajustar la secuenciación del trabajo.
La función de secuenciación en las máquinas de corte de placa más avanzadas le brinda al operado la capacidad de ver qué nidos usan los mismos consumibles, lo cual le permite agruparlos en un trabajo que puede dejarse para operar sin atender durante un tiempo establecido. Esta función de control también le da al operador la información sobre la vida de los consumibles. ¿Será necesario algún cambio de consumible durante el rato de operación sin atender? Si ciertos consumibles necesitan reemplazarse en medio de una operación sin atender, ¿cómo ajusta el operador la secuencia para conseguir el mayor tiempo posible de operación sin atender, sin sacrificar desempeño del corte con plasma?
Un control moderno le da al operador toda la información que necesita saber para mantener la calidad de la producción y el rendimiento, al mismo tiempo que saca el máximo provecho de los consumibles de corte con plasma.
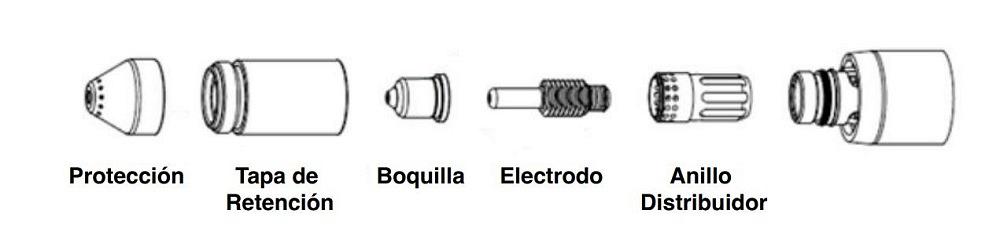
El electrodo, la boquilla y la protección son los consumibles que más se cambian, y usualmente se cambian al mismo tiempo porque se desgastan al mismo ritmo. Hypertherm
2. Conozca lo que se está cortando
Para quienes han operado mesas de corte con plasma no es secreto que trabajar con espesores de material diferentes requiere antorchas diferentes. La chapa metálica gruesa requiere altos amperajes y consumibles diferentes a los necesarios para cortar chapa delgada. En el corte con plasma, un tamaño no va con todo.
En los tiempos anteriores a los controles modernos, los operadores usaban tablas de corte suministradas por el fabricante de la fuente de plasma para elegir qué consumibles estaban bien para el trabajo. Actualmente, esa información se incorpora en el software de programación de la máquina.
Sin embargo, los parámetros usados como guía para el proceso de corte con plasma van más allá del simple espesor de la chapa y del tipo de material. Los operadores pueden seleccionar los parámetros de corte óptimos para la mejor calidad de borde o alguna variación que contrapese la calidad general del corte con la velocidad de corte.
La realidad es que para algunos talleres no es tan importante la calidad del borde de las partes cortadas con plasma que reciben. Si ése es el caso, la compañía de fabricación de metal probablemente se va a enfocar en optimizar el proceso de corte, en un esfuerzo por cumplir o mejorar los tiempos de entrega. Para aquellos talleres más interesados en la calidad del borde, el proceso de corte con plasma puede ajustarse para brindar estos resultados óptimos.
Es aquí donde el software de anidado y programación de la máquina ponen al operador de la máquina en la dirección correcta. Para el momento en que carga el trabajo, el amperaje correcto de la fuente de poder y los consumibles apropiados han sido designados para el trabajo. Esto ayuda a asegurar que el operador tome la decisión correcta y evita errores indeseados.
3. Acerca de esa longitud de arco…
El proceso de pre-corte de la antorcha que toca por arriba la superficie del material asegura que la máquina de corte con plasma mantenga la distancia óptima entre el material y la parte inferior de la antorcha. Sin embargo, no es ahí donde acaba la medición.
Después de la perforación inicial y el inicio del proceso de corte, la maquinaria moderna de corte con plasma mide el voltaje del arco. (Midiendo el voltaje del arco, puede determinarse la longitud del arco desde el electrodo hasta la placa.) Ésta mantiene este monitoreo durante toda la vida del electrodo, lo que asegura que la antorcha permanezca a la misma altura de corte incluso cuando el electrodo se desgasta y el emisor de hafnio dentro se vuelve más pequeño, y cuando la distancia entre la antorcha y el material cambia debido a diferencias de altura en la chapa.
Este control de altura es importante pues un arco de plasma no es perfectamente cuadrado. El arco está ahusado en los extremos, de manera similar a la flama de una vela. Para lograr la mejor calidad de corte y vida de los consumibles, la parte más cuadrada del arco—que es la parte central—necesita hacer contacto con la placa.
En el pasado, conforme el emisor de hafnio dentro del electrodo se reducía, la antorcha podía moverse más cerca del material para mantener el arco, aun cuando podía volverse más inestable. Como resultado, la falta de un arco estable , podría afectar la perforación y los cortes iniciales.
Al mantener un arco estable y la altura de corte correcta, la antorcha de plasma es capaz de producir una perforación limpia, un inicio más corto, y sin ondulaciones durante el proceso de corte subsecuente pues la porción más cuadrada del arco mantendría contacto con la pieza de trabajo. Además, los consumibles van a durar más.
4. Evite esfuerzos del sistema
Los sensores en la fuente de poder van a ayudar a los fabricantes de metal a evitar el dolor de cabeza que implican los consumibles de corta duración, e incluso la explosión de la antorcha.
La tecnología de la actualidad puede detectar el inicio de un estallido de electrodo catastrófico. (Imagine agua deslizándose hacia la antorcha de corte con plasma desde una manguera de aire comprimido y el estallido que ocurriría como resultado. Eso es lo que podría ocurrir si un electrodo está cerca del final de su vida y es forzado más allá de sus límites.) Cuando los sensores notan cambios drásticos en la corriente y un voltaje de arco errático, el control apaga el sistema de inmediato. Esto evita falla de la antorcha, y un tiempo improductivo prolongado asociado con la limpieza después de un estallido.
También se usan sensores para evitar el esfuerzo considerable a que se someten los consumibles cuando el corte con plasma está por terminar de una manera descontrolada, como cuando el proceso de corte con plasma continua aun después de que la antorcha sale del corte en el borde del material. Esto estira el arco, el cual quiere mantener la conexión con el metal, e implica un gran esfuerzo para los consumibles de la antorcha.
En este caso, los sensores notan un aumento abrupto en el voltaje del arco conforme el arco se estira para mantener contacto con el metal. Se detecta correctamente que el arco está a punto de terminar y se inicia una reducción gradual controlada de la corriente. Este tipo de apagado controlado le da al hafnio dentro del electrodo el tiempo que necesita para volver a solidificarse, lo cual ayuda a un aumento importante en la vida del consumible.
5. Manténgase atento
Para aquellos operadores de máquina involucrados en los ciclos de cambio de consumibles antes de los días de los controles modernos, es probable que vigilaran de cerca una medición de desempeño clave. Podría haber sido el número de perforaciones o pies de material cortado. (¡Estas mediciones siguen siendo usadas por el software para determinar el desgaste de los consumibles!) Sin importar lo que fuera, el operador sabía lo que necesitaban monitorear para que la antorcha de plasma se mantuviera cortando como se esperaba.
El surgimiento de los controles modernos formalizó el monitoreo del desgaste de consumibles, quitándole a los operadores parte de la responsabilidad, pero la máquina en sí no puede quitar los consumibles si éstos necesitan cambiarse. Los operadores todavía tienen que seguir involucrados.
Por eso es tan poderosa la combinación de un operador comprometido y controles avanzados en los sistemas de corte con plasma. Por ejemplo, el software de máquina puede calcular en qué parte de un nido es necesario un cambio de consumibles; entonces la máquina puede informarle al operador cuando tiene que estar en la máquina para hacer el cambio. Cuando trabajan al unísono, el sistema de corte con plasma y el operador pueden generar un tiempo productivo máximo de la máquina y resultados de corte de alta calidad.
Sin embargo, la vida en las instalaciones de fabricación de metal está marcada constantemente por el cambio, y eso significa que tanto los humanos como la maquinaria tienen que ser flexibles. Si un trabajo urgente interrumpe el calendario de producción, ese cambio va a alterar no sólo los tiempos de los trabajos subsecuentes, sino también la duración de los consumibles.
Las máquinas están diseñadas para proporcionar datos confiables. El operador necesita averiguar simplemente qué tan recientes son los datos.
6. Perfórelo
Obviamente, no todo mundo tiene una máquina de propósitos múltiples, la cual puede ofrecer fresado, corte, taladrado y marcado. Sin embargo, para quienes la tienen, cuentan con una buena alternativa cuando se trata de hacer agujeros en materiales gruesos. En lugar de perforar el material, lo cual implica el riesgo de botar escoria a la antorcha y dañar posiblemente los consumibles, los operadores de máquina pueden optar por perforar la parte inicial del agujero como un paso de pre-perforación o el agujero completo.
About the Publication
Compañías Relacionadas
subscribe now
FMA Communications ha introducido al mercado la edición en Español de la revista The Fabricator. Esta versión consiste del mismo tipo de artículos técnicos y sección de lanzamientos de nuevos productos que actualmente presentan el personal de primera categoría de Fabricator en Inglés.
start your free subscription- Podcasting
- Podcast:
- The Fabricator Podcast
- Published:
- 05/07/2024
- Running Time:
- 67:38
Patrick Brunken, VP of Addison Machine Engineering, joins The Fabricator Podcast to talk about the tube and pipe...
- Trending Articles
Anidado para la estabilidad del corte láser
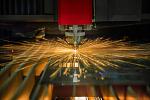
Seguridad en la soldadura desde el inicio
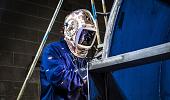
El software guía a los soldadores a través de instrucciones de trabajo
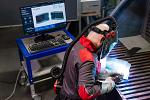
La rueda reduce las fuerzas de empuje/tracción hasta en un 50%

Gafas protectoras diseñadas para trabajadores que necesitan lentes correctivos
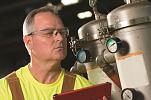
- Industry Events
Laser Welding Certificate Course
- May 7 - August 6, 2024
- Farmington Hills, IL
World-Class Roll Forming Workshop
- June 5 - 6, 2024
- Louisville, KY
Advanced Laser Application Workshop
- June 25 - 27, 2024
- Novi, MI
Precision Press Brake Certificate Course
- July 31 - August 1, 2024
- Elgin,