
The scope of additive manufacturing
November 6, 2023
By
Sukanya Ray Ghosh
Opportunities for leveraging additive manufacturing and 3D printing technologies in Canada.
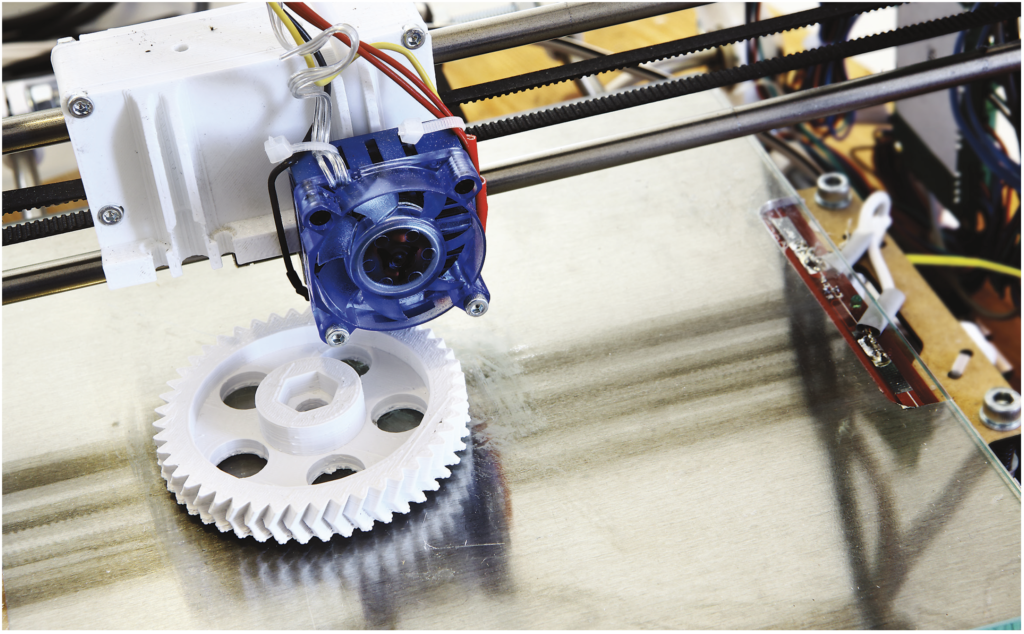
The full potential of additive manufacturing (AM) and 3D printing technologies is yet to be leveraged in Canadian manufacturing facilities. While the concepts are not unfamiliar territory, cost remains a major concern when considering adoption.
However, there are several avenues available with the current versions of AM and 3D printing technology, that can be successfully introduced in manufacturing settings to automate and improve current processes.
Beginning with AM and 3D printing
The “sticker shock” for many AM and 3D printing options is often a turning-away point for many manufacturers, says Mark Kirby, industry training manager at the University of Waterloo. This cost is especially high in metal additive manufacturing, requiring hundreds of thousands of dollars of investment in a capable printer. Plastic 3D printing can be quite affordable, says Kirby. However, most companies are more comfortable investing in tried and tested automation solutions rather than something completely new and expensive.
Where can manufacturers begin when considering AM and 3D printing? Kirby says it could be with the purchase of a plastic 3D printing machine. They can also purchase components from Canadian suppliers through Canada Makes, a not-for-profit industry organization. Kirby suggests that if a manufacturer is not sure whether an AM solution is available for their unique problem, they can even speak to experts in the field through the Canada Makes website’s “Ask the Experts” feature. Canada Makes can be used as a one-stop solution for getting some parts created.
“If you had an idea for, maybe 3D printing that would be interesting, but were not really sure where to start, you could explore the area with Canada Makes without being hard-sold solutions by vendors,” says Kirby.
Manufacturers can also leverage Next Generation Manufacturing Canada’s (NGen) demonstration program to kick-start the project with initial funding support.
Are AM and 3D printing for everyone? The simple answer is yes, says Kirby. There is some solution available for everyone. However, when a manufacturer expresses an interest in these technologies to solve a problem, the first question he asks is why they are interested in the first place.
“I ask them to describe the problem and the current solution they are using. Typically, they share that they use some kind of manufacturing process. If they say the current solution is too expensive, and therefore they need 3D printing solutions, I immediately discourage them. AM and 3D printing are not silver bullets that make you more competitive out of the gate just by replacing one process with another. It is not a good place to start; it is a good place to finish the journey, however,” explains Kirby.
He adds that manufacturers should think how 3D printing can initially help the company save money on existing processes that can be controlled.
A 3D printing operation needs 3D models. Kirby says that the manufacturer should also consider whether they have in-house knowledge of CAD (Computer-Aided Design) to be able to render 3D models efficiently.
3D printing application
Using 3D printing to manufacture machine parts is an application that most manufacturers are aware of. The application can in fact expand to include parts of robots, such as end-of-arm tooling like grippers, tool changers, carton erectors and more.
A Canadian company that specializes in this area is Anubis 3D. Tharwat Fouad, founder and president of the company, explains that it is important to understand the different technologies to leverage them properly in a manufacturing setting.
Fused deposition modelling (FDM) is ideal for small-quantity parts production for prototyping and checking the functionality of a particular assembly.
Fouad shares that there are other technologies in plastic 3D printing that manufacturers are not aware of, such as selective laser sintering (SLS).
“SLS can often provide more durable parts and are repeatable in terms of expectations from strength and mechanical properties, than FDM. If you’re a manufacturer, who’s trying to use AM technology to create complex parts that are available quicker, and sometimes perhaps cheaper, you could look at SLS as an alternative,” he says.
Fouad shares that his company uses SLS technology to create and supply end-of-arm tooling for its customers’ production lines. Sometimes, these are standard Anubis 3D products and sometimes the tools are customized to suit the customer’s needs.
This technology is widely accepted now and considered advantageous over traditional tools, says Fouad.
“One of the main drivers for 3D printed end-of-arm tooling is the collaborative robot space. Collaborative robots require lightweight tools because the payload capacities are limited. Also, these tools need to have some soft features and have certain safety requirements. With a 3D printed tool, we can address those needs much easier than traditional tools,” he explains.
As an example, surface grippers are mounted on robots to pick boxes. With 3D printed options, the grippers can have rounded edges instead of sharp corners. Fouad notes that if someone accidentally hits a metal equivalent, it can hurt them.
Recounting a success story, Fouad shares that they recently converted a company that was using regular surface grippers to 100 percent 3D printed end-of-arm tools. “They were using grippers from a company in France. They converted to 3D printed tools because they now have the flexibility of adding suction cups wherever they want. They also integrated a tool changer as it adds value during changeovers and maintenance. The 3D printed tools are lighter, and they get delivered faster when compared to importing grippers from France.”
Support for the AM journey
NGen’s AM demonstration program is designed to help manufacturers realize the potential of AM technology and identify implementation risks at an early stage.
Frank Defalco, director of member relations and the AM demo program administrator, shares that NGen identifies small- and medium-sized manufacturers and OEMs from within its membership or from referrals from IRAP ITAs that are eligible to participate.
“I set up a meeting with them to determine where they are in their AM journey. This is important because there are myriad reasons why the company is investigating this technology. I ask about their goal. For NGen, the goal is to identify how AM could be a production tool. Sometimes the manufacturers really understand the technology while some manufacturers are very new to it,” explains Defalco.
Defalco and the NGen team help manufacturers identify the most suitable technology and service providers based on their ability to meet AM objectives. The association also facilitates conversations between companies and service providers to ensure that the projects are successful.
“Target the processes instead of parts because you can nearly always find good applications for 3D printing somewhere in the manufacturing process. You will learn a lot. And if it helps you make your parts more efficiently, then you’ve got a return on the investment but you’ve also critically developed knowledge now that you can use for competitive advanced 3D printing. You will use the technology more intelligently,” says Kirby.
Advertisement
- IIC publishes report on digital twin core conceptual models and services
- Rockwell Automation completes acquisition of cybersecurity solutions provider Verve