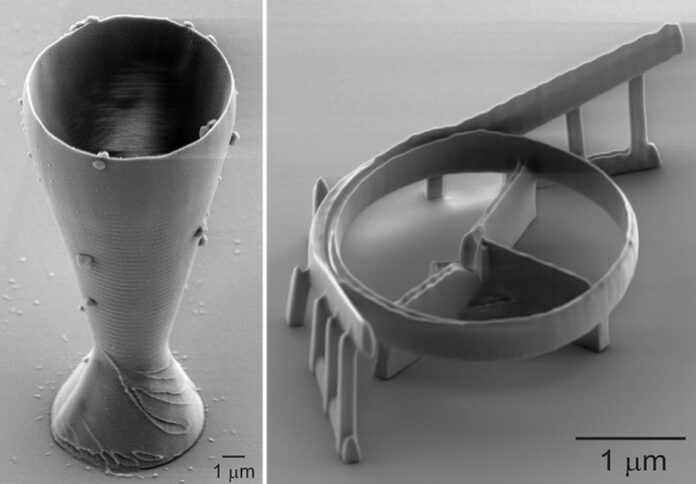
Researchers at Stockholm’s KTH Royal Institute of Technology have 3D-printed what they claim as the world’s smallest wine glass – nearly indistinguishable with the naked eye – with a rim the width of a human hair.
In a news release, the research team said the glass was printed to demonstrate a new simplified approach for manufacturing silica glass structures that can be used in a variety of applications ranging from telecommunications to robotics.
Frank Niklaus, a professor at KTH, claimed that the new method resolves issues including the requirement for thermal treatment when 3D printing crucial silica glass components.
Among other uses, he cited micro-robots that navigate harsh environments, filters and couplers for fibre optic networks, and customised lenses for medical equipment that performs minimally invasive surgery.
In particular, one such fibre optic filter was created, and the researchers demonstrate how the method can directly print gadgets on an optical fibre with a tip that is as fine as a human hair strand.
“The backbone of the internet is based on optical fibres made of glass. In those systems, all kinds of filters and couplers are needed that can now be 3D printed by our technique,” said Kristinn Gylfason, an associate professor of Micro- and Nano-systems at KTH, and co-author of the study.
According to Po-Han Huang, a PhD student at KTH and the study’s principal author, the process dramatically reduces the energy required to 3D-print silica glass, which generally requires heating materials up to several hundred degrees for hours.
“The advantage of our method is there’s no need for thermal treatment and the glass can withstand extreme heat in applications,” Huang noted.
The researchers said another advantage of the process is that silica glass can be made using easily accessible commercial materials.
Huang explained that by eliminating the necessity for thermal treatment, the approach can be employed more widely in a variety of application contexts.
“The concerns when integrating 3D printing methods are usually different for different applications. Even though optimisation of our method is still required for different applications, we believe our method presents an important and necessary breakthrough for 3D glass printing to be used in practical scenarios,” he remarked.